Understanding Manufacturing Process Flow Software
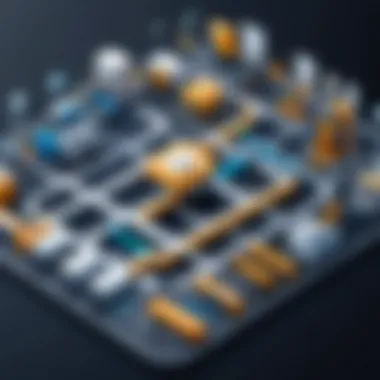
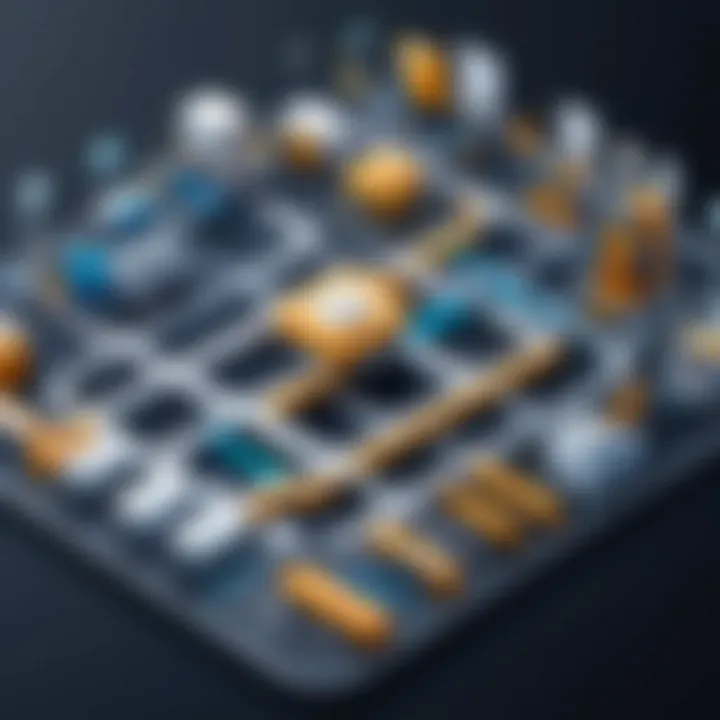
Intro
The manufacturing industry operates with intricate processes that require precision and efficient management. In such an environment, manufacturing process flow software emerges as a crucial tool aimed at optimizing operations. Understanding how this software functions can significantly benefit organizations seeking to enhance productivity and reduce waste.
This article examines various aspects of manufacturing process flow software, its significance in modern manufacturing settings, the components involved, and its impact on operational efficiency. By delving into its features, benefits, and requisite integration strategies, readers will gain valuable insights into selecting the right solution for their specific needs. The analysis also highlights potential challenges organizations may encounter during implementation and offers tactical approaches to mitigate these hurdles.
Thus, our aim is to provide industry advisors and decision-makers with essential knowledge that can facilitate the proactive improvement of manufacturing processes.
Prolusion to Manufacturing Process Flow Software
In an increasingly complex manufacturing landscape, organizations are turning to sophisticated tools to manage operations efficiently. Manufacturing Process Flow Software bridges the gap between raw materials and finished products. It streamlines processes, enhances visibility, and promotes collaboration amongst teams. By utilizing such software, companies can improve productivity and make informed decisions.
Definition and Overview
Manufacturing Process Flow Software refers to digital tools designed to facilitate and optimize workflows in manufacturing settings. These applications help track each stage of production, from initial design to final assembly. Such software integrates various functions, including task assignment, scheduling, and resource allocation. It provides a holistic view of the entire manufacturing process, enabling managers to identify bottlenecks and deficiencies.
The core objective is to enhance efficiency. This allows manufacturers to meet customer demands more effectively while minimizing waste and operational costs. Key functions often include visual mapping of workflows, real-time data tracking, and automated reporting.
Evolution of Manufacturing Software Solutions
The development of manufacturing software solutions has been shaped by technological advancements and the changing needs of the sector. In the early stages, software primarily focused on basic inventory management and data entry tasks. As competition intensified and the demand for efficiency increased, solutions evolved significantly.
