Understanding Maintenance Management Programs
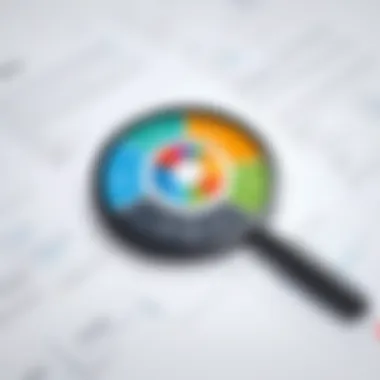
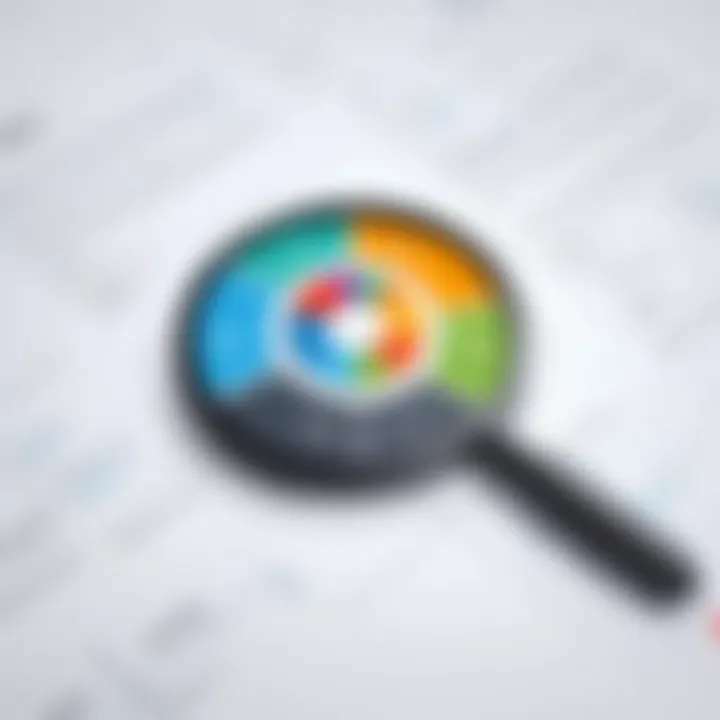
Intro
Maintenance management programs are essential frameworks for organizations seeking to optimize their operational efficiency and prolong asset life. These programs help in planning, executing, and reviewing maintenance activities to ensure that equipment and systems function optimally without unnecessary delays or expenses. With rapid advancements in technology, the integration of software tools for maintenance management has become critical. This guide explores the various aspects of maintenance management programs, including definitions, importance, implementation strategies, and the impact of modern technology.
Software Overview
In todayโs digital era, maintenance management software plays a pivotal role in facilitating seamless operations. Such software assists organizations in managing their assets, scheduling maintenance tasks, and tracking performance metrics. This transformative approach enhances not just routine maintenance but also ensures that preventive measures are in place to avert unforeseen breakdowns.
Brief Description of Software
Maintenance management software encompasses a suite of tools that help streamline the maintenance process. These applications often include features for inventory management, work order management, and reporting functionalities. By consolidating all maintenance-related tasks within one software environment, companies can significantly reduce manual errors and improve communication among teams.
Key Features and Functionalities
Key features of maintenance management software typically include:
- Work Order Management: Automation of work orders helps prioritize tasks and assign them to the right personnel.
- Asset Tracking: Facilities may track equipment usage, downtime, and maintenance history.
- Inventory Control: Managing spare parts and supplies efficiently reduces costs and prevents stockouts.
- Reporting and Analytics: Provides insights into performance through various metrics and dashboards.
- Mobile Accessibility: Allows field technicians to access information and update task statuses in real-time.
These functionalities collectively enhance the organizationโs ability to maintain assets effectively and efficiently.
Detailed Comparison
Choosing the right maintenance management software involves analyzing various options available on the market.
