Understanding the Materials Takeoff List: A Comprehensive Guide
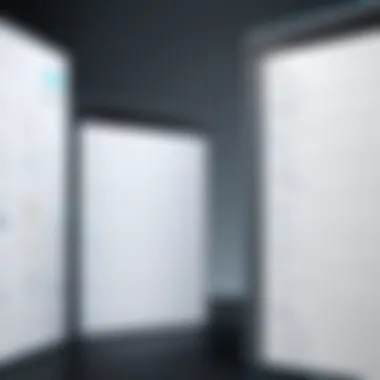

Intro
In the construction industry, precision is of utmost importance. One essential tool that ensures projects remain on target, both financially and operationally, is the materials takeoff list. This document acts as a bridge between design intentions and practical execution, allowing project teams to estimate the necessary materials accurately.
Understanding the materials takeoff list provides professionals with an advantage in budgeting, planning, and resource allocation. By leveraging accurate estimates, teams can avoid common pitfalls associated with cost overruns and material shortages. This guide presents a thorough exploration of the materials takeoff process, focusing on key techniques for creating these lists, as well as addressing challenges faced in this area.
Innovative software solutions play a significant role in enhancing the takeoff process. The integration of technology aids in streamlining workflows, ensuring that all team members access the most up-to-date information easily. As we delve deeper into this guide, we will uncover how software can improve accuracy, efficiency, and overall project management.
Prolusion to Materials Takeoff List
The materials takeoff list serves as a cornerstone in the construction and project management sectors. Essentially, it is a detailed compilation of all the materials, their quantities, and specifications required for a construction project. Understanding this list is crucial for accurate budgeting and resource allocation. This article aims to break down the concept and importance of the materials takeoff list, especially for professionals involved in project planning and execution.
A well-prepared materials takeoff list can prevent unnecessary delays and cost overruns in a project. By providing a clear roadmap of required materials, it fosters effective communication among stakeholders and aids in ensuring that projects remain on schedule.
Definition of Materials Takeoff
A materials takeoff is a quantified list of materials needed for the construction of a structure. This list includes various items such as concrete, steel, wood, and fittings. Each item is specified in detail to ensure clarity in procurement and project execution. The takeoff not only lists materials but also encompasses needed quantities and types. This precision is vital in competitive bidding scenarios, where accurate cost estimation can mean the difference between winning and losing a contract.
Importance in Construction Projects
The significance of a materials takeoff list cannot be overstated. It serves multiple purposes in the lifecycle of a construction project:
- Cost Control: Accurate material estimation helps in maintaining budgetary constraints. It avoids over-ordering and minimizes waste.
- Time Management: When materials are identified early, procurement can be planned efficiently, reducing delays associated with material shortages.
- Project Planning: A materials takeoff directly supports project scheduling. This ensures that the right quantity of materials is available on-site at the right time.
- Improved Communication: A detailed list provides a common point of reference for all team members, enhancing collaboration among architects, engineers, and contractors.
"An accurate materials takeoff not only streamlines project management but also enhances the overall efficiency and effectiveness of construction processes."
In summary, the materials takeoff list is an essential tool in the construction industry. By creating a structured approach to material estimation, it assists stakeholders in making informed decisions that directly impact project success.
Key Components of a Materials Takeoff List
A materials takeoff list is a central document that provides essential information regarding the physical items needed for a construction project. Understanding the key components of this list is fundamental for ensuring the accuracy of material estimates. Each element contributes significantly to effective project planning and execution.
Types of Materials
The types of materials included in a takeoff list vary based on the project's nature. Common materials are concrete, steel, wood, and finishes like drywall or paint. Each category requires specific considerations. For example, concrete comes in different grades and mixtures. Steel might be structural or rebar. Recognizing each type's unique requirements helps avoid misestimations.
Establishing clear classifications ensures that every material is accounted for and detailed. Specificity is key, as general terms may lead to costly confusion. Therefore, including precise specifications in each material type is essential for comprehensive planning.