With the rise of Industry 4.0, terms like IoT (Internet of Things), AI (Artificial Intelligence), and cloud computing have become buzzwords. Each of these elements contributes toward creating smarter, more connected manufacturing systems. Today, manufacturing process flow software not only automates processes, but also facilitates predictive analytics and real-time dashboard insights. This modernization allows for agile response to market changes, fostering a more dynamic production environment.
Modern manufacturing requires agility and precision; process flow software is not just a tool, but a strategic asset.
As businesses recognize the need for adaptable systems, the evolution of such software continues. The latest solutions prioritize user experience, offering intuitive interfaces that ensure smooth adoption among staff. Companies can now leverage advanced analytics and integration with other tools, establishing a cohesive manufacturing ecosystem.
Key Components of Manufacturing Process Flow Software
In todayβs competitive manufacturing landscape, having robust process flow software is crucial. The right software can change how companies manage their workflows, handle data, and interact with users. Thus, understanding the key components of manufacturing process flow software provides insight into its functionality and potential benefits.
Workflow Management
Workflow management is one of the core elements of manufacturing process flow software. It allows organizations to define, design, and automate their processes seamlessly. Efficient workflow management can lead to more predictable outcomes and helps eliminate bottlenecks. This component is essential because it assists in tracking tasks, setting deadlines, and managing resources effectively.
- Task Automation: Automating routine tasks saves time. For instance, instead of manually assigning tasks, software can route them automatically based on predetermined criteria.
- Monitoring Progress: Real-time tracking capabilities enable managers to see the status of operations at a glance, leading to better decision-making.
- Collaboration Tools: Many software solutions offer features that facilitate collaboration, allowing teams to work together more efficiently.
Investing in solid workflow management capabilities enhances operational efficiency and reduces the risk of human error.
Data Management Capabilities
Data management capabilities are integral to manufacturing process flow software. The ability to collect, analyze, and store data transparently allows businesses to derive actionable insights. Data drives decisions in manufacturing, making this component vital.
- Centralized Data Repository: Having a single source of truth prevents discrepancies and errors, ensuring all teams work with the same information.
- Advanced Analytics: With built-in analytics, organizations can monitor key performance indicators (KPIs), identify trends, and improve processes over time.
- Data Security: Protecting sensitive information is crucial. Effective software solutions implement robust security measures to safeguard data.
These data management capabilities not only enhance operational efficiency but also support strategic aims by providing clarity on performance metrics.
User Interface Design
A well-structured user interface design ensures systems are user-friendly and efficient. Poor UI can lead to frustration among users, making training difficult and adoption slow. Therefore, investing in intuitive design is essential for effective software.
- Simplicity and Clarity: An interface that is easy to navigate helps users understand the softwareβs functionalities quickly, reducing the learning curve.
- Responsive Design: Software should be accessible on various devices, enabling users to interact with the system from multiple locations, which is increasingly vital in today's mobile work environments.
- Customization Options: Customizable interfaces provide users the ability to tailor the software to their specific needs and preferences, enhancing overall satisfaction and usability.
Benefits of Implementing Process Flow Software
Implementing manufacturing process flow software provides a multitude of advantages that can directly impact overall operational performance. Understanding these benefits helps in justifying the investment and change management needed for such systems. When businesses adopt these technologies, they typically unlock significant improvements in efficiency, visibility, and cost effectiveness. This section outlines these benefits in detail, aiming to shed light on the concrete gains organizations can achieve.
