Mastering Inventory Storage Management for Efficiency
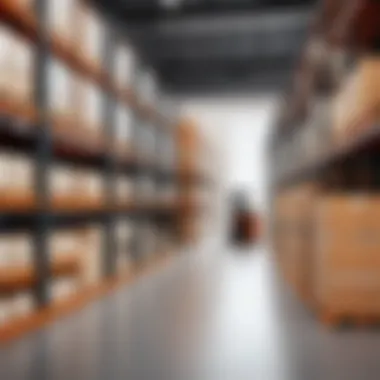
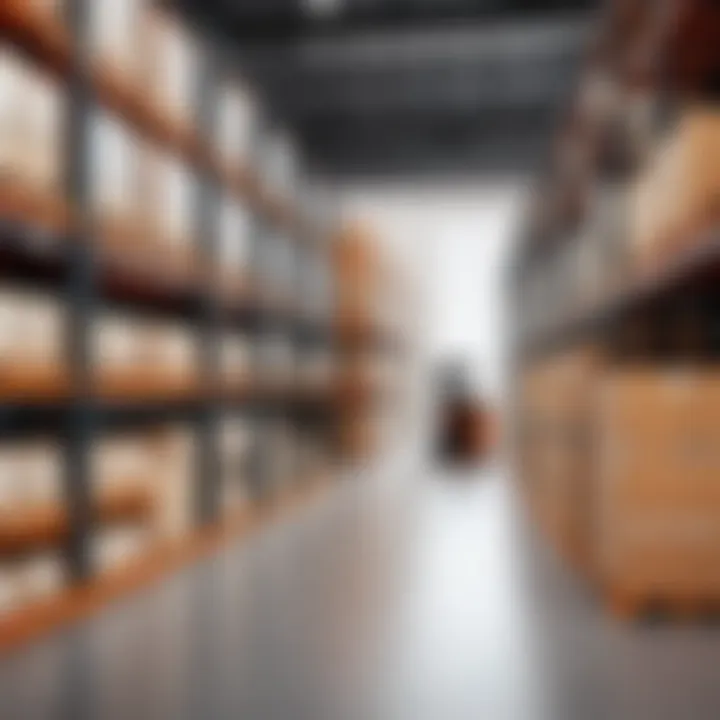
Intro
Inventory storage management is not just a matter of tossing boxes into a warehouse and hoping for the best. It's a nuanced practice, one that plays a pivotal role in streamlining operations and optimizing resources. The significance of how inventory gets managed can easily make or break a business’s success. With the rise of e-commerce and the increasing complexity of supply chains, understanding inventory storage has never been more crucial.
In this article, we will unpack the layers of inventory storage management, focusing on the systems and technologies that keep inventory organized and flowing smoothly. Readers will gain insight into techniques that can enhance operational efficiency, helping decision-makers make informed choices about software solutions tailored to specific business contexts.
From tracking accuracy to the implementation of storage systems, we will walk you through strategies that optimize inventory processes, ensuring scalability in today’s fast-paced marketplace. For entrepreneurs and IT professionals alike, this guide is a treasure trove aiming to equip readers with the knowledge needed to elevate their inventory management practices.
To start this insightful journey, we’ll delve into the essential software that lays the foundation for successful inventory storage management.
Understanding Inventory Storage Management
Inventory storage management is more than just a fancy term thrown around in logistics meetings. It’s the backbone of efficient supply chains and the lifeblood of any business that deals with physical products. Understanding this topic means grasping the nuances of storage, organization, and movement of goods within warehouses and distribution centers. The efficiency of inventory storage directly impacts operational costs, customer satisfaction, and overall business effectiveness.
Definitions and Key Concepts
At its core, inventory storage management refers to the methods and procedures used to store, track, and move products within a warehouse. Its primary aim is to ensure that inventory levels match demand while minimizing storage costs.