Quantities Required
Quantities are a crucial component of the takeoff list. Accurately determining how much of each material is necessary minimizes waste and helps in budgeting. Wrong quantity estimates can lead to project delays and cost overruns.
To ascertain accurate quantities, methods such as measuring dimensions on blueprints or digital plans are employed. Calculating square footage for flooring materials or linear footage for piping is common. Use of formulas or software tools can aid in achieving precise calculations. It's also prudent to account for variations in project scope that may occur after the takeoff process. Regular updates to the quantity estimates can help mitigate surprises later.
Cost Estimation
Cost estimation is significantly influenced by the materials takeoff list. This component provides a starting point for assessing the financial requirements of a project. Each material's price fluctuates based on market conditions and supplier reliability, thus highlighting the importance of current data.
Of equal importance is integrating a contingency budget for unexpected price changes. Overall, maintaining an accurate and up-to-date cost estimation based on the materials listed is vital for financial planning and project viability.
Supplier Information
Supplier information within the takeoff list ensures that sourcing materials is efficient. This includes details like name, contact information, and lead times for delivery. Having this data frequently allows for quick procurement decisions.
It's advisable to maintain relationships with multiple suppliers to ensure competitive pricing and availability. Moreover, understanding each supplier's strengths, such as their delivery speed or reliability, can help in making informed choices during material procurement.
Methods for Creating a Materials Takeoff List
Creating a materials takeoff list involves rigorous methodology to ensure that all necessary components for a construction project are accurately identified and quantified. Various methods exist, each providing its unique benefits and challenges. Understanding these methods is vital for professionals who aim to enhance efficiency and minimize errors in project management. Effective takeoff methods can lead to improved budgeting and coordinated procurement processes, essential aspects of any successful construction initiative.
Manual Takeoff Process
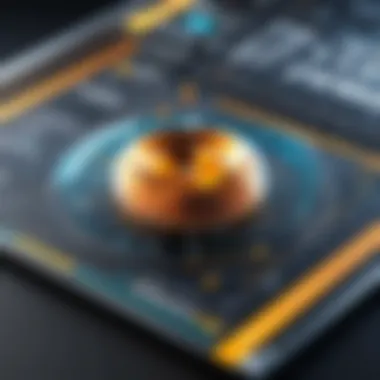

The manual takeoff process is one of the oldest techniques for estimating materials. This approach involves going through construction drawings, plans, and specifications while physically counting and measuring required materials.
Key Steps in Manual Takeoff:
- Review architectural and engineering drawings meticulously.
- Use a scale ruler to measure dimensions accurately.
- Create an itemized list of materials needed, detailing quantities and specifications.
This method can be beneficial for small projects or when dealing with specific details that automated systems may overlook. However, it can also be time-consuming and prone to human error. Thus, accuracy and diligence are essential.
Digital Takeoff Tools
Digital takeoff tools provide an automated and efficient method for creating materials takeoff lists. These tools are designed to streamline the takeoff process, allowing users to extract quantities directly from electronic blueprints and project files.
Advantages of Digital Tools:
- Speed: Rapid extraction of data reduces the time spent on manual counting.
- Accuracy: Minimizes the risk of errors inherent in manual processes.
- Integration: Many digital tools connect with project management software, facilitating seamless communication across teams.
Popular digital takeoff programs include Bluebeam Revu and PlanSwift, which offer features such as quantity takeoffs from PDFs and detailed reporting capabilities. Yet, users must be trained adequately to maximize the benefits of these tools.
Automated Estimation Software
Automated estimation software represents the pinnacle of materials takeoff methods. These sophisticated systems use algorithms to analyze project data and produce precise material lists. They support complex scheduling algorithms and can adjust quantities as project designs change.
Benefits of Automated Estimation:
- Efficiency: Reduces time spent on repetitive calculations and data entry.