Increased Efficiency and Productivity
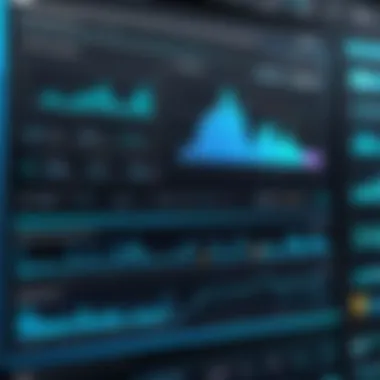
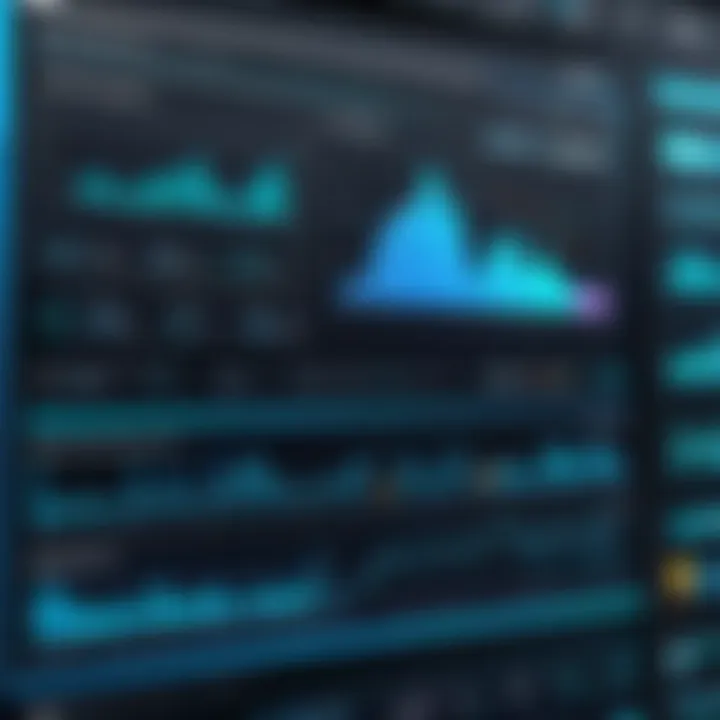
One of the most obvious benefits of process flow software is the enhancement of efficiency and productivity within manufacturing operations. By automating repetitive tasks, such software reduces the need for manual intervention. This not only speeds up various processes but also minimizes the risk of human error. For instance, real-time tracking of production stages enables quicker decision-making. When employees spend less time on mundane activities, they can focus on more strategic efforts, ultimately leading to increased output.
Moreover, the software allows for better resource allocation. By understanding which parts of the process are optimized and which are lagging, managers can direct resources where they are needed most. This data-driven approach fosters a culture of continuous improvement, as teams can quickly address inefficiencies as they arise.
Enhanced Visibility and Transparency
Visibility across all manufacturing processes is critical for effective management. Process flow software provides a clear and comprehensive view of various stages of production. This transparency is vital not only for internal stakeholders but also for external entities such as suppliers and customers. Stakeholders can monitor progress and quickly identify any potential bottlenecks.
Enhanced visibility directly contributes to better compliance as well. With easy access to documentation and reporting tools, businesses can streamline regulatory processes and maintain high standards. In turn, this leads to greater trust among partners and clients, reinforcing the business's reputation in a competitive marketplace.
"Companies with higher visibility through process flow software often experience reduced risk of supply chain disruptions."
Cost Reduction Opportunities
The implementation of manufacturing process flow software can uncover various cost reduction opportunities. First, improvements in workflow efficiency tend to reduce production time, which translates to lower operational costs. Companies can achieve more with the same resources, a crucial factor in maintaining a healthy profit margin.
Secondly, by improving inventory management through better forecasting and real-time data analysis, organizations can significantly cut excess stock and associated costs. These tools help in aligning production closely with demand, thereby reducing waste and storage costs.
In addition to direct cost savings, the long-term benefits of improved processes lead to a higher return on investment. As efficiency grows and operational costs decline, the financial benefits begin to compound, ensuring sustainable growth.
Challenges in Manufacturing Process Flow Software Adoption
Adopting manufacturing process flow software comes with distinct challenges that need careful consideration. Addressing these issues is vital for achieving a smooth transition and fully realizing the software's benefits. By understanding these challenges, organizations can prepare better and design effective strategies for successful implementation.
Integration with Existing Systems
Integration is often one of the most significant hurdles faced in the adoption of new manufacturing process flow software. Existing systems, such as Enterprise Resource Planning (ERP) and Supply Chain Management (SCM) tools, may be deeply interwoven into daily operations. If the new software does not seamlessly integrate with what is already in place, it can result in data silos and inefficient workflows.
To ensure successful integration, thorough planning and assessment are necessary. Here are some considerations:
- Compatibility: Ensure that the new software is compatible with current systems.
- Data Migration: Develop a robust plan for migrating data from old systems to the new one. This includes verifying data integrity during the transfer.
- Real-Time Sync: The ability to synchronize data in real-time can enhance functionality, but it also requires careful setup.
Recognizing and planning for these integration issues can help mitigate risks associated with system adoption.
