Essential Guide to Landscape Equipment Maintenance Software
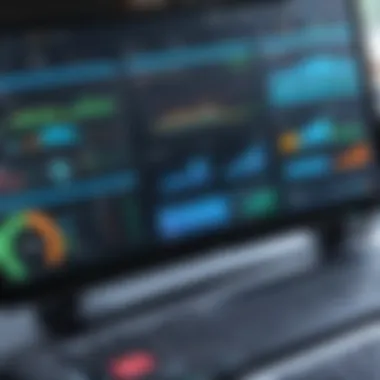
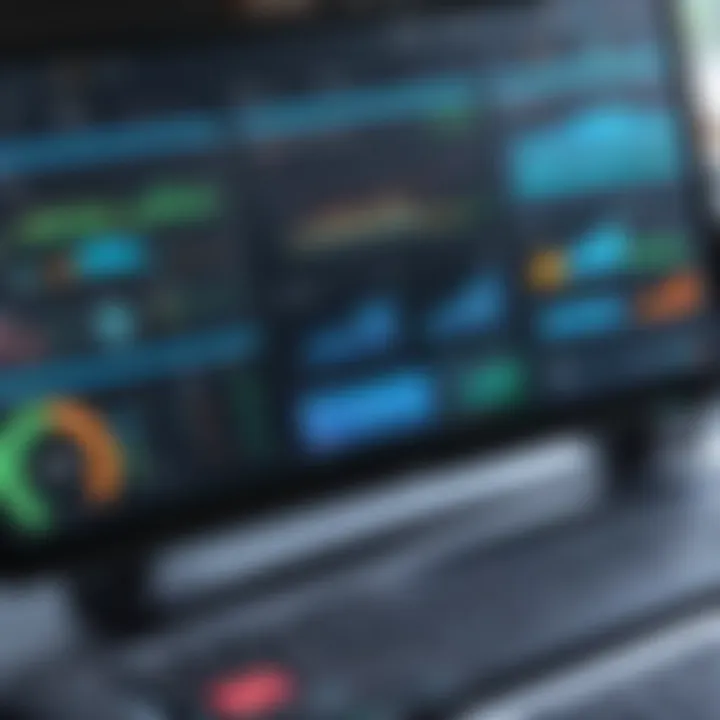
Intro
Landscape equipment maintenance software plays a pivotal role in the efficient management of landscaping businesses. In an industry where equipment uptime translates directly into productivity and profitability, understanding how to leverage this technology is essential. This guide delves into the key aspects of landscape equipment maintenance software, offering insights tailored for industry advisors who aim to support their clients with informed recommendations.
Software Overview
Brief Description of Software
Landscape equipment maintenance software is designed to streamline the upkeep and management of various landscaping tools and machinery. By facilitating regular maintenance tasks, tracking equipment usage, and managing repair schedules, this software supports businesses in primarily achieving optimal operational efficiency. It serves as a centralized hub where users can record service history, monitor machinery conditions, and plan preventive maintenance schedules.
Key Features and Functionalities
The most vital features of landscape equipment maintenance software include:
- Maintenance Tracking: Users can schedule routine maintenance and repair of equipment, effectively preventing unexpected downtime.
- Inventory Management: The software can keep inventory of parts and supplies, alerting users when stock is low.
- Report Generation: This feature enables businesses to generate detailed reports on equipment performance over time, helping identify trends or issues that may require attention.
- User Access Controls: Facilitating different access levels ensures that only authorized personnel can operate specific functions within the software.
- Integration with Other Systems: Many software options offer seamless integration with accounting, payroll, and project management systems, creating a more connected and efficient workflow.
Detailed Comparison
Comparison with Competitors
When evaluating landscape equipment maintenance software, it’s crucial to compare it with alternatives in the market. Key competitors may include software such as LawnPro, Fleet Complete, and MaintainX. Each has distinctive offerings:
- LawnPro focuses on smaller landscape businesses with a user-friendly interface.
- Fleet Complete provides robust fleet management features, catering well to larger enterprises.
- MaintainX excels in mobile access, enabling users to manage tasks on the go.
Understanding these differentiators helps advisors recommend the most suitable solution based on client needs.
