Navigating Pharmaceutical QMS Software Effectively
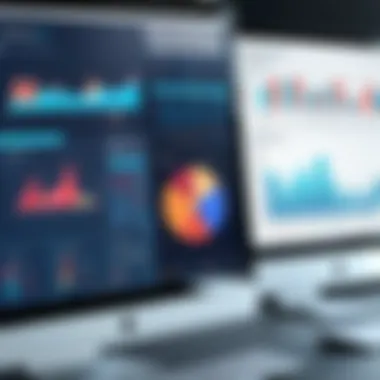
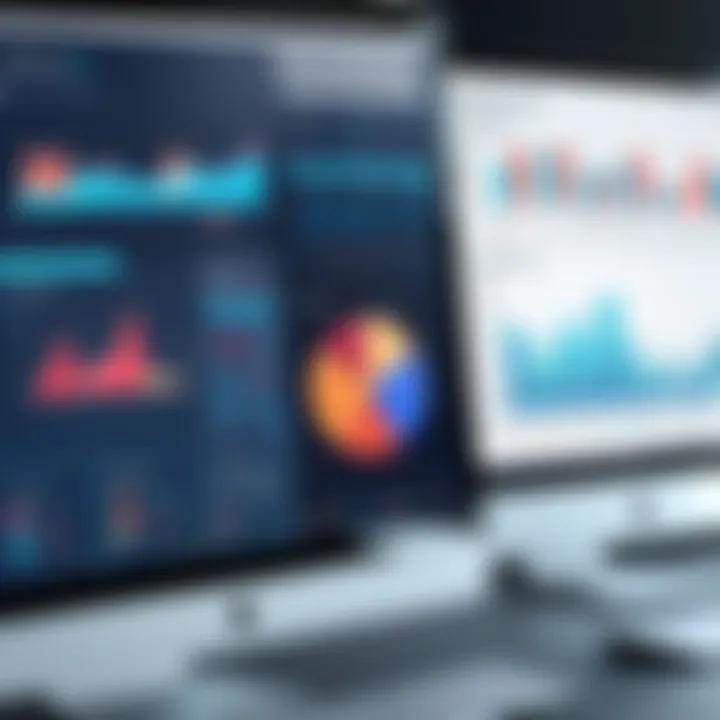
Software Overview
Pharmaceutical Quality Management System (QMS) software is an essential tool in ensuring that pharmaceutical companies meet regulatory standards while maintaining operational efficiency. By automating various processes, such software facilitates compliance with industry regulations, such as the FDA’s 21 CFR Part 11, ensuring that documentation and data handling are robust and secure.
Brief Description of Software
Pharmaceutical QMS software helps organizations manage quality processes comprehensively. It typically includes modules for document control, training management, non-conformance tracking, and audit management. The goal of this software is simple: improve quality while reducing risks. In this high-stakes industry, where the margin for error is slim, utilizing a QMS is not just desirable—it's imperative.
Key Features and Functionalities
• Document Control: Centralizes the storage and management of documents to ensure easy access and version control. This feature minimizes the risk of working with outdated information.
• Training Management: Tracks employee training to ensure that staff are updated on the latest regulations and procedures, thereby bolstering compliance.
• Non-Conformance Tracking: Records and manages quality issues or deviations from standard procedures, allowing for swift corrective actions.
• Audit Management: Streamlines audit processes, providing tools for managing schedules, checklists, and findings. This ensures that all audits are thorough and organized.
• Risk Management: Identifies potential risks in processes and allows organizations to assess and mitigate these risks proactively.
Detailed Comparison
When selecting Pharmaceutical QMS software, understanding the competitive landscape is crucial. There are several options available that cater specifically to the pharmaceutical sector. Each tool comes with its own set of benefits and limitations, which are worth comparing before making a decision.
Comparison with Competitors
Top players in this market include MasterControl, Veeva Vault QMS, and Sparta Systems' TrackWise. Each of these solutions offers distinct features:
- MasterControl: Known for its user-friendly interface and extensive document control capabilities. It is often praised for excellent customer support.
- Veeva Vault QMS: Cloud-based solution that integrates seamlessly with other Veeva products; ideal for companies that value comprehensive solutions.
- TrackWise: Highly customizable and scalable, suitable for larger organizations looking for extensive configurability.
Pricing Structure
Pricing can vary widely based on the functionalities required, the size of the organization, and deployment type. Many software vendors offer tiered pricing models:
- Entry-Level Plans: Typically suitable for small organizations or those just starting with a QMS. These may include basic features at a lower cost.
- Mid-Tier Plans: Designed for growing organizations needing additional functionalities like advanced reporting tools and enhanced support.