- Risk Management: Minimizes errors associated with estimation inaccuracies.
- Scalability: Suitable for projects of any size, making it a versatile choice for various applications.
Leading software options like Sage Estimating and Autodesk Takeoff incorporate advanced features such as cost databases and built-in reporting tools that help managers make informed decisions based on real-time data. Employing this technology, however, does require an investment in training and system integration, which project managers should plan for adequately.
Challenges in Developing a Materials Takeoff List
Creating a materials takeoff list is a critical process in construction and project management, yet it is fraught with challenges that can hinder accuracy and effectiveness. These challenges are not merely procedural; they influence the overall project outcomes, making it essential to understand and address them. Accurate estimates ensure proper budgeting, adequate material supply, and adherence to timelines. Thus, recognizing the challenges involved in developing a materials takeoff list is crucial for professionals aiming to enhance project execution.
Common Errors in Estimation
Inaccurate estimations can stem from various sources. Fundamental errors often include miscalculating quantities needed for a project. Items might be overestimated or underestimated, leading to surplus or shortage situations that can disrupt the workflow. Failure to consider all necessary materials is another common error. A team might overlook specific items essential for project completion, such as rebar in concrete projects. This not only complicates procurement but also negatively impacts timelines.
Here are some errors to watch:
- Misinterpretation of project plans
- Lack of detailed measurement
- Ignoring supplier details regarding unit quantities
Variable Material Costs
Material costs can fluctuate due to various market conditions. These fluctuations make budgeting and planning challenging. Factors like inflation, supply chain disruptions, and global market trends can cause material prices to change significantly. When creating a materials takeoff list, it's crucial to factor in these variables. Relying on outdated cost estimates can lead to budget overruns, impacting overall project viability. Establishing a contingency fund or working with updated market data can mitigate risks associated with these variable costs.
"Financial oversight in material management is essential. Neglecting market dynamics can lead to unmanageable project expenditures."
Data Management Issues
Effective data management is a cornerstone of a successful materials takeoff list but is often overlooked. Poor organization of data leads to confusion and inefficiencies. Inconsistent data entry practices can create discrepancies, making it difficult to track material usage and costs. Moreover, without a centralized system, project teams may struggle to collaborate effectively. Each stakeholder needs access to accurate and updated information to make informed decisions. Therefore, implementing a robust data management strategy is essential to address these issues. Consider the following:
- Utilize specific software solutions for data access
- Establish clear data inputs and outputs for the team
- Regularly update data records to reflect changes in material costs and availability
Addressing these challenges in developing a materials takeoff list is vital for ensuring project success. By recognizing and mitigating common errors, staying alert to variable costs, and enhancing data management practices, professionals can significantly improve their project outcomes.
Best Practices for An Accurate Takeoff
Accurate materials takeoffs are crucial in construction projects. Best practices help to avoid common pitfalls and ensure the takeoff reflects what is needed. By implementing these best practices, project managers can improve their overall project outcomes.
Standardizing Processes
Standardization in the takeoff process can lead to greater accuracy and consistency. When all team members follow a uniform set of guidelines, it reduces the chances of error. This means that various project teams can easily cross-check their work. It is beneficial to establish a clear template that outlines all the steps involved in creating a materials takeoff. Standardizing the way materials are categorized, quantified, and priced can streamline workflow.
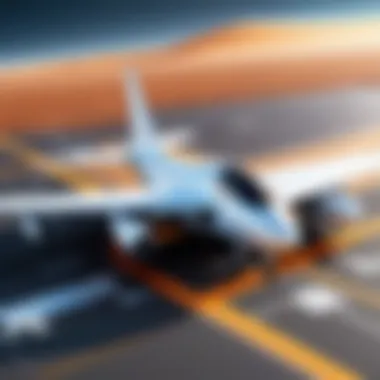

Regular training sessions can help reinforce these standards. This ensures that all team members are familiar with updated practices and tools. Additionally, a standard process helps to keep everyone accountable, which is an essential factor in the successful management of construction projects.
