Mastering Inventory Bookkeeping for Business Success
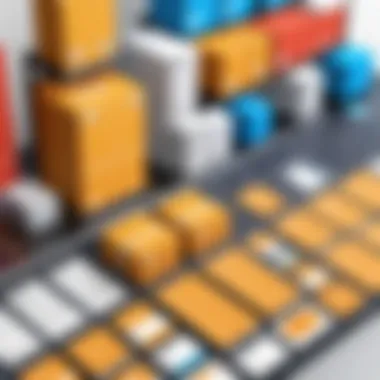
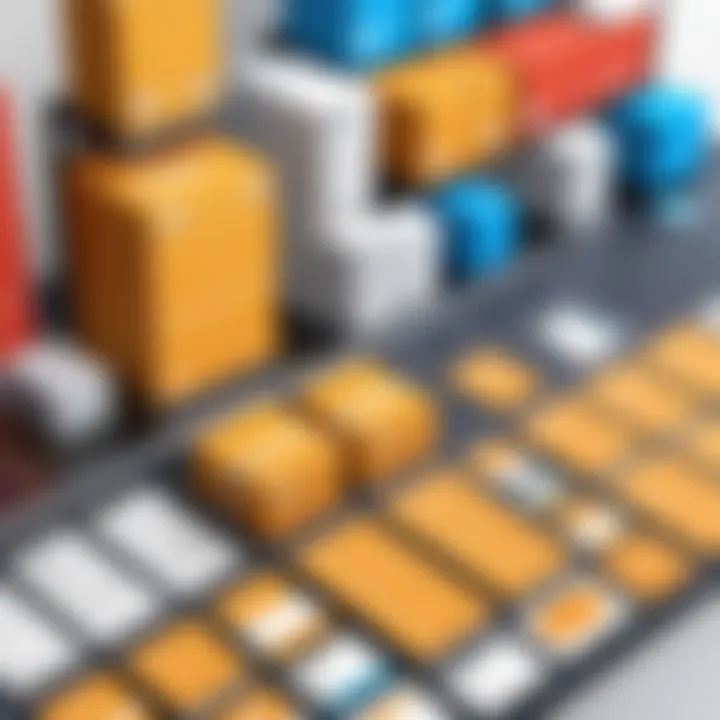
Intro
Inventory bookkeeping is crucial for businesses of every size. Understanding inventory levels can determine not just operational efficiency but also profitability. Effective management of inventory involves tracking quantities, costs, and movements of goods. This area has become more complex with the rise of technology, changing the way businesses approach their inventory systems.
In this detailed guide, we will explore various aspects of inventory bookkeeping. We'll discuss key methodologies, the importance of technology, and the operational challenges that arise. Each section aims to equip decision-makers, IT professionals, and entrepreneurs with the knowledge required to improve inventory management.
Through comprehensive analysis, readers will gain insights into the methodologies for effective management. We will also highlight how technology has transformed this field, enhancing both efficiency and accuracy. Compliance with regulations is another critical topic we will examine. Each of these elements plays a vital role in ensuring successful inventory practices that can lead to improved profitability within various sectors.
As we begin, it’s essential to understand not just the ‘how’ of inventory bookkeeping, but also the ‘why’ behind different practices. This knowledge provides a robust framework to tackle the complexities faced in inventory management today.
Understanding Inventory Bookkeeping
Inventory bookkeeping is a crucial aspect of any business that deals with physical goods. It involves tracking and managing inventory, calculating costs, and ensuring that financial records accurately reflect the company's assets. A clear grasp of inventory bookkeeping is essential for decision-makers since it directly impacts the bottom line.
Definition and Purpose
Inventory bookkeeping refers to the methods and systems used to record and manage a company's inventory. This process includes monitoring stock levels, documenting purchases and sales, and determining inventory value. The primary purpose of inventory bookkeeping is to provide accurate information about a company’s inventory status, which helps in planning and decision-making. An efficient inventory bookkeeping system also reduces excess stock, minimizes waste, and ensures that resources are utilized effectively.