Comparison with Competitors
When comparing different software solutions, it is crucial to consider factors such as ease of use, scalability, support, and the specific needs of your organization. Some popular software choices are:
- CMMS: Computerized Maintenance Management System focuses primarily on managing maintenance operations.
- EAM: Enterprise Asset Management offers a broader scope, encompassing asset lifecycle management.
Each of these platforms comes with its unique strengths and weaknesses, which must be evaluated according to organizational requirements.
Pricing Structure
The pricing structure for maintenance management software can vary widely based on the features and functionalities offered. Some may provide tiered pricing models based on user numbers or specific functionalities. For instance:
- Basic plans might start at an affordable monthly subscription for small teams.
- Advanced plans may include comprehensive features suitable for larger enterprises and often come at a premium.
Understanding your budget and the requisite features is vital in making an informed decision.
"Investing in maintenance management software is not just an expense, but an investment toward sustainable operational efficiency."
By carefully assessing features, pricing, and specific organizational needs, decision-makers can select a maintenance management program that enriches decision-making processes and enhances overall efficiency.
Intro to Maintenance Management Programs
In today's competitive business landscape, understanding maintenance management programs is crucial for achieving sustainable operational efficiency. Maintenance management entails a systematic approach to overseeing maintenance activities, ensuring that assets remain in optimal working condition. This article delves into its significance, providing insights into the various types of programs, their components, and the role technology plays in modern maintenance strategies.
Definition and Overview
Maintenance management programs can be defined as structured frameworks for planning, executing, and monitoring maintenance activities. They encompass a wide range of practices and methodologies designed to minimize downtime and maximize asset reliability. Organizations often tailor these programs to their specific operational needs, aligning them with overall business objectives. The core elements of these programs typically include preventive maintenance, corrective maintenance, and predictive maintenance. Each of these elements contributes to a comprehensive strategy that enhances the lifespan of equipment and reduces maintenance costs.
Importance in Operations
The importance of maintenance management programs extends well beyond mere equipment upkeep. Effective maintenance directly impacts productivity, safety, and profitability. Organizations that prioritize maintenance management often experience fewer unexpected failures, leading to improved throughput and reduced operational interruptions. Moreover, robust maintenance strategies contribute to regulatory compliance and uphold safety standards, both vital for any organization.
Organizations that invest in maintenance management see a marked improvement in their operational efficiency and overall asset management.
Incorporating maintenance management into day-to-day operations also aids in informed decision-making. With accurate data tracking and reporting, decision-makers can identify trends, allocate resources wisely, and propose adjustments to maintenance schedules based on real-time performance metrics. This ensures a proactive approach, allowing businesses to remain agile in addressing unexpected challenges. Overall, understanding maintenance management programs is not just beneficial but essential in todayโs dynamic market environment.
Types of Maintenance Management Programs
Understanding the various types of maintenance management programs is critical for organizations striving for operational excellence. Each program serves a unique purpose and offers distinct benefits, which contributes to the overall efficiency of operations.
Preventive Maintenance
Preventive maintenance focuses on scheduled tasks aimed at preventing equipment failures before they occur. Organizations implement regular inspections, cleaning, lubrication, and parts replacement to maintain optimal functionality. The clear advantage of preventive maintenance is its ability to minimize unexpected downtime, which can lead to considerable costs in both time and money.
- Consistency: Regular inspections lead to predictable outcomes and performance.
- Cost-Effectiveness: Saving from unplanned repairs and extending equipment life reduces overall expenses.
- Safety: Regular maintenance ensures safer operating conditions for employees.
Implementing a preventive maintenance strategy requires careful planning. Maintenance schedules should be tailored to the unique needs and operations of the organization.
Predictive Maintenance
Predictive maintenance uses data analytics to determine the condition of equipment and predict when maintenance should occur. The integration of technology, like sensors and IoT devices, is essential in this approach. By monitoring conditions in real time, organizations gain insights that allow them to act before a failure occurs.