User Resistance to Change
Another challenge is the potential resistance from users. Employees often become accustomed to existing processes and tools. Introducing new software may be met with skepticism or reluctance, as staff members may fear that they will not adapt quickly or well enough.
To combat resistance, organizations can:
- Involve Employees Early On: Engaging users in the selection and implementation process fosters a sense of ownership. Their input can also help in selecting the right software.
- Communicate Benefits Clearly: Thoroughly explain how the new software will make their tasks easier and improve overall efficiency.
- Provide Incentives: Sometimes, offering incentives for early adopters can motivate users to embrace the change.
Training and communication become pivotal in helping users see the value of the software.
Training and Skill Gaps
Finally, addressing training and skill gaps is essential. Many organizations may overlook the need for comprehensive training programs. If employees are unsure how to use the software it can lead to frustration and decreased productivity.
Companies should consider the following steps:
- Comprehensive Training Programs: Develop structured training sessions that cater to varying skill levels.
- Onboarding Support: Providing ongoing support post-implementation aids in reinforcing training and addressing any immediate concerns.
- Resource Availability: Make sure users have easy access to training materials, manuals, or helpdesk assistance when needed.
Training does not end after the initial rollout; it is a continuous journey aimed at enhancing proficiency.
In summary, while adopting manufacturing process flow software presents challenges, proper planning, user engagement, and training can smoothen the transition.
Choosing the Right Manufacturing Process Flow Software
Choosing the right manufacturing process flow software is a pivotal decision for any organization wishing to enhance operational efficiency. This process is not simply about selecting the latest technology; it involves comprehensively understanding the specific needs of the business and evaluating various options that can meet those requirements. The right software can drive significant improvements in productivity, accuracy, and overall process management.
In this section, we will explore essential elements to consider when selecting the appropriate manufacturing process flow software. The goal is to help decision-makers understand what features, vendor support, and scalability options they should prioritize to align with their strategic objectives.
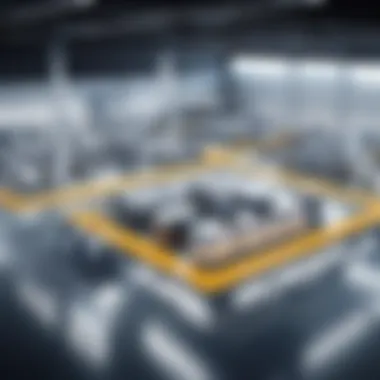
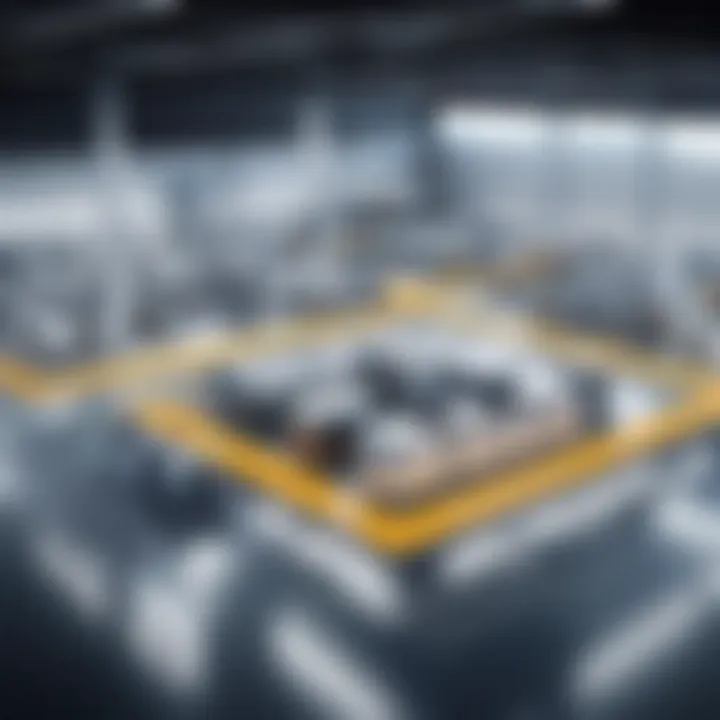
Key Features to Consider
When choosing manufacturing process flow software, certain features stand out as crucial for ensuring effectiveness and ease of use:
- Workflow Automation: The software should enable automatic routing of tasks and documents, reducing manual input.