Pricing Structure
Pricing structures for landscape equipment maintenance software can vary significantly. Many vendors offer subscription-based models where clients pay a monthly fee, while others may provide a one-time licensing option. Factors influencing price include:
- Number of Users: More users lead to higher costs.
- Feature Set: Advanced features often come at a premium.
- Integration Costs: Additional expenses may arise when integrating with other systems.
Potential users should assess the long-term costs and determine a budget that aligns with their operational needs.
"Choosing the right landscape equipment maintenance software is not just about functionality; it is about ensuring that the tool aligns with the specific challenges faced by the client’s business."
Understanding Landscape Equipment Maintenance Software
The landscape equipment maintenance software has become indispensable for businesses involved in landscaping and outdoor maintenance. Its role extends beyond basic functionality, offering a framework to enhance productivity while prolonging equipment lifespan. As landscape operations grow increasingly complex, understanding the nuances of this software is crucial for industry advisors.
Definition and Purpose
Landscape equipment maintenance software is a specialized tool designed to facilitate the planning, tracking, and execution of maintenance tasks related to landscaping machinery. Its primary purpose is to ensure that equipment operates at optimal levels, thereby reducing downtime and operational costs.
Here are some key purposes of this software:
- Centralized Management: It provides a centralized platform where fleet managers can log maintenance activities, view equipment status, and monitor performance metrics.
- Data-Driven Insights: The software analyses maintenance data, offering insights into equipment efficiency and performance trends over time.
- Task Scheduling: It helps in automating the scheduling of routine maintenance tasks, ensuring that no equipment suffers from neglect.
Role in Landscape Management
In the realm of landscape management, the software plays a multifaceted role. It is not only a tool for implementing maintenance strategies but also a platform that supports broader operational goals. Here are some roles that highlight its importance:
- Enhancing Operational Efficiency: By streamlining maintenance processes, organizations can minimize delays and optimize their operations.
- Reducing Costs: Timely maintenance can lead to fewer catastrophic failures, resulting in significant cost savings over time.
- Improving Safety: Well-maintained equipment is safer to operate, reducing the risk of accidents and equipment-related injuries.
In summary, understanding landscape equipment maintenance software is vital for industry professionals. It provides a strategic advantage in managing logistics, equipment performance, and ensuring long-term sustainability of operations in the competitive landscape industry.
Key Features of Maintenance Software
The landscape equipment maintenance software plays a critical role in enhancing operational efficiency. The features included in such software make it essential for companies managing large fleets or inventories of equipment. Each feature contributes to streamlined processes, reduced downtime, and improved resource allocation.
Asset Tracking and Management
Asset tracking is vital for any organization that relies on heavy machinery. It enables businesses to maintain a comprehensive overview of all equipment. With this feature, companies can easily track the location, usage, and status of each piece of equipment.
Management teams can make more informed decisions about asset usage and replacement. It also helps to prevent loss or theft of expensive machinery. For instance, if an equipment is frequently placed in a particular location, the team can ensure it is adequately maintained to prevent operational inefficiencies.
Work Order Management
Work order management simplifies the process of assigning tasks and tracking their completion. By providing a centralized platform for managing work orders, teams can easily prioritize tasks based on urgency or project requirements. Each work order can include details like budget, assigned personnel, and status updates.
This organized approach aids in effective communication among team members and helps in meeting deadlines. Collaborating on work orders enhances accountability and ensures that maintenance tasks are not overlooked. This is crucial for companies aiming to maximize equipment uptime.