Collaborating with Project Teams
Collaboration plays a vital role in producing an accurate materials takeoff. Effective communication between different teams—such as architects, engineers, and contractors—enhances the quality of information gathered. Each member brings unique insights that can help clarify project requirements and material specifications.
Utilizing collaborative software tools can also provide a platform for real-time updates and discussions. For example, systems like Procore or PlanGrid allow team members to share updates instantly. This reduces misunderstandings and helps to correct any discrepancies early in the planning process.
Working together not only boosts efficiency but also nurtures a shared understanding of project goals, which is beneficial for morale and overall productivity.
Regular Updates and Reviews
Continuous evaluation of the materials takeoff is essential. As project dynamics shift, new requirements may arise, or material costs may fluctuate. Conducting regular reviews ensures that the materials takeoff remains accurate and relevant throughout the project lifecycle.
Setting a schedule for updates can help maintain the integrity of the list. At each project phase, stakeholders should meet to discuss any changes or adjustments needed in the takeoff. These meetings can provide an opportunity to reassess material needs based on current project conditions. It is also advisable to keep a record of any changes made to the takeoff. This generates a trail of past decisions and helps in analyzing the impact of those changes.
Regularly reviewing and updating the materials takeoff list is not just a good practice but a necessary approach to effective project management.
Implementing these best practices contributes to a more efficient takeoff process. With a standardized approach, collaboration among teams, and regular updates, accuracy can greatly improve, ultimately leading to better project outcomes.
The Role of Technology in Materials Takeoff
In today’s construction and project management landscape, the role of technology in materials takeoff cannot be overstated. Integrating advanced technological solutions allows professionals to become more efficient in estimating material needs. It not only streamlines the takeoff process but also minimizes errors, thus resulting in more accurate project budgeting and planning.
The adoption of technology enhances the overall workflow, making it essential for professionals involved in construction projects. The key benefits include accuracy, efficiency, and the capacity to innovate. As the construction industry evolves, embracing technology can be a decisive factor in maintaining competitiveness.
Advancements in Software Solutions
Recent advancements in software solutions have transformed the materials takeoff process. Various programs now enable automated calculations and data management, significantly reducing the time required for manual takeoffs. Notable software options include Bluebeam Revu, PlanSwift, and Sage Estimating, which offer features tailored to streamline the entire estimation workflow.
These applications enhance user experience by allowing access to comprehensive databases of materials, pricing, and supplier information right at the user's fingertips. Additionally, advancements in mobile technology enable project managers to conduct takeoffs on-site, increasing accuracy while saving valuable time. The integration of Building Information Modeling (BIM) with takeoff software has further improved accuracy by providing three-dimensional models that give clearer insights into material requirements.
Integrating with Project Management Tools
Integration with project management tools is another significant aspect of the role of technology in materials takeoff. When materials takeoff software works seamlessly with project management platforms such as Microsoft Project or Primavera P6, it ensures that all stakeholders are on the same page from the beginning. This integration fosters better collaboration among teams, enabling streamlined communication regarding material requirements, timelines, and budgets. This holistic view helps reduce miscommunication and keeps projects running smoothly.
Furthermore, syncing data between these platforms enhances tracking and reporting capabilities. This allows decision-makers to analyze data in real-time, providing a basis for informed project adjustments. The ability to adjust estimates instantly as project parameters change is vital for staying on schedule and within budget.
Technology in materials takeoff not only improves accuracy but also fosters better collaboration across teams, leading to more successful outcomes.
As such, the intersection of technology and materials takeoff is fundamental to modern construction practices, driving efficiency and effectiveness in project execution.