- Real-Time Data Analytics: It is vital to have tools that provide insights into operations in real time, allowing for quicker decision-making.
- Integration Capabilities: The software must integrate seamlessly with existing systems, such as ERP or SCM tools, to avoid data silos and improve operational coherence.
- User-Friendly Interface: A simple and intuitive interface helps ensures engagement among employees and speeds up the learning curve.
- Reporting Features: Strong reporting tools assist management in understanding and optimizing manufacturing processes.
Focusing on these key features will help organizations select software that effectively supports their manufacturing goals.
Vendor Reputation and Support
The choice of vendor is equally as significant as the software itself. A well-established vendor often provides better services and a more robust product. Considerations include:
- Market Presence: Research vendor history and market share as indicators of reliability.
- Customer Reviews: Look for testimonials and case studies from other users, as this can provide insights about the vendor's performance.
- Technical Support: Assess available support options, such as training resources, help desks, and online communities. A responsive support system is crucial during implementation and in the ongoing usage of software.
A trusted vendor not only delivers quality software but also becomes a partner in the journey toward improved manufacturing processes.
Scalability and Customization Capabilities
Scalability is an essential consideration when selecting manufacturing process flow software. As businesses grow, their operational needs evolve. Software that cannot scale may become a bottleneck. Thus:
- Growth Potential: Determine if the software can accommodate increased production volumes or complexity without significant upgrades.
- Customization Options: Assess how easily the software can be tailored to meet unique operational requirements. Customizable solutions can provide significant advantages in aligning processes with business objectives.
Integration of Manufacturing Process Flow Software with Other Systems
The integration of manufacturing process flow software with other systems is critical for streamlining operations in a modern manufacturing environment. This kind of integration creates a cohesive ecosystem that allows for improved communication and data exchange between different functions of an organization. When various systems work seamlessly together, it leads to better visibility, accurate data reporting, and enhanced decision-making capabilities. In this section, various key integrations are discussed.
Enterprise Resource Planning (ERP) Systems
Integrating manufacturing process flow software with Enterprise Resource Planning (ERP) systems is one of the foundational steps for any manufacturer. ERP systems manage and streamline business processes, including inventory control, order management, accounting, and human resources. By connecting this software to process flow applications, manufacturers can ensure data consistency across departments. This connection eliminates data silos that often lead to discrepancies and errors in reporting.
Benefits of this integration include:
- Real-time data: Updates in any production step reflect immediately in the ERP system.
- Enhanced forecasting: Improved forecasting is possible with accurate data on production capacity and resource availability.
- Streamlined reporting: Automated reporting is made easier, reducing the time spent collecting and analyzing data.
Supply Chain Management (SCM) Tools
The integration of manufacturing process flow software with Supply Chain Management (SCM) tools enhances coordination and efficiency throughout the supply chain. SCM tools help manage the flow of goods from suppliers to customers, tracking inventory, shipments, and supplier performance. When these systems communicate effectively, manufacturers can respond swiftly to changes in demand or supply interruptions.
Some specific advantages of integrating these two systems are:
- Improved demand planning: Access to production data allows for more accurate demand forecasting.
- Lower lead times: With real-time access to information, delays can be minimized, leading to faster delivery times.
- Supplier collaboration: Enhanced communication with suppliers helps solve issues quickly and amicably.
Real-Time Monitoring Solutions
Real-time monitoring solutions play a vital role in manufacturing. These systems provide insights into equipment performance, production rates, and operational efficiency through data-driven approaches. When integrated with manufacturing process flow software, real-time monitoring enables companies to identify trends and anomalies as they occur, not after the fact.
Key benefits of this integration include:
- Proactive management: Immediate alerts for production issues allow for swift corrective actions.
- Optimization opportunities: Continuous monitoring provides insights for optimization mission, such as reducing waste and enhancing productivity.
- Data-driven decisions: Accurate real-time data assists decision-makers in refining strategies and operations effectively.
Effective integration of manufacturing process flow software not only enhances isolated functionalities but propels comprehensive operational excellence across the entire organization.
Case Studies of Successful Implementation
Case studies serve as vital tools in understanding the practical applications of manufacturing process flow software. They showcase real-life scenarios where this technology has been deployed, highlighting both successes and challenges experienced by diverse organizations. Analyzing these cases enables decision-makers and IT professionals to glean insights that can shape future implementation strategies.