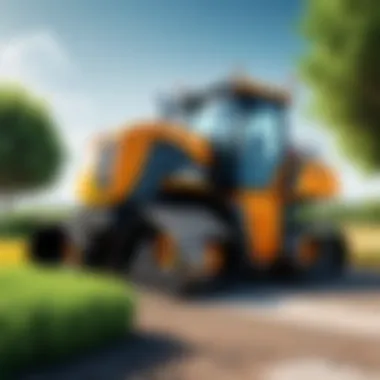
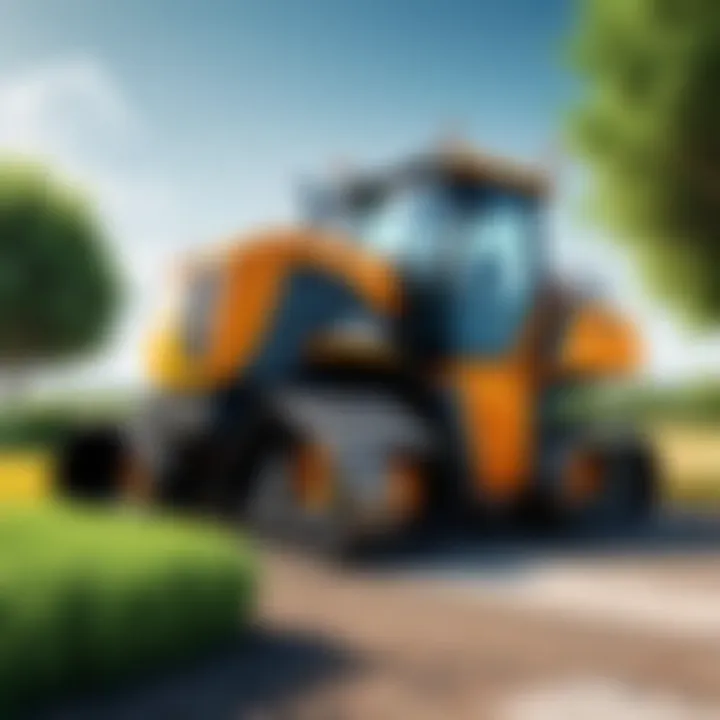
Maintenance Scheduling and Alerts
The maintenance scheduling feature helps organizations plan and automate regular maintenance tasks. By setting reminders and alerts, the software ensures that maintenance activities happen timely. This planning can prevent unexpected breakdowns, which could lead to costly repairs and lost productivity.
Automatic alerts keep teams informed of impending maintenance priorities. This proactive approach reduces equipment downtime significantly. Proper scheduling also contributes to longer equipment life by ensuring that routine services take place as required.
Reporting and Analytics
Analytics and reporting tools provide essential insights into equipment performance and maintenance history. This data is crucial for identifying trends and making informed decisions for future investments. Reports can help in measuring KPIs related to maintenance activities, operational efficiency, and costs.
Using analytics, businesses can pinpoint issues like recurring breakdowns. They can thus address the root cause effectively. This targeted approach to problem-solving ensures that resources are utilized effectively and helps maintain the competitive edge.
"Data-driven decision making is the cornerstone of modern equipment management."
In summary, the key features of maintenance software together create a cohesive tool for businesses. They simplify asset management and empower decision-making in landscape management. By understanding these features deeply, industry advisors can recommend effective solutions tailored to their clients' needs.
Benefits of Implementing Maintenance Software
Maintaining landscape equipment is crucial for operational success in the green industry. The effective use of maintenance software offers various advantages to businesses seeking to enhance their productivity and manage resources efficiently. This section delves into the specific benefits of implementing such software, focusing on how it can extend equipment lifespan, optimize operational efficiency, and contribute to cost reduction.
Increased Equipment Lifespan
The primary goal of maintenance software is to ensure that equipment remains in optimal working condition. By implementing a system that tracks and schedules maintenance tasks, businesses can prevent downtime caused by equipment failures. Timely interventions, such as routine inspections and necessary repairs, are essential. Regular maintenance not only mitigates the risks of unexpected breakdowns but also extends the overall lifespan of the machinery.
Some important points about increased lifespan include:
- Preventive Maintenance: This approach focuses on proactive actions rather than reactive measures. Regular checks reduce wear and tear.
- Optimal Usage: The software helps users understand how best to use their equipment, reducing strain on parts.
- Detailed Records: Keeping records of maintenance history helps identify patterns that could lead to future issues.
Regular maintenance is linked to longevity. Investing in maintenance software can lead to significant savings over time, primarily by postponing the need for replacements.
Enhanced Operational Efficiency
Operational efficiency is a crucial aspect of any landscape management strategy. By using maintenance software, businesses can streamline their operations, which translates to better allocation of resources and time.
Key points regarding operational efficiency include:
- Improved Communication: Many software solutions offer collaborative features, allowing teams to communicate about equipment status seamlessly.
- Task Prioritization: Managers can easily assign and prioritize maintenance tasks based on urgency and importance, thereby optimizing workforce productivity.