Some key concepts include:
- Lead Time: The time that passes between the initiation of an order and its fulfillment. Reducing this time can significantly enhance service levels.
- Inventory Turnover Ratio: This metric helps businesses understand how often inventory is sold and replaced over a period. A high turnover suggests efficient management and sales, while a low turnover may indicate overstock or poor sales.
- Safety Stock: This is the extra inventory kept to prevent stockouts, ensuring that operations can continue in the event of unexpected demand surges or supply chain hiccups.
These definitions lay the groundwork for understanding the intricacies of storage management, especially when viewed through the lens of operational efficiency and cost control.
Importance in Supply Chain Dynamics
In the grand scheme of supply chain dynamics, inventory storage management is crucial. It helps bridge the gap between suppliers and customers, making sure the right products are available at the right time. Poor inventory storage practices can lead to various complications, such as:
- Increased Costs: Carpeting the floor with unsold products leads to wasted resources. Conversely, a lack of stock can incur rush shipping costs or lost sales.
- Customer Dissatisfaction: Customers today expect quick and reliable service. Anything less can tarnish a brand's reputation.
- Operational Inefficiencies: Disorganized storage can result in unnecessary delays as workers spend extra time locating products.
“Effective inventory management is not just about keeping stock, it's about ensuring that your business flows smoothly.”
Invariably, optimizing inventory storage allows companies to adapt quickly to changing market conditions, effectively respond to customer demands, and cultivate a competitive edge in the market. It's not merely a function; it's a strategic imperative.
Inventory Management Principles
Inventory management principles serve as the backbone for establishing a functional and efficient inventory system. It’s not just about having stock on hand; it’s about understanding how to manage that inventory strategically to enhance overall operational performance. Navigating the complexities of inventory management requires a firm grasp of key concepts that dictate inflexion points in the flow of goods, influence cost structures, and drive profitability. Effective inventory management can mean the difference between a thriving business and one that struggles to stay afloat in today's fast-paced market environment.
The Economic Order Quantity Model
The Economic Order Quantity (EOQ) model presents a vital methodology for managing inventory costs related to ordering and holding stock. It’s a formula designed to minimize the total costs associated with ordering inventory, including holding costs and order costs. The EOQ model provides insight into how much of a product should be ordered at a time to maintain the desired inventory level without tying up excessive capital.
By applying this model, businesses can avoid pitfalls such as overstocking, which leads to unnecessary holding costs, or understocking, which can result in missed sales opportunities. The formula considers factors such as demand rate, ordering costs, and holding costs. What this translates to is a more streamlined approach where businesses can anticipate their inventory needs without the headaches of frequent restocking or surplus.
"Using the EOQ model is like having a GPS for your inventory—it shows you the most efficient route for managing stock levels."
Just-In-Time (JIT) Inventory
Just-In-Time (JIT) inventory management is a strategy that aligns raw-material orders from suppliers directly with production schedules. Think of it as a finely tuned orchestra, where each element plays in harmony without any unnecessary sound interruptions caused by overstock or wastage. The objective of JIT is to reduce waste and increase efficiency by keeping inventory levels as low as possible.
Successfully implementing a JIT inventory system requires strong supplier relationships and precise demand forecasting. It is crucial to have dependable suppliers who can deliver materials on short notice. In this way, JIT not only helps with inventory costs but also improves responsiveness to market demands. However, companies must tread carefully, because any disruption in the supply chain can lead to delays in production.
ABC Analysis
ABC Analysis is an inventory categorization technique which helps organizations prioritize their inventory management efforts. The basic premise is simple: categorize products based on their importance to the business, often assessed by their consumption value. The categorization generally falls into three distinct classes:
- A items: High-value items that require strict inventory control. These are the essentials and usually account for a small percentage of inventory but a large share of the overall purchase value.
- B items: Moderate-value items that need less strict management than A items but still deserve attention.
- C items: Low-value items that can be ordered in large quantities without much oversight.