- Enterprise Solutions: These are tailored for large corporations with complex needs, often requiring a customized quote based on specific requirements.
"In the world of pharmaceuticals, complying with regulations isn’t just about avoiding fines; it’s about ensuring that patients receive safe and effective products. A sophisticated QMS isn’t a luxury—it’s a necessity."
Prelude to Pharmaceutical QMS Software
In an industry where precision is paramount, the role of Quality Management System (QMS) software in the pharmaceutical sector cannot be overstated. This section is vital as it lays the groundwork for understanding how these systems function, their objectives, and the value they add to organizations.
Definition and Purpose
Pharmaceutical QMS software is designed to facilitate and enhance quality management processes. The core purpose of this software is to ensure that pharmaceutical companies meet and exceed the rigorous standards set by regulatory bodies. It encompasses several functionalities, including but not limited to document control, corrective and preventive actions (CAPA), and audit management.
By simplifying compliance procedures and standardizing processes, this software helps organizations maintain a high level of quality throughout their operations. It’s not merely about adhering to rules; it’s about embedding quality into the very fabric of an organization’s culture. The right QMS software acts as a compass, guiding firms through complex regulations while emphasizing continuous improvement. In essence, it’s about cultivating a mindset of quality that permeates every level of the operation.
Importance in the Pharmaceutical Sector
The pharmaceutical sector operates under the watchful eye of multiple regulatory bodies, making compliance a top priority for any organization. Without proper integration of QMS software, pharmaceutical companies may find themselves navigating a labyrinth of guidelines, making their path more perilous.
The importance of a robust QMS software system can be broken down into several key aspects:
- Risk Mitigation: By implementing rigorous quality checks, companies can avoid costly recalls and ensure patient safety.
- Operational Efficiency: Streamlined processes permit faster product development and time-to-market timelines, keeping firms competitive.
- Data Management: A centralized system allows for better data visibility and provides a reliable archive for audits, ensuring data integrity.
"Quality should never be a compromise in the pharmaceutical industry; it's a matter of life and death."
Moreover, the emphasis on documentation and traceability can bolster a company’s credibility. A well-implemented QMS can serve not just as a compliance tool but also as a competitive differentiator. In a field where trust and reliability are non-negotiable, investing in a comprehensive QMS software solution is not merely a business decision but a strategic imperative.
Regulatory Framework
A strong regulatory framework is crucial for any economic sector, but when it comes to pharmaceuticals, it’s akin to the backbone of the industry. This section focuses on how proper governing bodies and requirements enhance Quality Management System (QMS) software implementation. In an industry where safety is paramount, understanding the regulations can make or break a company's reputation. Ignorance of these laws can lead to hefty fines, operational disruptions, and worst of all, risks to public health. With compliance as the guiding star, QMS software must not only meet but excel in regulatory adherence to ensure quality control across the board.
Overview of Regulatory Compliance
Regulatory compliance serves as the set of rules, laws, and guidelines established by various authorities to ensure that pharmaceutical companies operate within defined safety and quality standards. These regulations are not arbitrary but crafted through extensive research and experience, aimed at mitigating risk and ensuring public safety. Understanding the compliance landscape involves knowing the difference between federal, state, local, and international regulations.
Keeping up with regulations can feel like hitting a moving target at times, but an integrated QMS addresses this concern head-on. By automating processes and maintaining stringent documentation, it allows organizations to navigate regulatory waters more smoothly, ensuring that compliance is not just met but ingrained into the organizational culture.
Key Regulations Impacting QMS Software
Several key regulatory guidelines influence the functionalities and implementation of QMS software in the pharmaceutical realm:
FDA Regulations
FDA regulations are among the most significant for those in the pharmaceutical industry. They mandate that companies establish a robust quality management system to safeguard that products are safe and effective. One major aspect of these regulations is the CFR Title 21, Part 820, known as the Quality System Regulation (QSR). This regulation provides a framework that specifies rigorous control over every aspect of manufacturing, from design to production and distribution.
A key characteristic of FDA regulations is that they are often updated to keep pace with technological advancements. This makes resident compliance extremely important as the QMS software must adapt to these changes without causing disruptions. The unique feature of FDA regulations lies in their enforcement; failure to comply can lead to not only financial penalties but also bans from the market entirely, which is clearly a major deterrent for companies.
ISO Standards
ISO standards establish international benchmarks for a multitude of sectors, including pharmaceuticals. The ISO 13485 standard specifically focuses on quality management systems tailored for medical devices. Having a QMS that aligns with ISO standards means maintaining consistent design, development, and delivery processes.