- Real-time Monitoring: Real-time alerts and updates keep managers informed on equipment status, enabling quick decision-making and responses.
The outcome of enhanced efficiency often results in increased client satisfaction. Equipment that works reliably and services that run smoothly establish a reputation for dependability in the competitive landscape industry.
Cost Reduction and Budgeting
Cost management is fundamental for any business. Maintenance software plays a vital role in promoting effective budgeting. By tracking maintenance tasks and costs, businesses can identify where funds are allocated and whether they can save in certain areas.
Critical aspects of cost reduction through maintenance software include:
- Reduction in Emergency Repairs: With proactive maintenance, the chances of having to deal with costly emergency repairs decrease significantly.
- Informed Purchasing Decisions: Maintenance history serves as a cornerstone for making informed buys for new equipment or parts.
- Budget Tracking: Many software solutions categorize expenses, allowing for better financial planning on equipment usage and repairs.
Implementing maintenance software leads to smarter spending. There is a balance between investing in maintenance and the cost of equipment downtime.
"An effective maintenance management system is an investment that pays off through efficiency improvements and cost savings over time."
In summary, implementing landscape equipment maintenance software provides advantages that extend beyond immediate operational aspects. It enhances equipment lifespan, boosts operational efficiency, and contributes significantly to cost management. As the landscape industry becomes more competitive, these benefits position businesses for sustainable success.
Choosing the Right Software
Selecting the appropriate landscape equipment maintenance software is a critical process for any business in the industry. The right choice can lead to improved workflow, better resource management, and ultimately, enhanced service delivery. This section delves into how to identify specific needs, evaluate software solutions, and understand pricing models.
Identifying Business Needs
The first step in choosing software is understanding the unique requirements of your business. Every landscape company has distinctive characteristics, including the size of the fleet, types of equipment, and overall operational goals. A thorough analysis should include:
- Current Challenges: What problems do you face associated with equipment maintenance? Are downtime and unplanned repairs frequent issues? Identifying these pain points will help you determine what features are necessary.
- Operational Scale: Are you managing a small team or a vast operation that involves multiple sites? Larger operations may require scalable solutions that can manage more assets.
- Future Growth: Consider not just current needs but what you might need down the line. Ensure the software can adapt as the business evolves, incorporating additional features without significant investement.
Taking time to outline these factors ensures that the chosen software aligns with business strategies and leads to meaningful results.
Evaluating Software Options
Once business needs are established, the next step is evaluating software options available in the market. This phase involves a deep dive into various products, focusing on functionality and overall fit.
- Feature Comparison: Look for software that covers essential features like asset tracking, work order management, and maintenance alerts. Each system has strengths and weaknesses, so it is vital to match features with your requirements.
- User Feedback: Real user experiences provide insights that can be invaluable. Review customer testimonials or look for case studies that demonstrate how the software has helped similar businesses.
- Demonstrations and Trials: Utilization of free trials or product demonstrations can help in assessing user interface and overall user experience. Engaging with the software firsthand provides a better understanding of how well it may integrate into your current processes.
- Support Services: Check what kind of customer support the software provider offers. Reliable customer service can significantly reduce downtime, especially when technical issues arise.