The ABC Analysis allows businesses to allocate resources effectively, ensuring that their time and capital focuses on managing high-priority products. This nuanced approach supports more resilient inventory practices, reduces the risks of overstocking less crucial items, and helps streamline logistics.
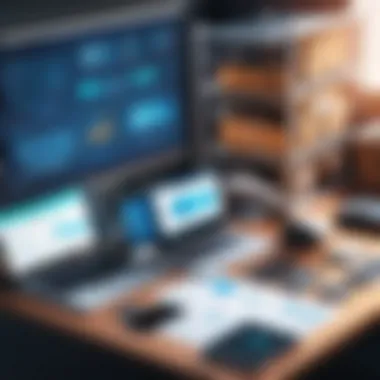
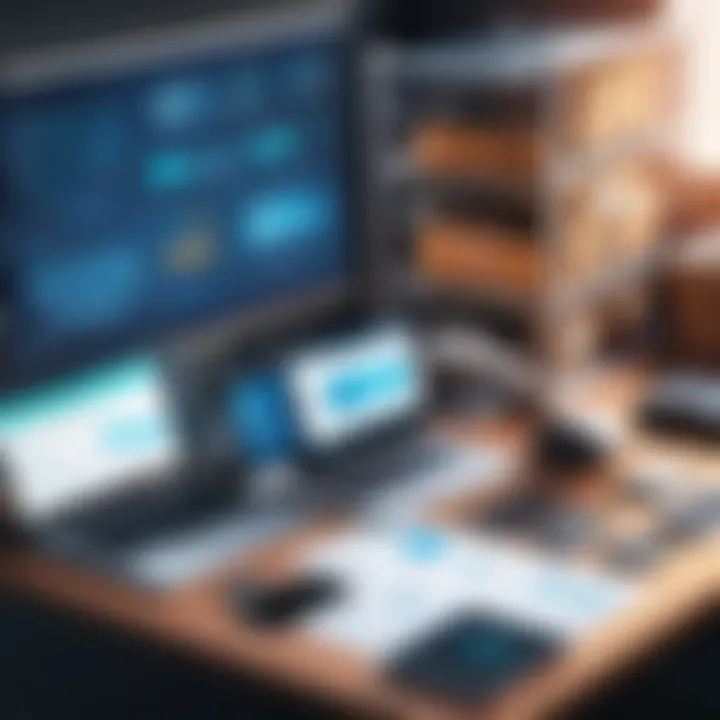
In summary, mastering these principles can greatly enhance the understanding and management of inventory storage systems. They don’t just facilitate better decisions; they also empower organizations to adapt to changing market conditions and optimize their operations effectively.
Types of Inventory Storage Systems
Understanding the various types of inventory storage systems is key to enhancing operational efficiency and maximizing space utilization. Each system has its unique advantages, disadvantages, and considerations that can significantly impact an organization's inventory management processes. Effectively matching the right storage system with the specific needs of the business can lead to better organization, reduced costs, and improved workflow while ensuring optimal stock levels.
Static vs. Dynamic Storage
Static storage refers to fixed shelving or racking systems where inventory is stored in designated locations. This method is straightforward and works well for straightforward inventory types, such as small items in a retail store or spare parts in a workshop. While easy to manage, it often lacks flexibility, resulting in inefficiencies especially when product demand fluctuates.
On the flip side, dynamic storage involves systems that allow goods to move and be stored in various locations. For instance, FIFO (First In, First Out) systems can be beneficial in industries dealing with perishable goods. This type can lead to better space utilization and faster retrieval times, which is crucial in environments where speed and efficiency are paramount. Moreover, the task of reorganizing static storage systems can be cumbersome and costly compared to dynamic ones that provide the agility to adapt to changing inventory needs.
Automated vs. Manual Systems
In today's fast-paced business world, automated storage solutions are becoming increasingly popular. They rely on technology such as conveyor systems, automated guided vehicles (AGVs), or robotics for storage and retrieval tasks. For example, Amazon utilizes extensive automation in its warehouses to manage vast inventory levels efficiently. Automated systems can greatly reduce labor costs and minimize human error.