The benefit of ISO standards is their global acceptance. This standard helps companies simplify regulatory compliance across borders, a vital consideration for organizations looking to market their products internationally. A unique feature of ISO standards is the emphasis on continual improvement. This pushes organizations not to rest on their laurels but to constantly seek enhancements in their processes, enhancing their quality management systems incrementally.
GxP Guidelines
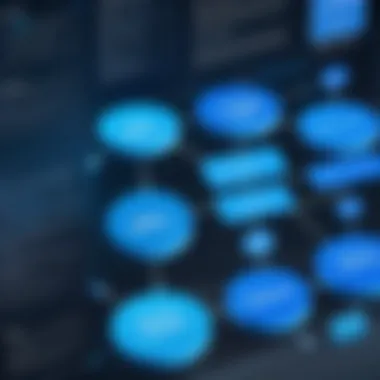
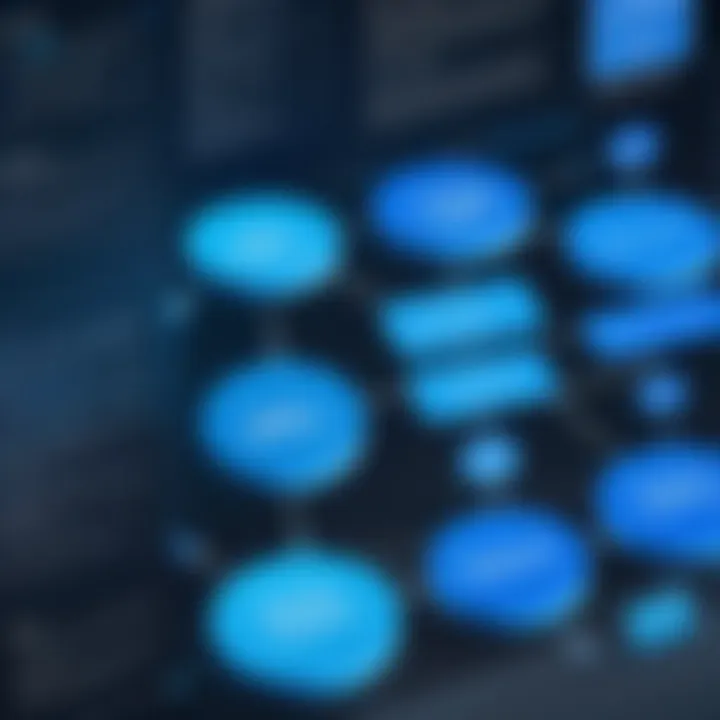
Good Practice (GxP) guidelines are fundamental in ensuring that pharmaceuticals and related products are consistently controlled throughout their production processes. Categories of GxP include Good Manufacturing Practice (GMP), Good Clinical Practice (GCP), and Good Laboratory Practice (GLP). Each of these guidelines places importance on adopting strict protocols for various pharmaceutical operations.
The hallmark of GxP guidelines is their focus on risk management, providing a comprehensive approach to ensure quality by embedding good practices into every stage of the product lifecycle. An advantageous aspect of adhering to GxP is that it fosters a culture of quality that extends beyond just compliance; it encourages a holistic approach to quality assurance in all operations. However, the evolving nature of GxP can sometimes present challenges for adherence, requiring companies to invest significant time and resources into staying compliant.
Staying abreast of these regulations is not just about compliance; it’s a matter of organizational integrity and public trust.
As the pharmaceutical landscape evolves, the importance of navigating these regulatory frameworks becomes even more critical. With stringent guidelines being the language of success, establishing a solid foundation in understanding and implementing QMS software under this guidance is essential.
Key Features of Pharmaceutical QMS Software
Key features of Pharmaceutical QMS software serve as the backbone of effective quality management in the pharmaceutical industry. These elements help organizations to streamline processes, enhance compliance, and ensure that products meet the high standards required by regulations. When choosing a QMS software solution, understanding these features is crucial because they can dictate the overall success of quality initiatives and operational efficiency.
Document Control and Management
Document control is an essential aspect of QMS in the pharmaceutical sector. This feature enables organizations to manage the creation, review, approval, distribution, and archival of documents in a systematic way. An efficient document management system not only enhances regulatory compliance but also reduces the risk of errors that can arise from using outdated or incorrect documentation.
For instance, consider a company that develops a new medication. The ability to control variations in documentation such as protocols or SOPs (Standard Operating Procedures) ensures everyone is working with the latest information. Here are key benefits of robust document control:
- Centralized Access: All team members can access documents from a single location, reducing confusion.
- Version Control: Every change to a document is tracked, allowing for easy retrieval of prior versions.