Comparative Analysis of Takeoff Software
In the contemporary construction landscape, the use of technology is increasingly becoming pivotal. Within this context, conducting a comparative analysis of takeoff software is essential for professionals aiming to optimize their practices. An effective materials takeoff list is only as robust as the tools employed to create it. This analysis not only aids in identifying the most suitable software that aligns with operational needs but it also illuminates a variety of options available in the market.
Evaluating different software packages can reveal key features, usability levels, and integration capabilities with existing systems. This is vital for decision-makers who require clear insights before committing to a software solution, thus saving time and resources in the long run.
Top Software Solutions Available
Several notable software solutions have gained traction in the field of materials takeoff. Each option has distinct features. Here are a few:
- Bluebeam Revu: Known for its markup capabilities and collaboration features.
- PlanSwift: Offers a user-friendly interface that simplifies the estimation process.
- STACK: Focused on cloud-based solutions, it enables easy access to takeoff lists from any location.
- Takeoff Live: Emphasizes real-time collaboration between team members.
Choosing the correct software hinges on understanding these specialized features and how they meet specific project requirements.
Cost vs. Feature Analysis
When selecting takeoff software, the relationship between cost and features cannot be overlooked. It is crucial to ascertain whether the software justifies its price through robust functionality. Here are some considerations:
- Initial Cost vs. Long-term Value: Low-cost options may offer limited features leading to higher long-term costs due to inefficiencies.
- Licensing Models: Some software comes with subscription models that might be more cost-effective over time compared to one-time purchase solutions.
- Integration Costs: The ability to integrate with existing project management tools can significantly affect total costs.
- User Support and Training: Evaluate the support offered with the software, as this can influence productivity during implementation.
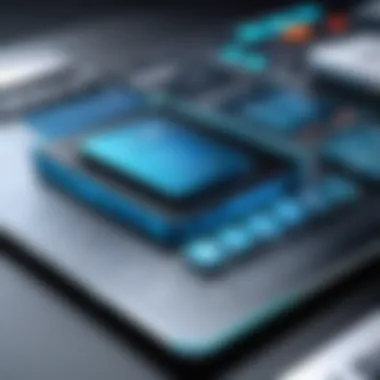

"A careful assessment of both cost and feature set is necessary to ensure an informed decision in selecting the proper software for takeoff processes."
Lastly, it’s beneficial to read reviews and case studies of the software in action. Feedback from other users can provide valuable insights into everyday application and help determine which option best meets the organization’s requirements.
Impacts of an Accurate Materials Takeoff List
An accurate materials takeoff list is integral to the success of construction projects. The precision of this list not only affects the budgeting process but also plays a crucial role in procurement and project scheduling. Discrepancies in material estimations can lead to inflated costs, delayed timelines, and various complications that might derail a project. Understanding the impacts of an accurate takeoff list will provide stakeholders with insights necessary to enhance overall project efficiency.
Enhancing Project Budgeting
When it comes to budgeting, a precise materials takeoff list directly influences cost allocation. Having a clear understanding of material requirements enables project managers to create more accurate budgets. This includes direct material costs, potential waste factors, and even market fluctuations. Accurate estimations can prevent overruns and ensure that funds are available when needed. Additionally, having quantifiable data allows for better forecasting and financial planning, thus reducing unexpected expenditures down the line.
Streamlining Procurement Processes
An effective materials takeoff list aids in streamlining procurement processes. By clearly identifying what materials are necessary and in what quantities, procurement teams can negotiate better prices and delivery schedules with suppliers. This efficiency reduces the time spent on sourcing and can lead to cost savings as bulk purchases are often more economical. With a sharp focus on what is needed, teams can also avoid the common pitfalls of under-ordering or over-ordering materials, ensuring that the project remains on schedule and within budget.
Improving Project Timelines
Accurate takeoff lists are vital in improving project timelines by allowing for better planning and resource allocation. When material needs are accurately mapped out, project managers can create more realistic timelines that account for the procurement and delivery phases. This foresight helps to minimize work delays, leading to smoother workflow on the job site. As a result, construction professionals can anticipate and mitigate risks associated with scheduling conflicts. Managing timelines effectively significantly contributes to project success and client satisfaction.