However, manual systems still hold their ground, especially for smaller businesses that might find automation economically unfeasible. Manual inventory storage entails human oversight, which offers a level of flexibility and personalization that automated systems may lack. For businesses navigating tight budgets, developing an effective manual inventory storage system can be just as effective, albeit more labor-intensive. Understanding the nuances between these two approaches can inform decision-making around technology investments.
Selective and Pallet Racking Systems
When it comes to racking systems, selective racking is one of the most common types used. It allows for easy access to individual pallets, making it an excellent choice for warehouses with diverse products and varying turnover rates. It's important to note, however, that selective racking can consume more space as it requires aisles wide enough for forklift operations.
Alternatively, pallet racking systems optimize storage space by allowing vertical stacking. This design is particularly advantageous for businesses with high volumes of a smaller variety of products. It maximizes floor space usage while ensuring that items are still accessible. For businesses looking to store large quantities of products while keeping operational costs down, pallet racking systems can be vital.
The right choice of storage system does not just help store items; it paves the way for smoother operations and ultimately contributes to a more efficient supply chain.
By thoroughly assessing inventory needs and understanding the particulars of each storage system type, businesses can significantly refine their inventory handling processes.
Technology in Inventory Storage Management
In the contemporary landscape of inventory storage, the role of technology cannot be overstated. It transforms how businesses manage, track, and optimize their inventory processes. The integration of various technological solutions into inventory management facilitates enhanced operational efficiency, cost reduction, and a significant increase in accuracy. Staying ahead of the competition demands that organizations leverage these tools, ensuring agility in an ever-changing market.
Role of Warehouse Management Systems (WMS)
Warehouse Management Systems are at the heart of modern inventory management. These software applications streamline warehouse operations and enable real-time visibility into inventory levels. By automating various tasks such as sorting, picking, and packing, WMS significantly reduces human error and improves workflow efficiency. Businesses observe a notable decrease in processing times, leading to faster order fulfillment.
Some specific advantages of utilizing WMS include:
- Improved Inventory Accuracy: Automated tracking systems reduce discrepancies and ensure that stock levels reflect the actual availability.
- Enhanced Data Reporting: Advanced analytical capabilities provide businesses with insights that are not only prudent for operational decisions but also for strategic planning.
- Scalability: As businesses grow, WMS can adapt to increasing volumes without a hitch, thus supporting expansion with ease.
Barcode and RFID Technology Integration
Barcode scanning and RFID technology are pivotal in modern inventory management. These technologies combat errors often present in manual tracking methods. Simply put, the efficiency gained through these technologies is invaluable.
Barcodes offer a low-cost solution for tracking products and shipments. When scanned, they provide instantaneous information on an item's location and status. On the other hand, RFID tags offer superior capabilities, such as scanning multiple items simultaneously without direct line-of-sight. This technology allows for:
- Faster Inventory Counts: Organizations can complete stock audits in a fraction of the time it would take using traditional methods.
- Increased Control over Stock: The real-time data relayed back to the WMS helps with reorders and identifying slow-moving items, avoiding costly stockouts.
Cloud-Based Solutions
Cloud-based inventory management solutions have ushered in a new era of flexibility and accessibility. Unlike traditional software that requires substantial up-front investment, cloud systems operate on a subscription basis, making it easier for businesses, especially smaller ones, to manage their inventories without the burden of substantial initial costs.
Some key features that organizations can benefit from include:
- Remote Accessibility: Staff can access inventory data from virtually anywhere, fostering remote operations and enhancing collaboration.
- Automatic Updates: Cloud providers handle updates and maintenance, ensuring companies always work with the latest features and security measures.
- Data Security: Cloud platforms typically offer robust security protocols, protecting sensitive inventory data from potential threats.