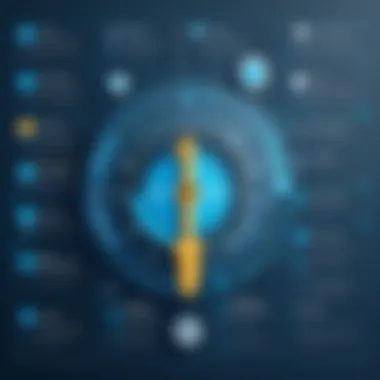
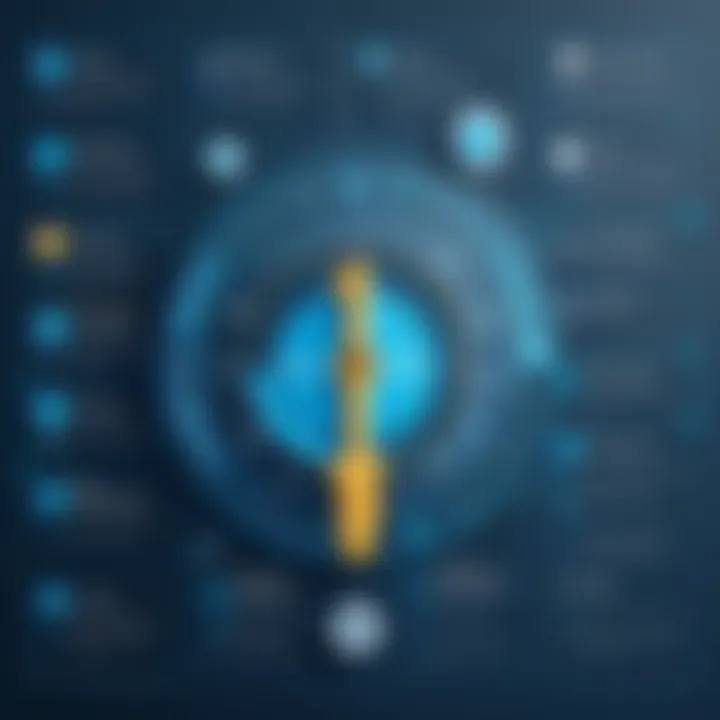
- Data-Driven: Decision-making backed by analytics leads to better maintenance planning.
- Reduced Downtime: Maintenance is performed only when necessary, reducing unproductive time.
- Efficient Resource Use: Fewer man-hours spent on unnecessary maintenance tasks.
This strategy requires a strong investment in technology and personnel training, making it crucial to consider both initial costs and long-term benefits.
Corrective Maintenance
Corrective maintenance is reactive; it addresses equipment failures after they occur. While this approach is often seen as less desirable, it can be effective in certain situations. Organizations may choose corrective maintenance when equipment is not used frequently, and the costs of unexpected failures are manageable.
- Flexibility: Adaptable to varying levels of equipment usage.
- Immediate Response: Allows for focus on urgent repairs rather than preventive actions.
- Simplified Approach: Requires fewer resources compared to preventive strategies.
However, organizations need to be cautious. Relying solely on corrective maintenance can lead to unexpected downtime and increased repair costs if not managed wisely.
Condition-Based Maintenance
Condition-based maintenance is a hybrid approach that combines elements from both preventive and predictive strategies. Here, maintenance actions are dictated by the real-time condition of the equipment. This method focuses on maintenance when certain predefined thresholds are met, ensuring a more efficient allocation of resources.
- Real-Time Monitoring: Allows for adjustments based on the actual state of equipment.
- Optimal Resource Management: Reduces unnecessary maintenance interventions.
- Increased Equipment Lifespan: Timely interventions based on conditions can prolong asset life.
Implementing a condition-based maintenance program necessitates a robust technology infrastructure to track and analyze equipment metrics continuously.
The choice of maintenance management program significantly affects operational efficiency, cost management, and overall equipment longevity, underscoring the need for a tailored approach that harnesses the strengths of each methodology.
Key Components of Maintenance Management Programs
The effectiveness of a maintenance management program relies heavily on several core components. These elements are vital for achieving organizational goals, optimizing operational efficiency, and prolonging the lifespan of assets. Without a comprehensive understanding of these components, organizations may face increased downtime, excessive costs, and reduced productivity.