- Audit Trails: Detailed logs of changes make audits simpler, highlighting compliance during inspections.
CAPA Management
Corrective and Preventive Action (CAPA) management is critical for addressing issues and preventing them from reoccurring. This feature automates the process of identifying, documenting, and resolving quality-related problems. When an issue arises—like a deviation in manufacturing—CAPA helps teams analyze the problem, implement corrective measures, and document the findings.
Notable aspects of CAPA management include:
- Timeliness: Speed up the resolution process by automating notifications and escalations.
- Comprehensive Analysis: Use root cause analysis tools to identify factors contributing to a problem.
- Outcome Tracking: Monitor the effectiveness of corrective actions to ensure desired results.
Audit Management
Audits are a routine but necessary part of the pharmaceutical landscape. QMS software often includes audit management features to facilitate both internal and external audits. These tools assist in planning, scheduling, conducting, and documenting audit findings systematically.
Key advantages include:
- Streamlined Scheduling: Automatically schedule audits based on regulatory timelines.
- Checklists: Customized checklists help ensure that nothing significant gets overlooked during audits.
- Findings Repository: Store and track audit findings in a centralized location for easy future reference and follow-up.
Risk Management Module
Understanding and mitigating risks is vital for pharmaceutical companies. A risk management module within QMS software identifies potential hazards associated with processes or products and assesses their possible impacts. By systematically evaluating risks, companies can prioritize mitigation efforts effectively.
Among the features that enhance risk management:
- Risk Assessment Templates: Preloaded templates that guide users in documenting and assessing risks.
- Real-time Monitoring: The ability to track risk changes and adjustments as they occur encourages proactive management.
- Integration with Other Modules: Risk management often connects to CAPA and audit management, providing a holistic view of quality issues.
Reporting and Analytics
Effective data reporting and analytics capabilities are crucial for informed decision-making in the pharmaceutical sector. These features gather data from various sources and present them in intuitive formats, from dashboards to comprehensive reports. They help stakeholders visualize trends, compliance statuses, and operational efficiencies.
By leveraging good reporting and analytics tools, companies can:
- Identify Trends: Track quality metrics over time to proactively address areas of concern.
- Compliance Tracking: Ensure that organizational standards and regulatory requirements are being met efficiently.
- Performance Metrics: Compare departments or product lines to improve practices across the board.
"Using analytical reporting gives us a clearer roadmap on where improvements can be made." - Quality Assurance Manager
In summary, the key features of Pharmaceutical QMS software are designed to address the unique challenges of the industry. Organizations that invest in these functionalities not only streamline their processes but also enhance their ability to comply with stringent regulatory requirements.
Choosing the Right QMS Software
Selecting the appropriate Quality Management System (QMS) software for the pharmaceutical sector is no small feat; it is akin to picking the right tool to craft a delicate piece of machinery. The stakes are high due to stringent regulations and the potential impact on patient safety. Making an informed choice can lead to enhanced compliance, optimized workflows, and reliability in data management. For companies aiming to navigate the complexities of regulatory requirements, understanding how to choose the right QMS software becomes essential for both operational integrity and developing a stringent quality framework.
Assessment Criteria
When evaluating QMS software, it is crucial to weigh several key criteria to ensure alignment with organizational goals and regulatory requirements. Here are some major aspects to consider:
- User-Friendliness: The software should be intuitive and easy for team members to navigate without steep learning curves.
- Customizability: Each organization has unique needs; thus, the ability to tailor workflows and features can greatly enhance usability.
- Compliance Features: Look for built-in compliance tracking aligned with regulatory standards that are specific to the pharmaceutical industry.
- Customer Support: Review the level of support provided post-implementation. Responsive customer service can save significant time when issues arise.
- Cost and ROI: Assess both upfront and ongoing costs versus potential return on investment; this often requires careful forecasting.
By using a comprehensive assessment checklist, companies can make informed decisions that align with their operational strategy.
Integration Capabilities
The ability of a QMS software to seamlessly integrate with existing systems or third-party tools can greatly influence its effectiveness.
Existing Systems
Existing systems often represent a company’s previous investments in technology. A QMS that works well within this framework can save resources and facilitate continuity. Key characteristics of existing systems to explore include:
- Data Flow: The capacity for the QMS software to facilitate a smooth data transfer between various departments can bolster overall efficiency.
- Compatibility: Understanding how well new QMS software meshes with legacy systems helps prevent costly disruptions.
- User Acceptance: If employees are accustomed to existing systems that the QMS software easily incorporates, user adoption increases and the transition becomes smoother.
Thus, leveraging existing systems is often economically beneficial, as it capitalizes on investments already made.