Cloud-based solutions are not just a trend; they’re reshaping the very framework of inventory management.
Challenges in Inventory Storage Management
Navigating the waters of inventory storage management is no walk in the park. Businesses often grapple with practical hurdles that can throw a wrench into their operations. Understanding these challenges is crucial because addressing them head-on leads to improved efficiency, reduced costs, and ultimately, a healthier bottom line. In this section, we’ll dissect some of the prevalent challenges—overstocking and stockouts, inventory accuracy and errors, as well as space optimization issues—each having its own strings attached.
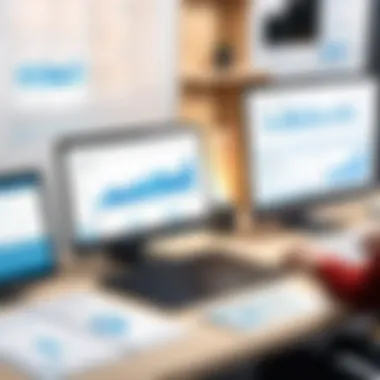
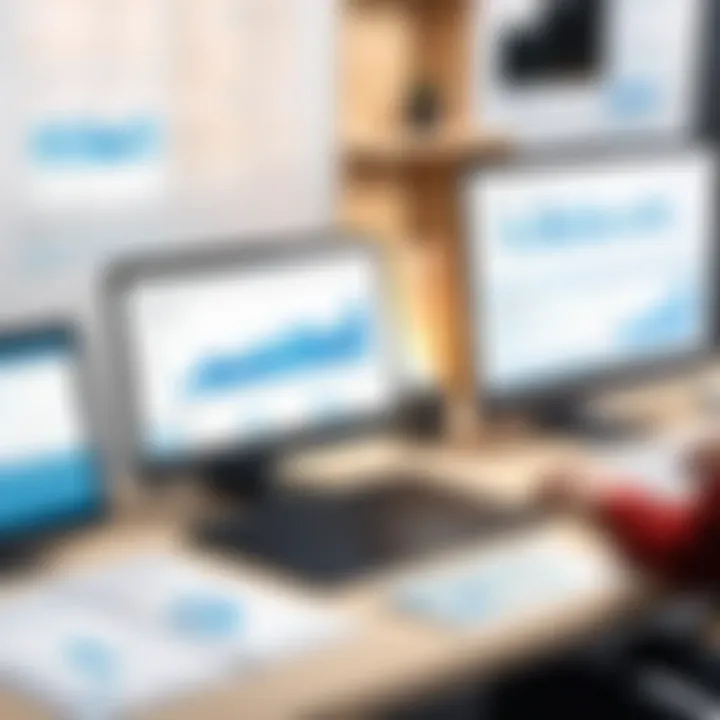
Overstock and Stockouts
Overstock and stockouts dance a fine line in the inventory world, often reflecting a business's fluctuating rhythm. When excess stock builds up, funds are tied up, which can be likened to putting your money in a piggy bank—cute at first glance but not doing any favors to growth opportunities.
On the flip side, stockouts mean missed sales and disgruntled customers, akin to being out of stock during a Black Friday sale—nobody wants that. Many firms find themselves caught in this cycle due to inadequate forecasting or misinterpreted market demand. To combat this, businesses need robust systems in place that employ predictive analytics to better gauge upcoming needs.
- Impacts of Overstocking:
- Consequences of Stockouts:
- Increased holding costs
- Risk of spoilage or obsolescence
- Reduced cash flow
- Lost sales opportunities
- Customer dissatisfaction
- Damage to brand reputation
Inventory Accuracy and Errors
Bumping into errors in inventory records is much like going down a rocky road; it can cause significant headaches. Inventory accuracy not only affects daily operations but also spills over into financial reporting and strategic decisions.