Asset Management
Asset management is the cornerstone of any maintenance program. It involves tracking the physical and functional characteristics of all assets within an organization. Having a robust asset management strategy helps in knowing where assets are located, their condition, and their maintenance history. This information is crucial for making informed decisions about repairs, replacements, and upgrades.
Benefits of effective asset management include:
- Improved asset utilization
- Enhanced performance monitoring
- Better compliance with regulatory standards
Tools for asset management often include Computerized Maintenance Management Systems (CMMS) which allow organizations to streamline this process. Accurate asset management can lead to substantial cost savings and more effective resource allocation.
Work Order Management
Work order management is essential for organizing and prioritizing maintenance tasks. This process ensures that the right work is being done at the right time. Each work order serves as an instruction for maintenance activities, detailing the tasks, necessary materials, and timelines for completion.
Key aspects of work order management are:
- Tracking progress of maintenance tasks
- Reducing response times
- Documenting maintenance history
A well-structured work order system not only organizes the workflow but also provides valuable data for analyzing maintenance activities over time. This can aid in forecasting maintenance needs and improving future planning.
Inventory Control
Inventory control in maintenance management involves overseeing the stock of spare parts and tools required for maintenance activities. An efficient system for inventory management is crucial to avoid both overstocking and stockouts.
Considerations for effective inventory control include:
- Monitoring usage rates of parts
- Establishing reorder points
- Along with optimizing storage space
The integration of inventory control with maintenance management software can provide real-time data on inventory levels. This integration enhances responsiveness to maintenance needs and helps manage costs associated with excess inventory.
Scheduling and Planning
Scheduling and planning are significant in ensuring that maintenance work is performed efficiently and without unnecessary delays. This component encompasses the organization of maintenance tasks, allocating resources effectively, and ensuring minimal disruption to operations.
Benefits of effective scheduling include:
- Increased uptime of assets
- Optimized workforce allocations
- Better anticipation of maintenance needs
Creating a well-defined schedule allows companies to balance preventive and corrective maintenance while aligning with operational priorities. Technology, including scheduling software, plays a vital role in facilitating these processes.
Effective maintenance management components not only streamline operations but also enable organizations to achieve targeted efficiency and cost savings.
The Role of Technology in Maintenance Management
In the landscape of maintenance management, technology emerges as a cornerstone for optimizing operations. The integration of advanced tools and systems not only streamlines processes but also significantly enhances decision-making. With the push for operational efficiency, leveraging technology is no longer a luxury but a necessity. This section delves into how various technological advancements, particularly CMMS, IoT, and mobile solutions, shape maintenance practices positively.
CMMS Software
Computerized Maintenance Management System (CMMS) software stands at the forefront of maintenance management technology. CMMS functionalities include scheduling preventive maintenance, tracking work orders, and managing inventory. This software allows organizations to gather data on asset performance and maintenance history, which in turn aids in making informed decisions.

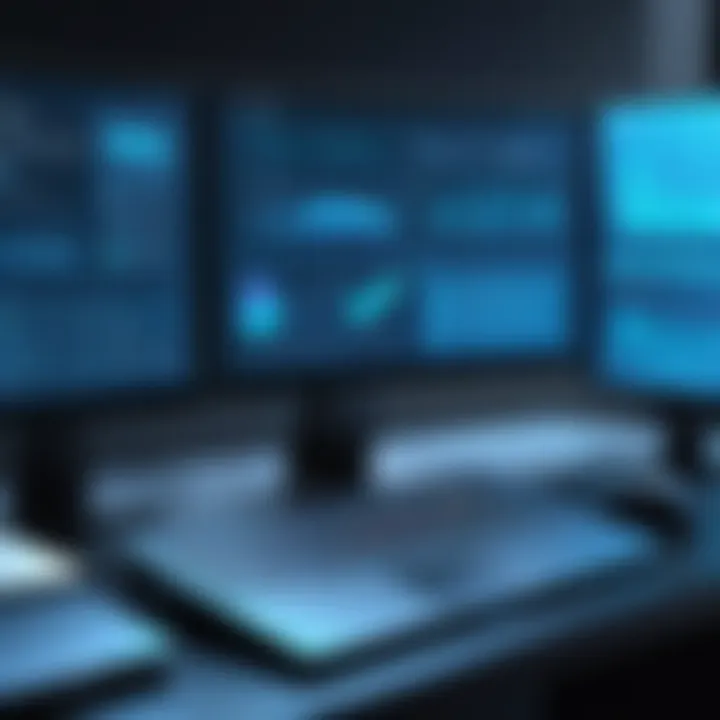
The benefits of CMMS are notable. For instance, by using a CMMS, companies can:
- Reduce downtime through effective scheduling.