Moreover, it allows businesses to maintain customer satisfaction by ensuring that products are available when needed. Overall, a solid inventory bookkeeping system supports the operational needs of a business and underpins its profitability.
Importance in Financial Reporting
In the realm of financial reporting, accurate inventory bookkeeping is vital. It plays a significant role in determining the financial health of a business. Inventory is considered a current asset on the balance sheet, and miscalculating inventory levels can lead to misleading financial statements.
Inventory impacts the Cost of Goods Sold (COGS), gross profit, and ultimately net income. Hence, discrepancies in inventory records can distort a company's financial performance metrics.
Accurate inventory data contributes to reliable financial reporting, which is essential for investors and stakeholders who rely on this information to make informed decisions about their investments.
Furthermore, consistent inventory reporting aids compliance with accounting standards such as GAAP and IFRS, necessitating businesses to adhere to specific principles in their bookkeeping practices. Thus, businesses must prioritize inventory bookkeeping as a critical element of their overall financial strategy.
Key Components of Inventory Management
Effective inventory management is essential for businesses aiming to optimize their operational efficiency. This involves understanding various components that play critical roles in maintaining accurate records and minimizing costs.
The key components of inventory management include the types of inventory held by a business and the methods used for inventory valuation. Each of these elements significantly contributes to the overall success of inventory bookkeeping.
By comprehensively understanding the key components, businesses can implement practices that enhance productivity and ensure better financial reporting.
Types of Inventory
Types of inventory can be broadly classified into three categories: raw materials, work-in-progress, and finished goods. Understanding these categories helps businesses manage their inventory effectively.
Raw Materials
Raw materials serve as the foundation for production processes. These are the essential components necessary for creating finished products. A key characteristic of raw materials is their inherent unpredictability in price and availability, which can affect production schedules.
Raw materials are a beneficial choice in this guide because they lay the groundwork for operational efficiency. A unique feature of raw materials is that their timely acquisition can lead to substantial cost savings in production. However, it requires proper planning and supplier management.
Work-in-Progress
Work-in-progress (WIP) inventory represents items that are in the production pipeline but are not yet complete. This type serves as an important bridge in the process of converting raw materials into finished goods. A key characteristic of WIP is its potential to accumulate costs, which can complicate accounting practices.
WIP is significant for this article as it emphasizes the need for tracking semi-finished products accurately. One unique aspect is that WIP requires continual monitoring to avoid production bottlenecks. However, high WIP levels can increase carrying costs, thus underlining the importance of efficient production management.
Finished Goods
Finished goods are products that have completed the manufacturing process and are ready for sale. Their key characteristic is their direct relation to customer demand. Finished goods are a popular focus as they represent the end product and revenue potential.
The unique feature of finished goods is that they must be properly stored and managed to fulfill orders efficiently. However, overstocking finished goods can lead to increased holding costs and potential waste, emphasizing the need for accurate demand forecasting.
Inventory Valuation Methods
Inventory valuation methods are crucial in determining the cost of goods sold and ultimately impacting profitability. Understanding these methods provides insights for better financial reporting and inventory management.
First-In, First-Out (FIFO)
FIFO is an inventory valuation method where the oldest inventory items are sold first. A key characteristic of FIFO is its ability to align with the actual flow of goods for many businesses. FIFO is advantageous as it reflects the current market value for inventory on hand, helping businesses report higher profits during periods of inflation.