Third-Party Tools
Third-party tools can enhance the capabilities of QMS software. They often bring unique functionalities and extend the software’s reach beyond standard offerings. Factors to consider include:
- Versatility: Many third-party tools offer specific functions, like analytics or compliance tracking, that can provide pivotal insights missed otherwise.
- Ecosystem Compatibility: Assessing how well these tools integrate into the overall software ecosystem is key to maintaining operational efficiency.
- Flexibility and Cost: Some tools may require additional fees, but they can also save time and resources down the line due to more specialized functionality.
Integrating these tools can bring a robust dimension to QMS capabilities, provided that they are evaluated properly against the organization’s needs.
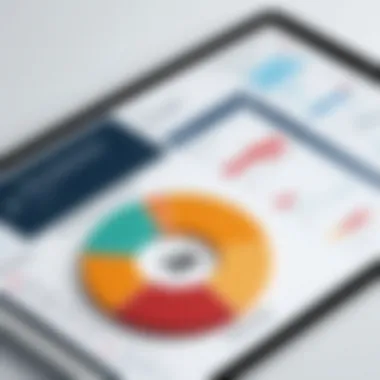

Scalability Considerations
Looking ahead, scalability is paramount. A good QMS software not only meets today’s needs but also anticipates future growth.
- Growth Tracking: As an organization expands, the QMS should easily accommodate new processes without requiring a complete software overhaul.
- User Capacity: Ensuring that the platform can support more users as your team grows can avoid potential bottlenecks in usage.
- Feature Expansion: Opting for software that allows for additional modules or functionalities over time can keep your QMS relevant and useful.
Considering scalability will help ensure that the chosen QMS solution remains effective and economical in the long run.
Implementation Strategies
Implementing a Quality Management System (QMS) in the pharmaceutical sector isn’t just a necessity; it’s a journey that requires meticulous planning, training, and continual assessment. This stage is essential because it lays the groundwork for how effectively the software will be utilized down the line. If the right strategies are put into place, organizations can reap significant benefits, such as streamlined processes, improved compliance, and ultimately, enhanced product quality.
Project Planning
Project planning is the cornerstone of any successful QMS implementation. The significance of having a well-structured project plan cannot be overstated. Often, organizations dive headfirst into software implementation only to find themselves overwhelmed or unprepared. Just like trying to sail without a map, it's easy to stray off course.
To delve deeper into project planning:
- Define Objectives: Start by identifying clear objectives for the QMS. What challenges are you aiming to overcome? Specific goals enable teams to work towards a common purpose.
- Establish a Timeline: An effective timeline outlines the critical milestones and deadlines. This structured approach fosters accountability and keeps everyone on track.
- Resource Allocation: Ensure that the right resources, including personnel and budget, are designated for the project. Conduct a needs assessment to identify gaps that may affect the implementation.
- Stakeholder Involvement: Keep key stakeholders engaged throughout the planning phase. This includes employees who will be interacting with the system daily as well as upper management who can provide strategic insight.
By laying out this plan in a methodical manner, organizations can mitigate confusion and focus on achieving a smooth implementation.
Training and Support
Once the project plan is in place, training becomes the next critical step. The success of QMS software hinges largely on user adoption. It’s one thing to have a robust software solution, but if employees aren’t adequately trained, you’re just buying yourself a fancy paper weight.
Here’s why proper training and ongoing support are vital:
- User Training Programs: Implement comprehensive training programs tailored for various user levels. Employees ranging from data entry clerks to top executives might use the system differently. A one-size-fits-all approach simply won’t cut it.
- Continuous Support Channels: Establish support mechanisms, be it through a help desk, user manuals, or FAQ sections. Employees should know where to turn if they encounter issues.
- Feedback Loops: Encourage feedback from users to refine the training process further. This way, organizations can adapt their training to better meet the real-world needs of users.
With ongoing support, companies can enhance user confidence and engagement, ultimately driving better outcomes.
Monitoring and Continuous Improvement
Monitoring the system after implementation is crucial. Integration of a continuous improvement process upfront ensures the QMS evolves alongside the organization's changing needs. It paints a realistic picture of the current state and shows where adjustments are needed.
Here’s where organizations can focus their efforts:
- Regular Audits: Schedule periodic audits to ensure the QMS aligns with industry standards and regulatory requirements. These audits act like a health check, giving insights into potential areas of concern.
- Performance Metrics: Identify KPIs that indicate the effectiveness of the QMS. Are you hitting compliance targets? Tracking progress against these benchmarks allows for informed decision-making.