- Generate reports for performance analysis and planning.
- Enhance compliance with safety regulations.
The successful implementation of a CMMS can lead to a more organized maintenance team and improved asset life cycles. Organizations must consider factors such as user-friendliness, customization options, and support services when selecting a CMMS.
IoT and Data Integration
The Internet of Things (IoT) plays a critical role in the evolution of maintenance management. It connects physical devices to the internet, enabling real-time data collection and monitoring. Such integration facilitates condition-based maintenance and predictive analytics. This way, maintenance teams can identify potential equipment failures before they happen.
Key advantages of utilizing IoT include:
- Real-time monitoring of equipment health.
- Enhanced data analytics for decision support.
- Lower operational costs by reducing emergency repairs.
Implementing IoT solutions requires thoughtful consideration regarding cybersecurity and data management. Organizations must ensure they have robust systems in place to protect sensitive information and effectively analyze the vast amounts of data generated.
Mobile Maintenance Solutions
Mobile maintenance solutions represent a significant innovation in maintenance management. These solutions empower technicians with real-time access to data and work orders through mobile devices. This mobility not only increases efficiency but also improves communication in the field.
Advantages of mobile maintenance solutions include:
- Increased technician productivity by minimizing downtime.
- Enhanced accuracy when capturing data and reporting issues.
- The ability to receive updates and instructions instantaneously.
For companies considering adoption, it's essential to evaluate app usability and integration capabilities with existing systems. Having a user-friendly interface can significantly impact technician adoption and overall effectiveness.
"The future effectiveness of maintenance management rests on how well organizations embrace and implement technology."
Implementation Strategies
Implementing a maintenance management program is a crucial step for any organization aiming to enhance its operational efficiency. This section digs into the essential strategies for putting such programs into practice, identifying organizational needs, selecting suitable programs, and focusing on training and development.
Assessing Organizational Needs
Understanding the specific needs of an organization is the cornerstone of an effective maintenance management program. This initial assessment should evaluate current operations, existing technologies, and employee competencies. A thorough analysis entails gathering data on equipment performance, maintenance costs, and historical downtime incidents. Engaging with various departments can provide valuable insights as well.
Key elements to consider include:
- Current Equipment Status: Evaluate age, condition, and performance metrics.
- Workforce Skills: Identify knowledge gaps among staff regarding maintenance tasks.
- Budget Constraints: Align the maintenance program with financial capabilities.
- Regulatory Compliance: Ensure adherence to relevant legal and industry regulations.
The benefits of a proper needs assessment include tailored solutions that align with organizational goals, reduced waste of resources, and improved employee satisfaction.
Choosing the Right Program
Selecting the appropriate maintenance management program is a complex process that requires thoughtful consideration of multiple factors. Organizations should analyze various options based on their specific needs identified in the assessment phase. Factors affecting this decision include:
- Type of Maintenance: Depending on the equipment and operational demands, one may opt for preventive, predictive, or condition-based maintenance practices.
- Scalability and Flexibility: Choose a program that can grow with the organization and adapt to changing needs.
- Integration Capabilities: Look for programs that can easily integrate with existing technology or future upgrades.
- Vendor Support: Evaluate the level of technical support and updates provided by the program vendor.