This section will focus on two manufacturing companies that successfully integrated process flow software. By examining their experiences, we can identify key factors that contributed to their success and draw lessons applicable to other sectors.
Manufacturing Company A
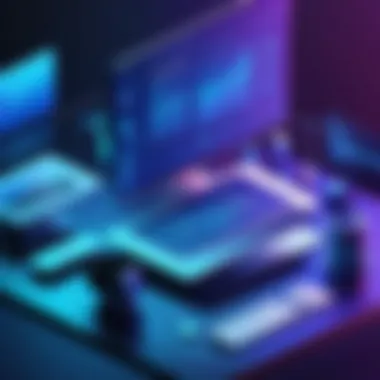
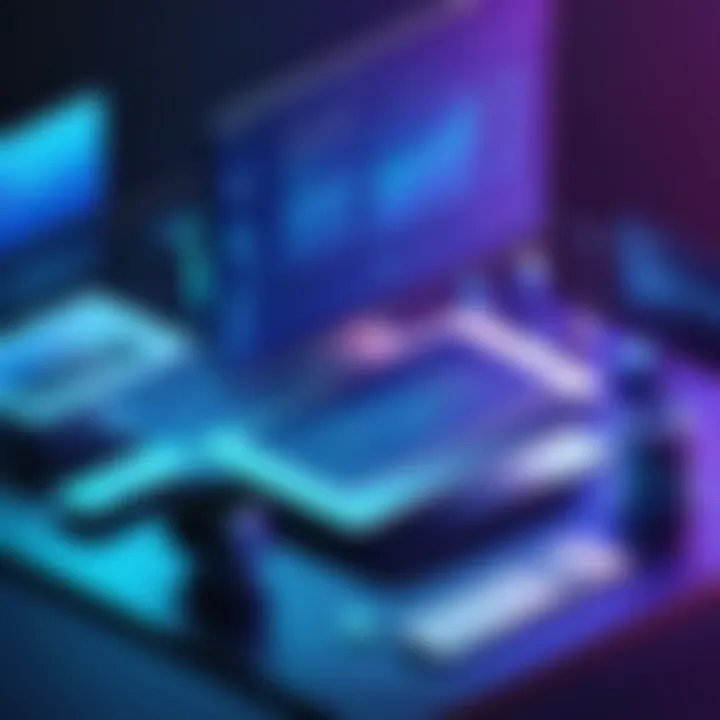
Manufacturing Company A, a leading player in the automotive industry, faced challenges in streamlining its operations due to fragmented processes. Each department operated in silos, making it difficult to achieve cohesive workflow management. The organization decided to implement Siemens Opcenter, a robust process flow software, to address these inefficiencies.
Upon implementation, Manufacturing Company A saw significant improvements. Key benefits included:
- Reduced cycle times: Transparency across departments allowed for quicker decision-making.
- Enhanced collaboration: Centralized data fostered communication among teams.
- Real-time analytics: With better data management, the company could track performance metrics instantly.
The transition, however, was not without hurdles. Initial resistance from staff was prevalent, and comprehensive training sessions were necessary to ease the adaptation process. Nevertheless, after a focused effort, the company reported a 20% increase in overall productivity within the first year of using the software.
Manufacturing Company B
Manufacturing Company B, specializing in consumer electronics, was experiencing issues with inventory management. They opted for Oracle NetSuite to integrate process flow software into their operations. This decision came after assessing the growing complexities in inventory tracking and supplier relationships.
The installation of Oracle NetSuite allowed Manufacturing Company B to:
- Improve inventory accuracy: Automated tracking reduced errors significantly.
- Streamline supplier communication: Enhanced visibility strengthened relationships with suppliers.
- Accelerate order processing: Efficiency increased as data flowed seamlessly across departments.
A challenge faced during the implementation was ensuring data migration from their old legacy systems. They addressed this by establishing continuous support frameworks, helping employees acclimate to the new system. In the end, the company reduced order fulfillment times by 30%, demonstrating the real impact of effective process flow software integration.
Case studies provide invaluable insights into real-world applications, revealing both the benefits and challenges of adopting manufacturing process flow software.
These two case studies illustrate the transformative potential of manufacturing process flow software when implemented thoughtfully. By analyzing specific details, others in the industry can adapt strategies that suit their unique environments.