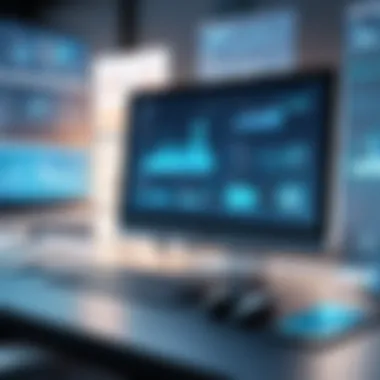
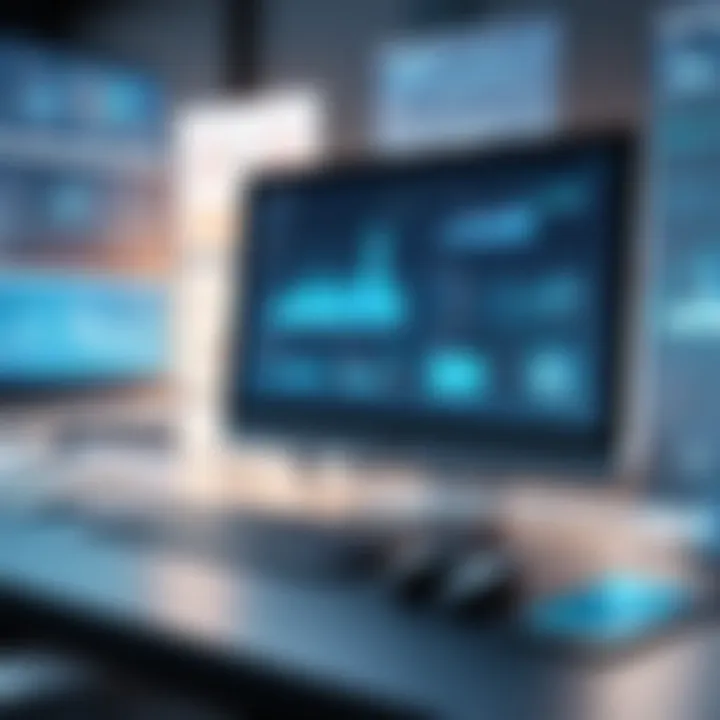
A unique feature of FIFO is its straightforward approach, but relying solely on this method can misrepresent inventory costs during volatile market conditions.
Last-In, First-Out (LIFO)
In contrast, LIFO assumes that the most recently acquired inventory items are sold first. This method is particularly beneficial during times when costs are rising because it allows businesses to lower their taxable income. The key characteristic of LIFO is its ability to match current costs against current revenues, providing a tax advantage.
However, LIFO can lead to outdated inventory values on the balance sheet, which could mislead investors and management alike.
Weighted Average Cost
The weighted average cost method averages the cost of all available inventory. A key characteristic of this method is its simplicity and ability to smooth out price fluctuations over time. It is a beneficial choice for businesses with high volumes of similar items, such as retail.
A unique feature of the weighted average method is that it helps manage cost variance, but it may not accurately reflect the actual flow of inventory, thus affecting financial reporting.
Understanding these inventory types and valuation methods equips businesses with the knowledge to maintain accurate financial records and ensure effective inventory control.
Principles of Accurate Inventory Tracking
Accurate inventory tracking is a cornerstone of effective inventory management. Without precision in tracking, businesses may face substantial risks, including financial discrepancies, lost sales, and customer dissatisfaction. The principles of accurate inventory tracking encompass methodologies and practices that ensure inventory levels reflect actual stock on hand. This not only promotes better decision-making but also enhances operational efficiency.
Regular Auditing Practices
Regular auditing practices are essential for recognizing discrepancies and ensuring that inventory records align with physical counts. These audits should be scheduled at fixed intervals, such as monthly or quarterly, depending on the nature and scale of the business. Conducting physical counts allows businesses to identify unrecorded loss, theft, or damage to stock. Verification can fall under several categories:
- Full Inventory Count: Conducted periodically, a full count checks every item in stock. This comprehensive approach is resource-intensive but reveals systemic issues.
- Cycle Counting: A more flexible approach, cycle counting involves counting a portion of the inventory on a rotating schedule, minimizing disruptions and maintaining focus on high-value items or those with faster turnover.
Organizations should implement strict protocols during audits to ensure accuracy. This includes training staff on counting methods, utilizing technology for data entry, and maintaining detailed records to track changes over time. In doing so, companies can enhance their inventory accuracy, which is vital for solid financial reporting and operational efficiency.