A well-chosen program can lead to enhanced efficiency, better asset utilization, and significant cost savings over time.
Training and Development
Once a maintenance management program is chosen, the focus must shift to ensuring that employees are adequately trained. Continuous professional development is vital for minimizing downtime and maximizing operational efficiency. Training should be comprehensive and tailored to different roles within the organization. Essential components of effective training include:
- Hands-On Training: Practical sessions on tools and technology to ensure familiarity.
- Regular Workshops: Scheduled sessions to refresh skills and keep staff updated on best practices.
- Team Collaboration: Encourage teamwork in training efforts, which promotes knowledge sharing and group learning.
Investing in employee training not only prepares staff for challenges but also fosters a culture of continuous improvement and accountability.
"A well-informed workforce is the backbone of successful maintenance management."
Evaluating Maintenance Management Programs
Evaluating maintenance management programs is crucial for ensuring that they align with organizational goals and deliver the desired outcomes. This evaluation process involves a systematic approach to assess the effectiveness and efficiency of maintenance strategies. By regularly examining these programs, organizations can identify areas for improvement and optimize resource allocation. Key aspects of this evaluation include performance measurement, feedback mechanisms, and alignment with broader business objectives.
Key Performance Indicators
Key Performance Indicators (KPIs) are essential tools in evaluating the success of maintenance management programs. These metrics provide quantifiable measures of performance, allowing organizations to track their maintenance activities over time. Common KPIs in this context include:
- Mean Time Between Failures (MTBF): This measures the average time between equipment breakdowns. A higher MTBF indicates better reliability.
- Mean Time to Repair (MTTR): This refers to the average time taken to restore equipment after a failure. Shorter MTTR values indicate more efficient maintenance processes.
- Maintenance Cost as a Percentage of Replacement Asset Value: This ratio helps organizations understand their maintenance spending proportional to the asset's value.
These indicators guide decision-makers in determining the effectiveness of their maintenance programs. Additionally, they provide insights into cost efficiency and the overall condition of assets.
Continuous Improvement Processes
Continuous improvement processes play a vital role in enhancing maintenance management programs. This approach encourages organizations to constantly analyze and refine their maintenance strategies. The process typically involves several key steps:
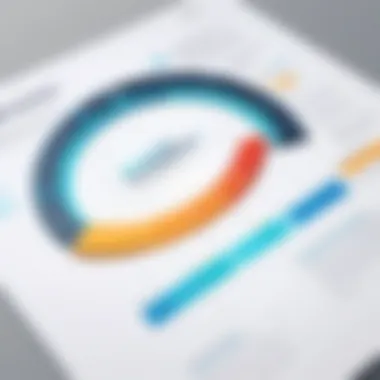
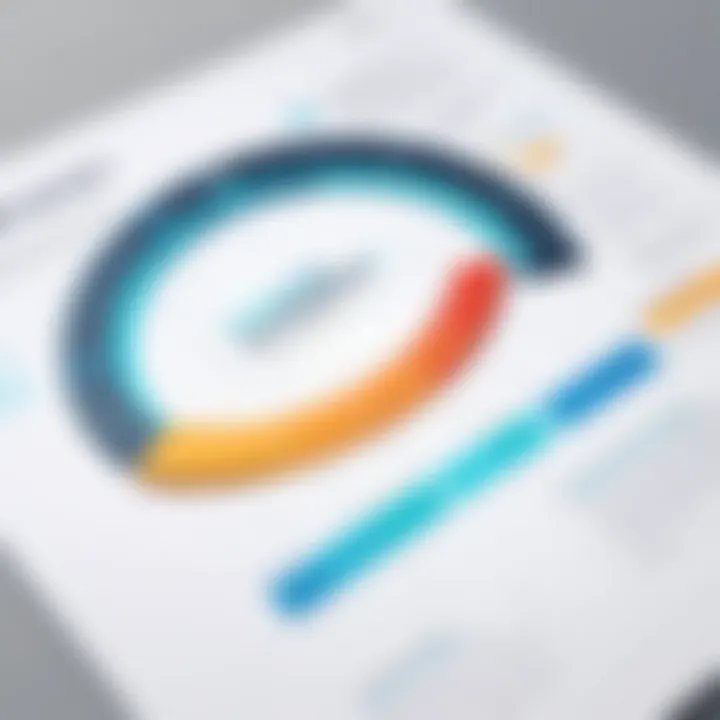
- Data Collection: Gather data on KPIs, maintenance activities, and asset performance regularly.