Future Trends in Manufacturing Process Flow Software
The manufacturing sector is experiencing rapid changes due to technological advances. These innovations are not just evolutionary; they are revolutionary. Understanding these future trends is crucial for companies aiming to stay competitive and efficient. The application of new technologies is transforming how process flow software integrates within manufacturing operations. Two of the most significant trends in this area are Automation and Artificial Intelligence, along with Cloud-Based Solutions.
Automation and Artificial Intelligence
Automation combined with artificial intelligence is reshaping the landscape of manufacturing. These technologies offer not just efficiency but also precision and consistency in production processes. By automating routine tasks through robotics, manufacturers can minimize human error, thus enhancing overall output quality.
Moreover, artificial intelligence allows for advanced analytics. This means software systems can learn from data, predict outcomes, and optimize workflows autonomously. For example, AI algorithms can analyze production data to identify bottlenecks in real-time, allowing for immediate resolution.
The benefits of integrating automation and AI into process flow software include:
- Cost Savings: Reducing labor costs while increasing throughput.
- Improved Decision-Making: Leveraging data-driven insights to make quicker and better decisions.
- Quality Control: Ensuring high standards by monitoring processes continuously.
These technologies also find application in predictive maintenance, where AI models foresee equipment failures before they occur, thus preventing costly downtime.
Cloud-Based Solutions
Cloud-based solutions are another trend revolutionizing manufacturing process flow software. These systems offer flexibility and scalability that traditional solutions often cannot match. By utilizing the cloud, organizations can access their software from anywhere, facilitating better collaboration among teams spread across different locations.
One of the most significant advantages of cloud-based solutions is cost efficiency, especially for small to medium-sized businesses. With subscription-based models, companies avoid hefty upfront investments in hardware and software. Instead, they pay as they use, making budgeting easier.
Furthermore, cloud solutions enable seamless integration with other platforms. For example, when combined with Internet of Things (IoT) technologies, manufacturers can achieve greater insights and real-time data monitoring. The characteristics of cloud-based solutions include:
- Data Storage and Access: Secure, centralized data management without physical limits.
- Enhanced Collaboration: Remote access allows teams to work together in real-time irrespective of their location.
- Regular Updates: Automatic software updates ensure businesses are using the latest functionalities without any manual effort.
"The shift towards cloud technologies also drives greater agility and responsiveness, which are critical in today's fast-paced markets."
These trends are not mere fads but essential trajectories that manufacturing process flow software must align with. Companies that recognize and invest in these advancements stand to gain a significant competitive advantage.
Closure
In the landscape of manufacturing, the integration of process flow software represents a fundamental shift toward enhanced operational efficiency. The significance of this software cannot be overstated. As manufacturers face growing pressures to improve productivity while reducing costs, understanding and implementing manufacturing process flow software emerges as a critical strategy.
Summary of Key Points
- Overview of Process Flow Software: This software serves to streamline operations by providing a structured approach to managing workflows within the manufacturing environment.
- Key Components: Effective software includes essential features such as workflow management, robust data management, and intuitive user interface designs, which facilitate ease of use and comprehensive data analysis.
- Benefits: Organizations that implement such software are likely to see increased efficiency, enhanced visibility into operations, and opportunities for significant cost reductions.
- Challenges: However, the adoption of this software comes with challenges, including potential integration issues with existing systems and resistance from users accustomed to traditional methods.
- Future Trends: Looking ahead, trends like automation and cloud-based solutions indicate a shift toward more agile and responsive manufacturing processes.
Final Recommendations
For decision-makers considering the adoption of manufacturing process flow software, several recommendations stand out:
- Assess Your Needs: Begin by evaluating the unique requirements of your manufacturing processes to identify software that aligns closely with your operational objectives.
- Choose Wisely: Pay attention to software features that provide the best fit for your organization's workflows, data requirements, and user interface preferences.
- Prioritize Training: Invest in comprehensive training programs for your staff to mitigate resistance to change and address skill gaps.
- Plan for Integration: Consider how the new software will integrate with existing systems and be prepared to allocate resources for potential adjustments.
Implementing process flow software is not merely a technical upgrade but a strategic move that can redefine the efficiency and responsiveness of manufacturing operations. By focusing on the factors elaborated in this article, organizations can make informed decisions that lead to sustainable improvement.