The impacts of an accurate materials takeoff list are profound, affecting budgeting, procurement, and timelines alike.
Case Studies in Effective Materials Takeoff
In understanding the materials takeoff list, examining real-world case studies is essential. These examples contribute valuable insight into the actual application of techniques and tools involved in materials estimation. They illustrate both successful implementations and where challenges arose, helping professionals learn from each scenario. Such case studies reinforce the significance of accurate takeoff lists in the broader context of project management, highlighting their role in enhancing efficiency, reducing costs, and ensuring project deadlines are met.
Successful Projects Leveraging Accurate Takeoffs
Successful construction projects often share one common thread: an accurate materials takeoff. For instance, consider a recent commercial building project that employed an advanced takeoff software. By utilizing tools like AutoCAD and PlanSwift, the project team was able to precisely calculate material needs, leading to:
- Reduced waste
- Optimized procurement processes
- Timely project completion
The team collaborated closely with suppliers, ensuring that materials were sourced and delivered according to the project timeline. The emphasis on effective communication and planning was crucial, as it minimized delays and avoided disruptions in the workflow. The result was a project that not only stayed within budget but also exceeded client expectations in terms of quality and delivery.
Lessons Learned from Misestimation
On the opposite end of the spectrum are projects that faced significant challenges due to misestimations in materials takeoff. One notable case involved a residential development where initial estimates were based on outdated plans. This oversight led to:
- Unexpected material shortages
- Increased costs for expedited orders
- Project delays of several weeks
The key takeaway from such scenarios is the critical importance of staying updated on material requirements and costs throughout the lifecycle of a project. Regularly revisiting estimates can prevent many of the pitfalls that lead to budget overruns and delays. Communication among all stakeholders—from architects to contractors—is paramount to ensure that everyone is aligned with the latest information.
"Learning from the mistakes in misestimations is as valuable as celebrating our successes. Each project paves the way for improved practices in the future." - Industry Expert
In summary, the exploration of case studies in effective materials takeoff not only showcases the successes but also highlights the missteps that can occur. These insights are essential for decision-makers aiming to refine their estimation processes and improve overall project outcomes.
Closure and Future Trends
The conclusion of this guide provides an essential overview of the materials takeoff list's role within the construction and project management sectors. This closing section reflects on the significance of maintaining an accurate and detailed takeoff list. It also foreshadows future trends that can impact the accuracy and efficiency of materials estimation.
With technology advancing rapidly, the traditional methods of materials takeoff may evolve significantly. Companies should be aware of these changes. The implication of these advancements is substantial, allowing for better estimation, reduced costs, and more streamlined processes.
Summary of Key Insights
Throughout this article, several critical insights have emerged regarding materials takeoff lists. Here is a brief recap:
- Precision is Key: Accurate estimation reduces waste.
- Tech Integration: Using software tools enhances accuracy.
- Collaboration Matters: Engagement among teams improves the quality of takeoffs.
- Regular Updates: Frequent revisions help in adjusting to cost changes.
These insights emphasize the need for ongoing education in the techniques of compiling and assessing materials takeoff lists.
Anticipating Future Developments
Looking ahead, we can identify several potential developments that may shape how materials takeoff lists are utilized:
- Increased Automation: Automation via AI and machine learning can enhance estimation practices. This will allow for faster and more precise calculations.
- Cloud-Based Solutions: These offer improved accessibility and collaboration. Teams can work across locations seamlessly, sharing real-time data.
- Enhanced Analytics Tools: Data analytics could transform how materials data is approached, offering deeper insights into trends and costs over time.
- Sustainability Factors: Increasing focus on sustainability may lead to new metrics in materials selection and evaluation, influencing procurement strategies.
Keeping an eye on these trends will equip decision-makers with the necessary foresight to adapt strategies effectively.