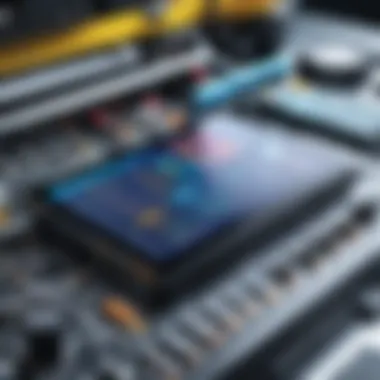
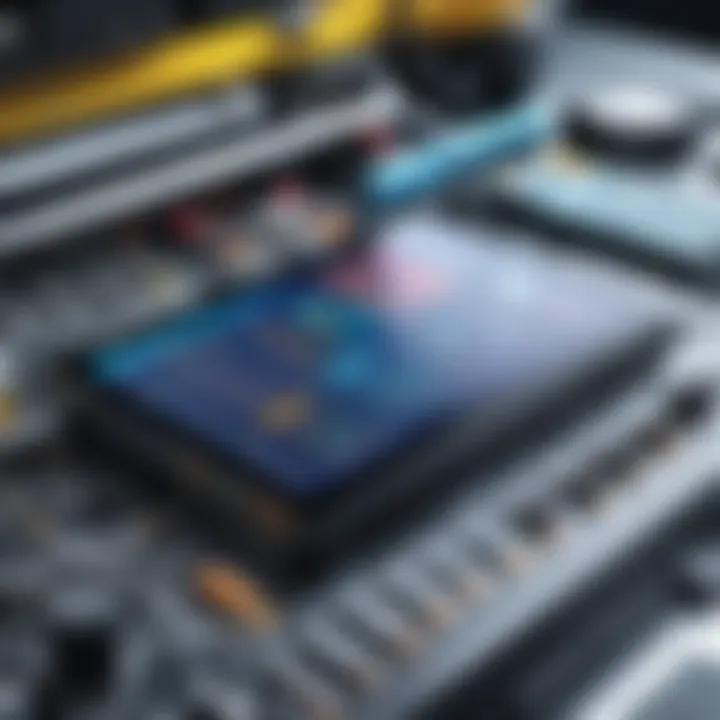
Understanding Pricing Models
The cost of maintenance software can vary widely, depending on the provider and functionalities. Understanding the different pricing models will assist in budgeting and ensuring the chosen software provides good return on investment. Some common pricing models include:
- Subscription-Based Pricing: Many software providers offer monthly or annual subscription fees, which can be economical. This model often includes updates and customer support as part of the package.
- One-Time Licensing Fee: This traditional model requires a lump sum payment for lifetime usage. While it may seem attractive, ongoing costs for updates and support could become burdensome.
- Freemium Models: Some software companies offer basic features at no charge, with advanced capabilities available through paid tiers. This can be helpful for businesses wishing to test functionality without a significant financial commitment.
Integration with Existing Systems
Integrating landscape equipment maintenance software with existing systems is a significant consideration for businesses. It ensures that operations run smoothly while maximizing the potential of new technologies. Companies often operate on various systems, including inventory management, accounting, and customer relationship management (CRM). Therefore, a well-planned integration strategy can enhance the overall functionality of these tools, contributing to better efficiency and data accuracy.
Compatibility Considerations
Compatibility among systems is a primary concern. Not all software solutions integrate seamlessly with legacy systems. Businesses should evaluate the technical specifications of any new software they consider, particularly interfaces and APIs.
Some important factors to examine include:
- Software Version: Ensure that both old and new systems can communicate. Updates on legacy systems may be necessary for compatibility.
- Data Formats: Check that data formats align. Issues can arise when transferring data if formats are incompatible.
- Operating Systems: Ensure that both systems can operate on a common platform to avoid connected issues.
- Vendor Support: Opt for solutions that provide support for integration. Vendors often have dedicated teams to assist with the transition.
By examining these characteristics, businesses can greatly lessen disruption during integration.
Data Migration Strategies
When integrating new maintenance software, effective data migration strategies are crucial. The process involves transferring data from existing systems to the new platform. A poorly executed migration can result in data loss or corruption. Here are several approaches to consider:
- Assess Data Quality: Before migration, it is vital to check the data for accuracy. Remove duplicates and irrelevant information to ensure only necessary data is transferred.
- Plan Migration Phases: Break down the migration into stages. This can help manage the workload and monitor the process effectively.
- Use Automated Tools: There are specific data migration tools designed to automate and streamline the transfer process. These can significantly reduce errors and time spent.
- Test Before Final Migration: Always run a test migration with a small data segment. This helps identify potential issues before transferring all data.
Implementing these strategies can aid in achieving a smooth transition to a new system. Successful integration ultimately enhances operational efficiencies and revitalizes equipment management practices.
Key takeaway: A successful integration of maintenance software relies on compatibility considerations and well-planned data migration strategies. This can lead to significant improvements in equipment management and service delivery.
User Considerations and Training
When implementing landscape equipment maintenance software, understanding user considerations and training needs is essential. This aspect is crucial because even the most advanced software can only be effective if users are comfortable and capable of using it.