- Adaptation and Feedback: Be open to changes. The pharmaceutical landscape is dynamic, and your QMS needs to flex and adapt as regulations evolve. It’s imperative to stay ahead, which could involve updating training or tweaking processes to improve functionality further.
In essence, a well-structured framework for monitoring and continuous improvement can reinforce the value of QMS software in a fast-paced industry.
Continuous improvement in QMS is not merely an option; it is the lifeblood that ensures organizations stay compliant and competitive in the ever-changing pharmaceutical landscape.
Benefits of Pharmaceutical QMS Software
In the pharmaceutical industry, a robust Quality Management System (QMS) software program is not just a convenience; it’s a bridge to operational excellence and regulatory compliance. The importance of these systems is evident in their multifaceted benefits that enhance not only compliance but also overall business efficiency. Let's explore how pharmaceutical QMS software serves as a critical component in achieving organizational objectives.
Enhanced Compliance and Quality Control
Compliance is non-negotiable in pharmaceuticals. Every product that hits the market must meet stringent regulations; otherwise, the fallout can be devastating. Pharmaceutical QMS software aids organizations in maintaining regulatory compliance by offering systematic processes that align with industry standards.
Features such as document control, which tracks every piece of paperwork related to quality assurance, ensure that no stone is left unturned. Audit trails are essential here, allowing for transparency in operations. Regular audits become less burdensome; the software often includes audit management tools that streamline this process.
Additionally, with built-in CAPA (Corrective and Preventive Actions) management, organizations can swiftly address potential compliance failings before they escalate. This proactive approach significantly mitigates risks associated with non-compliance, fostering a culture of quality and assurance throughout the organization.
"Quality is not an act; it is a habit." - Aristotle
Increased Efficiency and Productivity
When it comes to productivity, the integration of pharmaceutical QMS software is a game changer. These systems automate numerous processes that would otherwise consume valuable time and resources. For example, manual data entry can become a virtual labyrinth, leading to delayed insights and increased chances for error.
Pharmaceutical QMS software streamlines workflows, reducing redundancies and cutting back on the time needed for reporting. Resources can be allocated more effectively, with employees spending less time on admin duties and more time on strategic initiatives. The efficiency gained here can be staggering. By integrating QMS tools across different departments, organizations can enhance communication and collaboration, resulting in faster and more informed decision-making.
Improved Data Management and Accessibility
The power of data cannot be understated. In the pharmaceutical sector, having access to accurate, real-time data is crucial for decision-making. QMS software centralizes data management, making it easier for stakeholders to access vital information from one source.
Moreover, with features like analytics dashboards, the software provides insights that were once buried in spreadsheets and reports. Decision-makers can track key performance indicators (KPIs) in real time, facilitating a more agile and relevant response to emerging challenges.
Accessibility also means that the correct data is just a few clicks away for those who need it, ensuring everyone from the lab to the boardroom can stay aligned on quality standards. This not only promotes accountability but also nurtures a unified approach to quality across all levels.
In summary, the benefits of pharmaceutical QMS software extend beyond mere compliance. They encapsulate efficiency, quality, and data management, forming a bedrock upon which organizations can build their future. As the industry continues to evolve, investing in solid QMS software becomes increasingly essential for any company striving for success.
Challenges in QMS Software Implementation
Implementing Quality Management System software in the pharmaceutical sector is not a walk in the park. It comes with a host of challenges that can throw a wrench in the best-laid plans. Understanding these challenges is crucial for IT professionals and decision-makers. They're not just speed bumps on the road to compliance; they can derail an entire project if not managed correctly. Let’s take a look at some key challenges that organizations face.
Resistance to Change within Organizations
One of the biggest hurdles in adopting new QMS software is the internal resistance from employees. When you think about it, people are naturally hesitant to change their routines. This type of resistance can be multifaceted. First, there’s the comfort factor. Employees may have been using the same system for years, and the thought of learning something new can be daunting.
Moreover, legacy systems often have a level of familiarity that new software just can’t compete with. Consider the phrase, "If it ain't broke, don’t fix it." Employees may perceive the new software as an unnecessary complication, especially if they don't see the immediate benefits.
Training becomes essential to give people the confidence to transition. It’s vital to communicate the advantages clearly.
- Provide training sessions that emphasize the user-friendly aspects of the new system.
- Involve staff members in the planning stages to ensure they feel part of the process.
- Highlight success stories from other organizations that have made similar transitions.
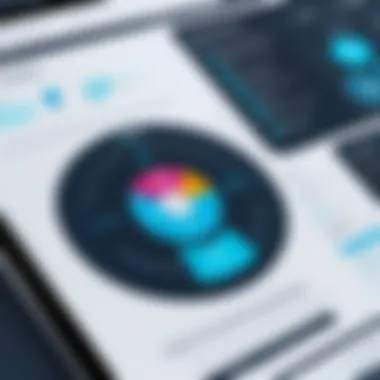

"Engagement is key. When people feel involved, they're more likely to embrace change."