Inventory Reconciliation Processes
Inventory reconciliation processes bridge the gap between recorded data and physical inventory. This process typically occurs after audits to address any discrepancies discovered during counts. Businesses should establish systematic methodologies for reconciling records to ensure consistency across their operations.
These reconciliation processes often include:
- Comparison of Reports: Matching stock levels and sales reports against physical counts helps to highlight inconsistencies in inventory records.
- Adjustments for Errors: Following discrepancies, businesses should investigate their causes, whether through data entry mistakes or accounting errors. Appropriate adjustments should be recorded to reflect an accurate inventory status.
- Documenting Procedures: Proper documentation of adjustments is essential. This includes the reasons for discrepancies, corrective actions taken, and approvals from responsible parties.
The effectiveness of reconciliation processes relies on consistent application of best practices and adequate training for staff. Adopting a disciplined approach to inventory reconciliation not only assures accuracy in financial reporting but also supports better purchasing decisions and improves overall inventory management.
"Effective inventory management is not merely about stock levels. It is about managing how that stock flows through an organization."
Through regular auditing and rigorous reconciliation processes, businesses can foster a culture of accountability and efficiency in inventory management, ultimately leading to enhanced operational performance.
Technological Innovations in Inventory Bookkeeping
The realm of inventory bookkeeping is increasingly influenced by technological innovations. Businesses are recognizing that incorporating advanced technologies can significantly enhance their inventory management processes. The integration of these solutions results in improved accuracy, efficiency, and streamlined operations. This section explores crucial technological aspects, including inventory management software and the role of artificial intelligence.
Inventory Management Software
Effective inventory management software is crucial in maintaining control over stock levels, order processing, and overall inventory tracking. Companies benefit from selecting the right tools that fit their specific needs.
Key Features to Consider
When evaluating inventory management software, several key features can greatly influence its effectiveness:
- Real-time Tracking: This feature allows businesses to monitor stock levels and locations instantaneously. Real-time data minimizes the risk of stockouts and overstock situations.
- User-Friendly Interface: A software program should be easy to navigate, facilitating adoption and minimizing training time for staff members.
- Reporting and Analytics: Comprehensive reporting tools enable businesses to analyze inventory trends, making it easier to forecast demand and adjust strategies accordingly.
The inclusion of these features makes inventory management software a favored choice among organizations. One unique characteristic is the ability to automate reporting processes. This saves time and reduces errors, aligning perfectly with goals of efficiency in inventory management.
Benefits of Automation
Automation is a core benefit of modern inventory software. Automated systems reduce the need for manual tasks, which can be error-prone and labor-intensive.
- Increased Efficiency: Automation speeds up inventory processes, allowing for quicker response to changes in stock levels.
- Accurate Reporting: Automated tools generate accurate reports swiftly, enabling precise monitoring of inventory levels and trends.
One unique aspect of automation is the easy integration with other business systems, such as accounting or sales platforms. This integration brings up advantages, including enhanced data consistency across systems and timely communication between various departments.
Impact of Artificial Intelligence
Artificial intelligence (AI) is shaping the future of inventory bookkeeping by offering solutions that enhance decision-making processes and operational efficiency. Understanding AI’s capabilities provides companies with tools to anticipate trends and optimize resources.