The successful integration of software into daily operations often hinges on the ability of team members to adapt to new tools and processes. This consideration not only involves technical aptitude but also a willingness to embrace change. If users lack adequate training, they may struggle, leading to decreased efficiency and potential errors in equipment management. Thus, investing time and resources into appropriate training will lead to better outcomes and maximize the effectiveness of the chosen software.
User Interface and Experience
The user interface (UI) and overall experience play a fundamental role in how easily users can navigate the landscape equipment maintenance software. A clear, intuitive UI helps ensure that users can quickly find the information they need without unnecessary confusion. A complicated design can frustrate users and deter them from utilizing all available features.
Key elements that contribute to a positive user experience include:
- Simple Navigation: Users should not have to hunt through multiple menus to access critical functions. A streamlined navigational structure enhances usability.
- Clean Design: Visual clutter can distract and overwhelm users. A well-designed interface focuses on essential information and creates a more pleasant working environment.
- Responsive Features: Software must respond quickly to user inputs. Lagging or slow responses can hinder task completion and reduce user satisfaction.
Overall, a strong user interface facilitates engagement and fosters user adoption long-term. The more accessible the software is, the more likely it is that users will leverage its capabilities.
Training Requirements
Adequate training is paramount for users of landscape equipment maintenance software. It equips them with the skills required to operate the system proficiently. Training programs should be tailored to meet the specific needs of the users, as not all team members may have the same level of technical skills.
Considerations for effective training include:
- Training Formats: Various formats can be utilized, including in-person workshops, webinars, or self-paced online courses. Each format caters to different learning preferences.
- Duration: Training programs should provide sufficient time for users to absorb the material while also allowing for practice with the software.
- Ongoing Support: Follow-up sessions and resources should be available post-training. This ensures that users have continual support as they encounter challenges while using the software.
Successful training will enable users to perform tasks efficiently and will consequently lead to improved job performance. Users who are confident in utilizing the software are likely to take full advantage of its features, resulting in better management of landscape equipment and ultimately enhancing overall operational efficiency.
"Investing in user training reinforces the potential returns of the software by ensuring proper utilization and optimizing maintenance protocols."
By prioritizing user considerations and training, organizations can establish a foundation for effective software use, leading to enhanced equipment management processes.
Measuring Success
Measuring success in landscape equipment maintenance software is critical. It allows organizations to evaluate their performance and make informed decisions. By focusing on specific metrics, stakeholders can understand the impact of the software on their operations. This section identifies the key performance indicators and feedback mechanisms necessary for continuous improvement.
Key Performance Indicators
Key performance indicators (KPIs) are essential for monitoring the efficiency of landscape equipment maintenance software. KPIs can provide insights into how effectively the software is meeting the organization's needs. Here are some significant indicators to consider:
- Equipment Uptime: This measures the amount of time the equipment is in working condition. Higher uptime indicates better maintenance practices.
- Maintenance Costs: Analyzing the costs associated with maintenance helps in budgeting. Understanding these costs can lead to more effective financial planning.
- Response Time to Issues: Quick response to maintenance issues is vital. This KPI can reveal how promptly the maintenance team reacts to equipment failures.
- User Adoption Rates: Tracking how many team members actively use the software reflects its acceptance. High adoption rates signify user satisfaction.
- Failure Rate of Equipment: Monitoring the frequency of equipment failures allows for assessing the effectiveness of maintenance strategies.
These KPIs provide a roadmap for evaluating software effectiveness and help stakeholders make data-driven decisions.