Cost and Resource Allocation
Money talks and in the case of QMS software, it can often shout quite loudly. Budget constraints and resource allocation can create a significant barrier to effective implementation. For many organizations, it’s a balancing act between spending on new software and maintaining day-to-day operations.
A common pitfall is underestimating the total cost of ownership. It's not just about the initial purchase; there are ongoing expenses for maintenance, updates, and potential support services. Decision-makers should keep in mind that you might also need to invest in additional hardware or even additional staff training, both of which can stretch resources thin.
To navigate these challenges, organizations can adopt the
- Phased Approach: Roll out the system in stages to manage costs effectively.
- Budget for Contingencies: Always have a bit set aside for those unexpected costs.
- Research ROI: Understanding how the new software can save time and money in the long run can help justify the initial investment.
Cost might be a leading factor, but with the right planning and thoughtfulness, even tight budgets can find a way to incorporate the required software.
Dealing with these challenges head-on is crucial to reaping the long-term benefits of QMS software. While the road may be bumpy, a well-executed strategy can lead companies toward enhanced quality, compliance, and efficiency.
Future Trends in Pharmaceutical QMS Software
The landscape of pharmaceutical Quality Management Systems (QMS) is shifting rapidly, driven by technological advancements and changing industry requirements. Understanding these future trends is crucial for decision-makers, IT professionals, and entrepreneurs investing in QMS software. Anticipating where the industry is headed will not only keep stakeholders ahead of the curve but also enhance regulatory compliance and operational efficiency. By tapping into modern trends, the pharmaceutical sector can strive for improved outcomes and smarter processes.
Leveraging AI and Machine Learning
Integrating artificial intelligence (AI) and machine learning into QMS remarkably transforms how data is managed and analyzed within the pharmaceutical industry. For instance, AI algorithms can be trained to predict outcomes based on historical data, enabling proactive corrections rather than reactive measures. This shift from a reactive to a predictive model means potential risks can be managed before they escalate, improving safety and quality.
Key benefits of leveraging AI include:
- Enhanced Decision-Making: Automated data analysis can provide actionable insights, making it easier for teams to make informed decisions.
- Resource Optimization: By automating routine tasks, pharmaceutical companies can better allocate human resources to complex problem-solving activities.
- Personalized Compliance: AI can adjust compliance protocols based on real-time data, ensuring that operations align with the latest regulatory requirements.
Cloud-Based Solutions
Cloud-based QMS solutions usher in a new era of collaboration and accessibility. For teams working across multiple locations, these solutions provide a central repository for documents and quality metrics, enhancing communication and reducing errors. Companies like Veeva and MasterControl exemplify how cloud technology streamlines processes and connects stakeholders.
The main advantages include:
- Scalability: As business needs grow, cloud solutions can be scaled easily without requiring extensive hardware investments.
- Reduced IT Burden: With cloud services, the maintenance burdens typically associated with on-premise software are shifted to service providers.
- Real-time Updates: Changes in regulatory requirements can be immediately reflected in the cloud system, ensuring compliance without the hassles of manual updates.
Automated Compliance Tracking
One of the most tedious aspects of the pharmaceutical industry is the constant need to stay compliant amidst ever-evolving regulations. Automated compliance tracking addresses this challenge. By employing sophisticated software systems, companies can continuously monitor their operations against regulatory standards, reducing the risk of non-compliance.
Benefits of this approach include:
- Immediate Alerts: Automated systems can flag potential compliance issues before they become significant problems, allowing staff to act quickly.
- Audit Readiness: Real-time tracking ensures that all records and documentation are up to par for regular audits.
- Transparency: Automated systems increase visibility, offering clear insights into compliance trends over time.
"Pharmaceutical companies today face unprecedented regulatory scrutiny; automated compliance tracking can be their best ally in navigating these turbulent waters."
In summary, embracing these future trends can position pharmaceutical organizations for a more efficient, compliant, and forward-thinking approach to quality management. The ongoing evolution in technology offers substantial opportunities; therefore, being proactive and adaptable is the key to thriving in this environment.
Case Studies and Real-World Examples
In the complex world of pharmaceuticals, understanding how Quality Management System (QMS) software performs in real-life scenarios often provides invaluable insights. Case studies serve not just as anecdotes but as practical illustrations of both the successes and tribulations that companies face while implementing and using QMS software. The commitment to maintaining compliance and enhancing operational efficiency often hinges on learning from the experiences of others in the industry. These examples allow decision-makers and IT professionals to pave their own course, armed with knowledge borne from trial and error, thus facilitating smarter choices.