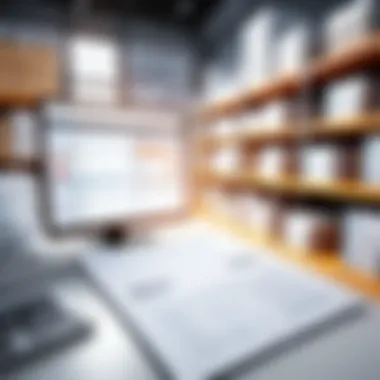
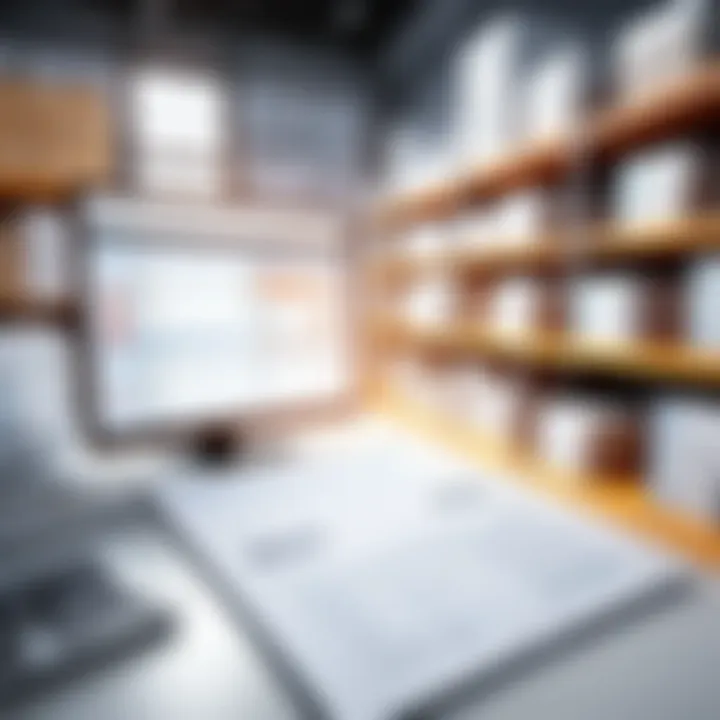
Predictive Analytics for Demand Forecasting
Predictive analytics utilizes historical data to forecast future demand. This method is critical in managing stock levels effectively.
- Improved Accuracy: By analyzing patterns and trends, businesses can make informed decisions regarding procurement and inventory distribution.
- Cost Efficiency: Accurate forecasts can help avoid excess inventory costs, contributing to better cash flow management.
A notable feature of predictive analytics is its capacity to continuously learn and adapt based on new data inputs. This adaptive learning helps businesses remain agile and responsive in dynamic markets.
Operational Efficiency through Smart Inventory
Smart inventory management powered by AI aims to enhance operational efficiency by automating various tasks.
- Optimized Stock Levels: AI models can calculate optimal stock levels based on various parameters, helping reduce waste and improve turnover rates.
- Reduced Human Error: By minimizing manual entry, businesses can significantly reduce errors that lead to inventory discrepancies.
One unique feature of smart inventory systems is their ability to integrate with the Internet of Things (IoT) devices, allowing for seamless synchronization of inventory data. This capability provides advantages in real-time updates and decision making, establishing a more intuitive inventory system.
Staying ahead in inventory bookkeeping is no longer just about efficient processes—it's about leveraging technology to make smarter choices.
Challenges in Inventory Bookkeeping
Inventory bookkeeping is vital for the success of any business that deals with products. It involves constant tracking of inventory levels, orders, sales, and deliveries. Despite its importance, this area presents multiple challenges that businesses face regularly. Understanding these challenges is crucial for decision-makers and professionals looking to enhance their inventory management systems. Addressing issues related to common errors and risk management can significantly improve overall efficiency and accuracy in financial reporting.
Common Errors and Mismanagement
Common errors in inventory bookkeeping can result from a variety of factors, including human mistakes, outdated systems, and lack of training. Some of the notable errors include:
- Data Entry Mistakes: Incorrectly inputting quantities or prices can skew inventory records.
- Miscounting: Errors during physical counts may lead to discrepancies between actual and recorded inventory levels.
- Overlooking Obsolete Stock: Failing to identify items that are no longer sellable can falsely inflate inventory valuation.
- Inaccurate Supply Chain Information: Unreliable data from suppliers or delivery delays complicate inventory management.
- Failure to Adapt to Market Changes: Businesses that do not respond to shifts in demand may find themselves overstocked or understocked, leading to loss of revenue.