- Analysis: Examine the collected data to identify patterns, trends, and outliers that could point to inefficiencies.
- Implementation: Develop and execute action plans to address identified issues or optimize processes.
- Review: After changes are implemented, evaluate their impact on the KPIs to ensure that they lead to the desired improvements.
By adopting continuous improvement practices, organizations can adapt to changing environments, meet evolving business needs, and maintain competitive advantage.
"Regular evaluation of maintenance programs not only identifies weaknesses but also paves the way for strategic enhancements."
In summary, evaluating maintenance management programs is an ongoing process that involves careful consideration of performance metrics and a commitment to continuous improvement. This approach ultimately leads to better asset management, reduced costs, and increased operational efficiency.
Challenges in Maintenance Management
In the realm of maintenance management, professionals encounter a series of obstacles that can significantly impact the effectiveness of their programs. These challenges are multifaceted and often interconnected, encompassing resource allocation, change resistance, and data management issues. Understanding these challenges is essential for organizations striving to enhance their maintenance strategies.
Resource Allocation
Effective resource allocation is critical in maintenance management. Organizations must balance human, financial, and material resources to ensure optimal maintenance activities. Poor allocation can lead to several issues, such as increased downtime, inefficient use of equipment, and even escalated operational costs. To address this, leaders should conduct a thorough assessment of resource needs, considering factors like workload, workforce skills, and budget constraints.
Investing in employee training can improve maintenance effectiveness, as skilled workers can diagnose and resolve issues more efficiently. Also, integrating advanced technologies can streamline operations, thus enhancing resource utilization. For instance, employing CMMS software can provide insights into resource needs based on historic data, helping management make informed decisions.
Change Resistance
Change is often met with reluctance in many organizations, and maintenance management is no exception. Resistance to adopting new procedures or technologies can hinder the effectiveness of maintenance strategies. This sometimes stems from a fear of the unknown or concerns about job security; if employees feel that new technologies may replace their roles, they may oppose changes.
Addressing this resistance requires effective communication from leadership. It should be clear that changes aim to enhance processes, not replace personnel. Engaging employees in the transition can also foster a sense of ownership and acceptance. Providing comprehensive training on how to operate new tools can ease the transition, as employees become more confident in their use.
Data Management Issues
Data management plays a pivotal role in maintenance programs. As organizations rely more on data-driven decision-making, struggles in managing that data can lead to poor maintenance outcomes. Many organizations face problems with data collection, storage, and analysis. Inconsistent data can result in misinformed decision-making, leading to inefficient maintenance practices.
Organizations should establish clear protocols for data management. This involves developing standardized procedures for data entry and ensuring data integrity over time. Utilizing cloud-based solutions can modernize data management while facilitating real-time access to information. Moreover, embracing analytics software can enable the extraction of valuable insights from data, aiding maintenance teams in trend identification and decision-making.
"Effective data management is not just a function; it is a cornerstone of a successful maintenance management program."
In summary, challenges like resource allocation, change resistance, and data management can significantly affect the efficiency of maintenance management programs. However, with strategic planning and proactive measures, organizations can overcome these obstacles and optimize their maintenance strategies.
Future Trends in Maintenance Management
As industries evolve, so do the methods employed in maintenance management. The future trends in this area showcase a blend of innovation and practicality that can greatly enhance operational efficiency. Focusing on automation, artificial intelligence, and sustainability, these trends are shaping the next generation of maintenance practices. Recognizing their significance allows organizations to remain competitive and responsive to technological advancements.