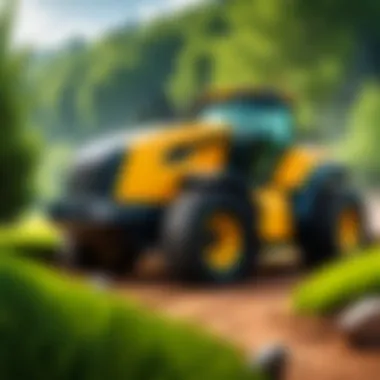
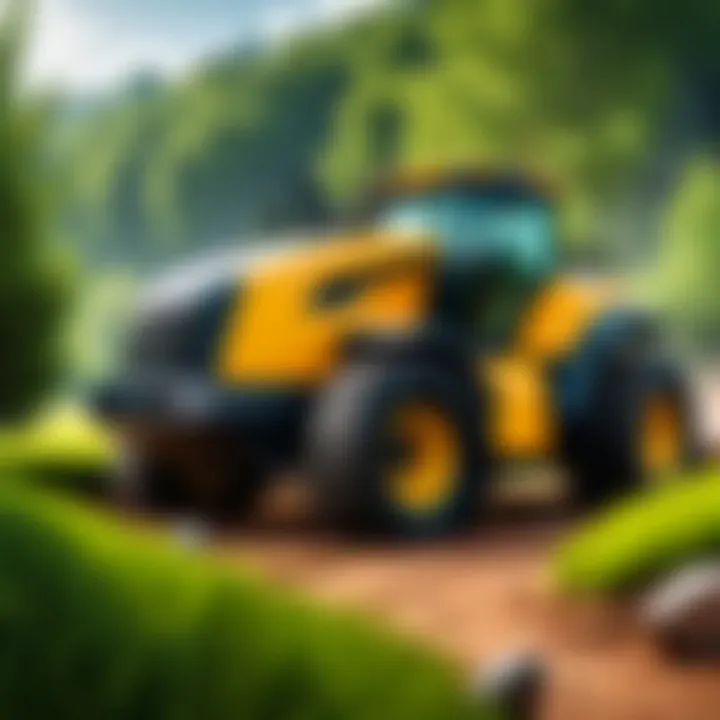
Feedback and Continuous Improvement
Feedback is a vital aspect of measuring success. It fosters continuous improvement in landscape equipment maintenance software. Engaging users and stakeholders for input can reveal areas needing enhancement. Here are a few strategies for collecting feedback:
- User Surveys: Regular surveys help gauge user satisfaction. Utilize tools to create simple questionnaires that focus on user experience and software functionality.
- Interviews: Conducting interviews with key personnel provides qualitative data. Conversations can uncover deeper insights not captured in surveys.
- Performance Reviews: Regularly reviewing KPIs with the team allows for self-assessment. Discussing these metrics can stimulate dialogue about improvement.
- Iterative Updates: Based on feedback, implement software updates that address user concerns. Continuous updates show users their input matters.
Together, effective feedback mechanisms and performance metrics cultivate an environment for success. As organizations adapt their strategies, they can better utilize landscape equipment maintenance software to meet their goals.
Industry Trends in Maintenance Software
Understanding the trends in landscape equipment maintenance software is crucial for industry advisers and decision-makers. These trends inform best practices and aid organizations in adopting effective tools that enhance their operational capabilities. As the industry continues to evolve, maintenance software must adapt to new technologies and changing environmental considerations.
Emerging Technologies
The integration of emerging technologies marks a pivotal shift in the landscape equipment maintenance sector. Key developments include the adoption of artificial intelligence (AI) and Internet of Things (IoT) capabilities. AI enhances predictive maintenance, allowing companies to anticipate equipment failures before they occur. This proactive approach minimizes downtime and extends equipment lifespan.
IoT devices are also becoming prevalent in maintenance software. By connecting equipment to the internet, real-time data can be gathered and analyzed. This connection offers insights into performance metrics, usage patterns, and maintenance needs. As technology progresses, devices may soon reach a point where they can perform self-diagnostics.
Incorporating these technologies can lead to several benefits:
- Improved predictive analysis
- Increased operational efficiency
- Enhanced data-driven decision-making
Sustainability Considerations
As sustainability grows in importance across industries, landscape equipment maintenance software must reflect eco-friendly practices. Users increasingly seek software solutions that facilitate sustainable operations. This includes features such as tracking emissions and energy consumption. By monitoring these factors, companies can make informed choices that align with their environmental goals.
Implementing sustainable practices through maintenance software can also offer economic advantages. Companies that invest in green technologies often see reductions in operating costs. Moreover, clients increasingly prefer to work with businesses that prioritize sustainability, thus enhancing brand reputation.
Key aspects of sustainability in maintenance software may include:
- Reduced carbon footprint through optimized equipment usage
- Resource management to minimize waste
- Compliance with environmental regulations
Integrating sustainable practices with maintenance software is not just a trend; it's a necessity for businesses aiming for long-term success and viability in a competitive landscape.