These errors can culminate in financial discrepancies, leading to larger issues in financial reporting, ultimately impacting business decisions. Therefore, it is essential for organizations to implement measures to reduce the occurrences of these errors.
Strategies to Mitigate Risks
To counter common inventory challenges, companies can adopt various strategies aimed at minimizing errors and optimizing management processes:
- Implement Regular Training: Continuous training ensures that staff are updated on best practices regarding inventory management. This can include training on software as well as physical counting methods.
- Use Technology: Embracing inventory management software such as Fishbowl or QuickBooks can automate processes. Technology often reduces human error and increases accuracy in data handling.
- Set Standard Operating Procedures (SOPs): SOPs help ensure that everyone follows the same processes, promoting consistency across the board.
- Conduct Regular Audits: Regular audits of inventory can help pinpoint discrepancies quickly. This allows businesses to address problems before they escalate into more significant issues.
- Maintain Clear Communication: Engaging with suppliers regularly helps organizations stay on top of delivery schedules and changes in product availability.
Addressing these challenges is not only about preventing mistakes but also about creating a resilient system where risks are managed proactively.
"It is easier to prevent bad inventory practices than to correct them after they have caused financial damage."
Understanding the intricacies involved in inventory bookkeeping challenges will help companies improve their management strategies. As businesses grow and evolve, so must their approaches to inventory accountability.
Regulatory Compliance and Standards
Regulatory compliance and standards in inventory bookkeeping are essential for maintaining transparency and accuracy in financial reporting. Understanding these regulations is crucial for organizations aiming to ensure compliance and reduce risks associated with mismanagement. Being aware of GAAP and IFRS regulations helps businesses align their inventory practices with recognized standards, fostering trust with stakeholders.
Compliance with regulatory standards promotes a reliable framework for recording and reporting inventory data. Additionally, it ensures that the company adheres to the legal obligations mandated by various authorities. Therefore, it is necessary to stay updated with the changing regulations and implement practices that comply with them.
Regulatory compliance isore than just a legal duty; it is a strategic necessity for maintaining credibility and operational efficiency.
Understanding GAAP Principles
The Generally Accepted Accounting Principles (GAAP) set the standard for financial reporting and bookkeeping. They provide a clear framework for reporting inventory, allowing companies to present their financial position accurately. GAAP ensures consistency in how inventory is valued, which is crucial for comparing financial statements over time.
Key elements of GAAP in inventory management include:
- Consistency: Businesses must consistently apply the same inventory valuation method.
- Relevance: The information presented must be relevant to decision-making processes.
- Reliability: Financial reports must accurately reflect the company’s operations, showing honest data.
Following GAAP helps companies in establishing credibility with investors and regulators. It facilitates improving operational strategies based on accurate data analysis.
International Financial Reporting Standards
International Financial Reporting Standards (IFRS) are vital for organizations operating globally or those considering international expansion. IFRS provides guidelines that are universally recognized, making it easier for businesses to connect with international investors and partners.
Some critical aspects of IFRS in inventory bookkeeping include:
- Fair Value Measurement: IFRS often requires businesses to measure inventory at fair value, which can offer a more accurate reflection of current market conditions.
- Disclosure requirements: IFRS mandates detailed disclosures about inventory valuation methods and the criteria used for recognition, thus increasing transparency.
- Consistency across borders: Using IFRS allows for easier comparisons across different international companies, enhancing stakeholders' understanding.