Successful Implementations
Navigating the intricate landscape of pharmaceutical compliance requires not only thorough understanding but also tactical execution. Many organizations have adopted QMS software, leading to successful implementations that set a benchmark for others.
One notable example is Smith & Johnson Pharmaceuticals, which faced significant documentation backlogs that hampered its ability to meet regulatory deadlines. By implementing the MasterControl QMS, they streamlined their documentation processes. The software allowed for enhanced collaboration and real-time updates, cutting the documentation time by nearly 40%. This transformation not only facilitated regulatory compliance but also fostered a culture of accountability across their divisions.
Furthermore, BioTech Innovations employs TrackWise QMS to manage their audit processes more effectively. This implementation has resulted in a reduction of non-conformance incidents by 25% within the first year. Employees are now able to generate audit reports with a couple of clicks, which enhances efficiency within the audit management space. This gives management a clearer overview of compliance levels at any point in time.
Such success stories spotlight the necessity of choosing the right QMS software tailored to an organization’s specific needs and the consequential benefits gained from enhancing their operations.
Lessons Learned from Challenges
While highlighting the successes is crucial, it is equally important to acknowledge the challenges encountered during QMS software implementation. Learning from these hurdles can provide invaluable lessons for new adopters.
For instance, PharmaTech Co. faced an uphill battle when they decided to adopt a cloud-based QMS. Initially, the employees were resistant to the change, along with a lack of adequate training resources. This resulted in a chaotic rollout that saw errors in compliance reporting initially skyrocket. It wasn’t until they dedicated time to train staff thoroughly and created an open feedback mechanism that issues were resolved. The subsequent re-training reinforced their operational protocols, leading to a more secure and confident workforce.
Another critical lesson came from R&D Pharmaceuticals, which invested in a top-tier QMS solution but neglected to involve key stakeholders during the selection process. The software was so complex that end-users struggled to adapt, resulting in extended implementation time and wasted resources. Through this experience, they learned the importance of thorough needs assessment and stakeholder engagement to ensure that any new system adopted aligns with actual user needs, ultimately pointing towards the importance of communication.
"It's not just about adopting new software; it's about integrating it in a manner that aligns with the workflows so that it genuinely adds value."
In summation, reflecting on case studies and real-world examples presents both a mirror of what’s possible and a roadmap of pitfalls to avoid. The key takeaway remains clear: strategic alignment and thorough training can be the difference between successful utilization of QMS software and it becoming another unused tool in the organization’s arsenal.
The End
The significance of a robust Quality Management System (QMS) in the pharmaceutical industry cannot be overstated. As this guide reveals, pharmaceutical QMS software serves as a pivotal tool in navigating the regulatory landscape, while also enhancing operational efficiencies. The journey towards quality compliance involves not just the implementation of software but a thorough comprehension of its role in fostering a culture of accountability and continual improvement within organizations.
Summarizing the Importance of QMS Software
In wrapping up our exploration of QMS software, it’s essential to reflect on a few key points:
- Regulatory Compliance: QMS software ensures adherence to stringent regulatory requirements which are crucial for maintaining product safety and efficacy. Its systematic approach aids organizations in effectively managing documentation, tracking incidents, and observing standards.
- Quality Assurance: By automating and standardizing various processes, QMS software significantly reduces the risk of human errors. This is particularly vital in an industry where precision is paramount.
- Operational Efficiency: Effective QMS software streamlines processes from manufacturing to post-market surveillance, thus enhancing productivity and reducing costs associated with non-compliance and rework.
"A well-functioning QMS is not merely a compliance tool; it’s a catalyst for continual improvement in quality and operational excellence."
In essence, integrating a comprehensive QMS software can lead to profound changes in how pharmaceutical companies operate. From improving regulatory compliance to bolstering customer trust, its benefits extend well beyond just meeting the bare minimums.
Final Considerations for Advisors
As advisors in the pharmaceutical space, understanding the nuances of QMS software is vital. Here are some considerations to keep in mind when guiding clients:
- Tailored Solutions: Each organization ’s needs are unique. Help clients assess their specific requirements and select software that aligns with their operational workflow.
- Training and Support: Emphasize the need for continuous training and support post-implementation. A software’s effectiveness is intricately linked to how well personnel are trained to use it.
- Stay Updated: Lastly, the landscape of regulations is ever-evolving. Regularly review and adapt the QMS to align with the latest regulatory changes and technological advancements to avoid pitfalls down the road.