Case Studies and Success Stories
Case studies and success stories play a crucial role in understanding the practical application and effectiveness of landscape equipment maintenance software. They provide tangible evidence of how these tools can optimize operations, improve efficiency, and prolong equipment lifespan. By analyzing specific examples, industry advisors can offer a more nuanced perspective to clients, helping them make informed decisions tailored to their unique circumstances.
When discussing case studies, it is essential to highlight several elements. First, the selection of a diverse range of scenarios can illustrate how various businesses, regardless of size or type, benefit from maintenance software. This diversity showcases adaptability and highlights the relevance of these tools across the landscape industry. Furthermore, detailed metrics before and after the implementation of maintenance software provide concrete evidence of impact.
Advisors should consider not only the positive outcomes but also the challenges faced during the implementation process. Understanding these obstacles can help businesses better prepare and strategize for successful adoption.
Case Study Overview
Examining a global provider of landscaping services, GreenScape, illustrates the real-world implications of landscape equipment maintenance software. Prior to adopting the solution, GreenScape struggled with fragmented information systems and inefficient resource allocation. Each department operated in silos, which affected communication and resulted in delayed responses to maintenance needs.
The company implemented Fleetio, a widely used maintenance tracking software, that allowed for centralized data management. With Fleetio, GreenScape could track its diverse equipment fleet in real time, enabling quick identification of maintenance requirements.
In a year, the company reported an increase of 30% in equipment uptime and a reduction of 15% in operating costs. This change allowed the company to scale its operations efficiently and increase profit margins without sacrificing quality.
Lessons Learned
From the GreenScape case, several lessons can be drawn.
- Centralization is Key: A centralized platform for managing equipment and maintenance tasks simplifies operations. When all information is available in one place, it reduces errors due to miscommunication.
- Informed Decision-Making: The ability to access real-time data on equipment status enables proactive decision-making. This can significantly reduce the risk of unexpected breakdowns.
- Training and Support: Implementing a new system requires adequate training for all employees. Resistance can stem from a lack of understanding of the new processes, highlighting the need for thorough training programs.
The successful implementation of maintenance software can lead to enhanced operational efficiency and cost savings, reinforcing the necessity for advisors to advocate for its adoption.
In summary, case studies such as that of GreenScape provide valuable insights into the real-world applications of landscape equipment maintenance software. They help to illustrate both the benefits and challenges, enabling industry advisors to offer well-rounded recommendations.
Ending and Recommendations
In the realm of landscape equipment maintenance, utilizing specialized software can significantly reshape management practices. This section aims to distill the essential insights discussed throughout the article. The software's core objective lies in enhancing operational effectiveness and extending equipment longevity. As landscape management continues to evolve, the integration of maintenance software becomes crucial for decision-makers.
The pivotal benefits outlined suggest that decision-makers must consider implementing such solutions to capitalize on their advantages. Improvements in asset tracking and work order management not only streamline operational processes but also provide data-driven decision-making support. Given the increasing complexity and demands of landscape operations, an emphasis on evaluating and selecting the right maintenance software is imperative.
This software offers a way to optimize resource allocation effectively, reducing waste, and enhancing overall productivity.
Summary of Key Points
- Improved Equipment Management: The software addresses gaps in equipment upkeep, allowing for timely servicing and repairs.
- Cost Efficiency: By streamlining maintenance tasks, organizations can cut down on unnecessary expenditures.
- Data Insights: Provides analytics to inform future purchases and maintenance scheduling.
- User Training: Proper education of staff leads to more effective use of the software.
Future Outlook
The future of landscape equipment maintenance software is promising. As technology continues to advance, we can expect several trends to shape its development.
- Integration with IoT: More equipment will be equipped with sensors, connecting to maintenance software for real-time monitoring of performance.
- Artificial Intelligence: The incorporation of AI will enable predictive maintenance strategies, allowing managers to identify potential issues before they occur.
- Customization: As businesses grow, software will adapt to specific needs, enhancing functionality based on user feedback.
In summary, the landscape maintenance software is not just a tool; it is an essential element of modern landscaping businesses. Focusing on these future enhancements will surely create avenues for greater efficiency and adaptability in the industry. Employing these solutions will likely position firms ahead in a competitive marketplace.