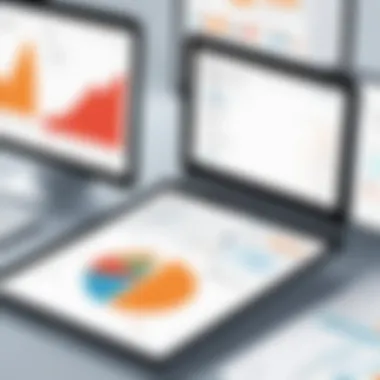
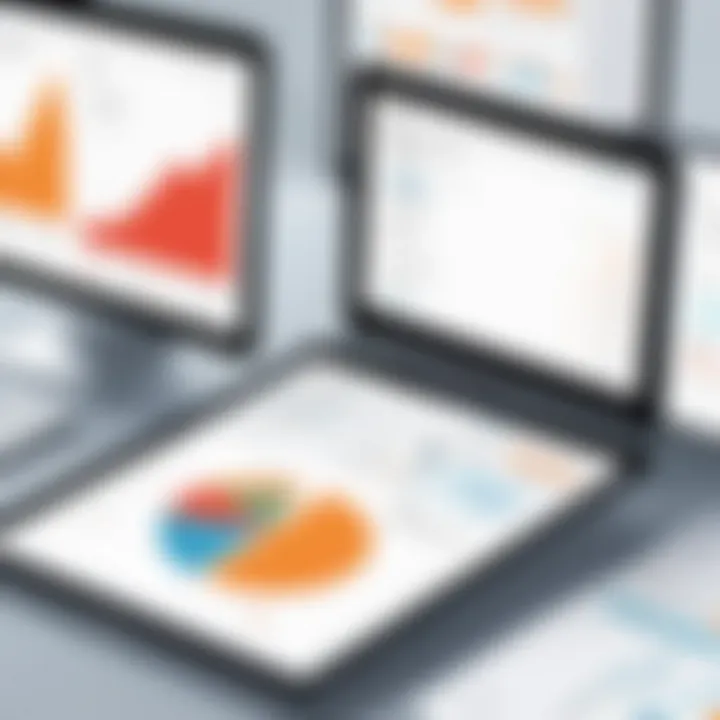
Overall, embracing IFRS can greatly benefit businesses in increasing their global standing and appealing to a broader base of investors and consumers.
Best Practices for Effective Inventory Bookkeeping
Effective inventory bookkeeping is an essential element of successful business operations. It is important because precise inventory management directly influences profitability. Adopting best practices ensures that a business maintains accuracy in its records, facilitates compliance with regulations, and enhances decision-making based on reliable data.
Establishing Standard Operating Procedures
Standard Operating Procedures (SOPs) are the backbone of consistent practices in inventory bookkeeping. They provide a framework that guides staff on how to manage inventory effectively. SOPs encompass various aspects, including inventory receiving, storage, tracking, and shipping processes.
Implementing SOPs can lead to numerous benefits:
- Consistency: By having clear guidelines, all team members understand their responsibilities and tasks. This leads to uniformity in how inventory is handled, minimizing discrepancies.
- Efficiency: Streamlined procedures reduce wasted time. Staff can focus on their tasks knowing what steps to follow, which directly impacts productivity.
- Error Reduction: A well-documented process limits the chances of mistakes during inventory handling. This is crucial in maintaining accurate records and reducing losses.
To establish effective SOPs, businesses should consider the unique aspects of their inventory system. Regular reviews and updates of these procedures should occur to adapt to changing business needs and technological advancements.
Training Staff for Inventory Accuracy
Staff training is vital to achieving high levels of inventory accuracy. Knowledgeable employees can better manage and update inventory records, directly affecting the effectiveness of bookkeeping. Training should cover various areas:
- Understanding Inventory Systems: Employees must grasp how the inventory management software works. This includes knowing how to input data accurately and run reports.
- Inventory Counting Techniques: Regular counting practices, such as cycle counting, should be taught. Staff needs to understand how to conduct counts correctly to prevent errors.
- Awareness of Policies and Procedures: Training should also focus on the importance of SOPs. This encourages adherence to best practices across the board.
Investing time and resources into training not only pays off in increased accuracy but also fosters a culture of accountability. When staff members can see the impact of their work on the bottom line, they tend to be more engaged and diligent in their tasks.
"An accurate inventory system is not solely a function of technology; it is the result of aligned people and processes."
By implementing these best practices in inventory bookkeeping, businesses can enhance operational efficiency and ensure reliable financial reporting.