Automation and Robotics
Automation is a pivotal trend in maintenance management that drives productivity. By integrating robotic systems, companies can streamline repetitive tasks, reducing manual effort. Automated machines can perform inspections, monitor equipment, and execute routine maintenance tasks. This not only minimizes human error but also allows staff to focus on more complex issues.
Benefits of automation include:
- Increased Precision: Robots can perform tasks that require high accuracy, ensuring maintenance is done to specifications.
- Time Efficiency: Automation can drastically reduce the duration of maintenance cycles, allowing for quicker turnaround on machinery and equipment upkeep.
- Cost Savings: With fewer labor hours required, organizations can better allocate their resources while also potentially lowering overhead costs.
Artificial Intelligence Applications
Artificial intelligence (AI) is increasingly finding its way into maintenance management. AI algorithms analyze large amounts of data, providing insights that can predict equipment failures or maintenance needs before they become critical. Utilizing AI can significantly improve decision-making processes.
Key aspects of AI in maintenance include:
- Predictive Analytics: By using historical data, AI predicts when maintenance should occur, avoiding unnecessary downtime.
- Enhanced Diagnostics: AI systems can diagnose equipment issues through real-time monitoring, leading to faster resolution.
- Resource Optimization: AI helps in better resource planning, by predicting consumption and allocating inventory accordingly.
Sustainability Initiatives
The focus on sustainability is transforming maintenance management programs. Companies are increasingly aware of their environmental footprint and are implementing practices that reflect a commitment to sustainability. This involves using eco-friendly materials and processes in maintenance activities.
Important considerations in sustainability initiatives include:
- Energy Efficiency: Implementing energy-efficient machinery reduces operational costs and minimizes environmental impact.
- Waste Reduction: Various methods of waste management and recycling are integrated into maintenance plans, promoting a circular economy.
- Compliance with Regulations: As governments enforce stricter regulations regarding environmental practices, companies must adapt. Sustainability in maintenance ensures compliance and mitigates any potential fines or legal issues.
Thereby, organizations that take heed of these trends can position themselves as leaders in the industry. Adopting automation, leveraging AI, and committing to sustainability can bolster maintenance effectiveness and overall operational success.
End
The importance of effective maintenance management lies in its ability to reduce downtime and extend the lifespan of assets. By implementing systematic approaches, organizations can foresee potential failures and act proactively. This is critical in industries where equipment reliability directly affects production and service delivery.
Specific elements such as preventive, predictive, and condition-based maintenance have shown their value in mitigating risks. These strategies provide frameworks that guide organizations in developing tailored solutions that meet their unique needs.
Moreover, the rise of technology enhances maintenance management's efficiency. Tools like Computerized Maintenance Management Systems (CMMS) support data-driven decision-making. They simplify work order management and improve communication across teams.
However, as discussed in earlier sections, effective implementation is contingent upon addressing challenges like resource allocation and change resistance. A proper understanding of these obstacles allows organizations to develop strategies that foster a culture open to change.
Overall, the benefits of maintenance management programs are profound. By prioritizing these practices, organizations can achieve both operational excellence and significant cost savings, leading to a more sustainable business model.
Summary of Insights
This article has highlighted key insights regarding maintenance management programs. Here are the main takeaways:
- Definition and Importance: Maintenance management programs focus on optimizing operations and ensuring asset longevity.
- Types of Programs: Different types such as preventive, predictive, and condition-based maintenance offer tailored solutions for varying organizational needs.
- Key Components: Core components like asset management, work order management, inventory control, and scheduling are essential for effective program execution.
- Role of Technology: Tools like CMMS and IoT solutions play a significant role in enhancing the efficiency and effectiveness of maintenance management.
- Implementation Strategies: Successful implementation requires a clear assessment of organizational needs and adequate training for personnel.
- Evaluating Programs: Continuous improvement processes and the use of Key Performance Indicators (KPIs) help in evaluating the success of maintenance management efforts.
Through carefully designed systems and processes, organizations can greatly improve their maintenance approach. This leads not only to enhanced productivity but also to a more resilient operational framework that can adapt to future challenges.