Case Studies and Real-World Examples
Understanding real-world applications of inventory bookkeeping is vital for professionals in this field. Case studies provide insights that theoretical knowledge alone cannot deliver. These examples showcase how businesses successfully implement innovative strategies. They also highlight the pitfalls to avoid.
Successful Inventory Innovations
One key benefit of studying successful inventory innovations lies in the practical lessons learned from these real-world scenarios. For instance, Walmart’s use of RFID (Radio-Frequency Identification) technology changed inventory management paradigms. This technology allows for real-time tracking of inventory levels and significantly reduces loss and theft. Companies can adjust their stock levels immediately, ensuring a better match between supply and demand.
Another noteworthy example is Amazon. Their advanced robotics systems automate the picking and packing process. This innovation demonstrates the efficiencies gained when integrating technology with inventory processes. The real-world applications stress the importance of staying ahead in adopting new solutions. Companies can benchmark their practices against leaders in the industry and adapt accordingly.
- Key takeaways from successful innovations include:
- Leveraging technology for efficiency.
- Continuous improvement and adaptation of new systems.
- Learning from industry leaders to drive progress.
Lessons Learned from Inventory Failures
Learning from failures in inventory management is as crucial as celebrating successes. Several high-profile cases illustrate essential lessons. For example, Target’s expansion into Canada faced significant inventory management challenges. The company struggled with mismatches in supply and demand. This resulted in empty shelves and lost sales. Such issues underline the importance of thorough market research and accurate demand forecasting.
Similarly, the automotive industry often deals with inventory visibility problems. Companies like Ford once faced significant production delays due to improper inventory tracking. The issue highlighted the need for robust inventory auditing practices.
- Vital lessons from these failures include:
- Conducting rigorous market analysis before expansion.
- Ensuring that supply chain management systems have real-time data.
- Implementing regular audits to guarantee inventory accuracy.
Understanding both successful innovations and failures creates a richer perspective on inventory bookkeeping. It encourages decision-makers to adopt best practices and avoid common pitfalls.
Future Trends in Inventory Management
Inventory management is continually evolving. The integration of advanced technologies and shifting market demands necessitate a reassessment of traditional practices. Understanding future trends is crucial for decision-makers aiming to optimize their operations. These trends encompass innovations like blockchain technology and sustainability considerations. Thus, a focus on these elements provides insight into how businesses can remain competitive.
The Role of Blockchain Technology
Blockchain technology is making significant strides in inventory management. Its decentralized and transparent nature allows for greater trust among stakeholders. Records on a blockchain are immutable, which means data cannot be altered retroactively without consensus. This feature enhances accuracy in inventory bookkeeping.
Moreover, blockchain enables real-time tracking of inventory. Stakeholders can access the same data simultaneously, leading to effective collaboration across supply chains. This transparency reduces discrepancies, minimizes fraud, and enhances accountability. By implementing blockchain solutions, businesses can streamline operations and improve accuracy significantly.
In addition, smart contracts can automate many processes. For instance, a contract could automatically trigger replenishment orders when stock levels reach a predetermined threshold. This reduces human error and improves efficiency in real-time inventory management.
"Blockchain technology offers not just security, but also a comprehensive solution for managing supply chains effectively."
Sustainability Considerations
Today’s market increasingly values sustainability. Consumers are more conscious of environmental impacts, pushing companies to reconsider their inventory practices. Sustainable inventory management focuses on reducing waste, improving resource efficiency, and minimizing carbon footprints.
One consideration is optimizing supply chain logistics. By analyzing data on inventory levels and demand trends, businesses can reduce excess stock. Maintaining optimal inventory levels not only saves cost but also acts toward reducing overproduction and its subsequent waste.
Additionally, adopting eco-friendly packaging and materials can enhance a company’s reputation. Businesses that prioritize sustainable practices often attract environmentally conscious consumers, thus fostering brand loyalty. Investing in energy-efficient technologies and transportation methods also aligns inventory management with sustainability goals.