Even minor inaccuracies can snowball, leading to larger issues that create a domino effect throughout the supply chain. Businesses often underestimate the importance of meticulous tracking and reconciling inventory data. Regular audits become essential. They ensure that what's on the shelves matches what the records say.
- Common Causes of Inaccuracy:
- Impact of Errors:
- Manual data entry errors
- Poor technology integration
- Lack of staff training
- Financial discrepancies
- Ineffective restocking processes
- Loss of customer trust
Space Optimization Issues
Space is money in the world of inventory storage management. An optimized space isn’t just about cramming items onto shelves, but about arranging items in a way that enhances accessibility and efficiency. Failure to utilize space properly can lead to unnecessary costs and operational inefficiencies.
Many warehouses are like jigsaw puzzles, with every piece needing to fit just right. With the rise of e-commerce logistics, the demand for efficient storage solutions has never been higher. Companies must rethink their layout to ensure they aren't wasting valuable square footage.
- Key Principles of Space Optimization:
- Analyze product turnover rates
- Implement vertical storage solutions
- Regularly review and adjust layouts
> “A well-organized storage system can drastically reduce picking time and costs, translating directly to improved customer satisfaction.”
In summary, addressing these challenges with actionable strategies can pave the way for smoother operations and ultimately lead to a more successful inventory storage management process.
Best Practices for Effective Inventory Storage
Effective inventory storage is a cornerstone of operational excellence. Implementing best practices in this domain not only enhances the efficiency of warehouse operations but also ensures that businesses meet customer demands while minimizing costs. This section delves into various strategies involving routine audits, harnessing data analytics, and cultivating a knowledgeable workforce. Each of these elements plays a vital role in forming a coherent inventory management strategy that is not only effective but also sustainable in the long run.
Regular Inventory Audits
Regular inventory audits serve as the backbone of inventory management. They help in maintaining accuracy in stock levels, identifying discrepancies, and ensuring what is recorded aligns with what is physically available. Ideally, audits should be conducted periodically—monthly or quarterly—to spot problems before they snowball. Simply counting stock once a year is not enough; regular checks help avoid overstocking or stockouts, both of which can have dire consequences on a business’s bottom line.
Having a systematic approach toward audits can also bring several benefits:
- Reduced Inventory Shrinkage: Regular checks can significantly cut down on losses due to theft or mismanagement.
- Improved Supplier Relationships: Accurate inventory records help in timely reordering, leaving less room for conflict regarding delivery expectations.
- Enhanced Customer Satisfaction: Knowing what products are available at any given moment means businesses can fulfill orders efficiently, leading to happier customers.
Incorporating various audit methods, such as cycle counting or comprehensive physical counts, can ensure a robust inventory management system.
Leveraging Data Analytics
Data analytics is an underutilized gem in inventory storage management. By analyzing trends, patterns, and demands, organizations can make informed decisions that align closely with market needs. One key aspect is predictive analytics, which helps in forecasting demand based on historical data. Using such insights can lead to:
- Optimized Stock Levels: By aligning your inventory with predicted demand, overstock situations can be significantly reduced.
- Informed Purchasing Decisions: Understanding seasonal patterns allows for better planning regarding procurements, preventing blind purchases.
- Identification of Slow-moving Items: Analytics can reveal which products are not selling, encouraging timely markdowns or strategic promotions to clear out unsold inventory.
In this digital age, integrating business intelligence tools can offer further advantages. These platforms provide real-time updates on inventory levels, enabling a clearer picture of stock trends.
Training and Development of Staff
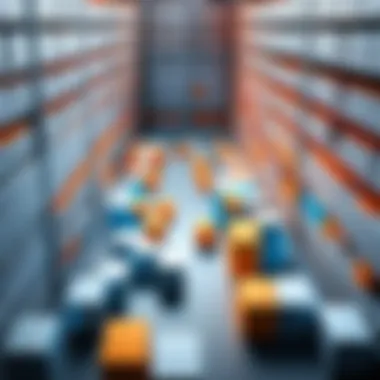
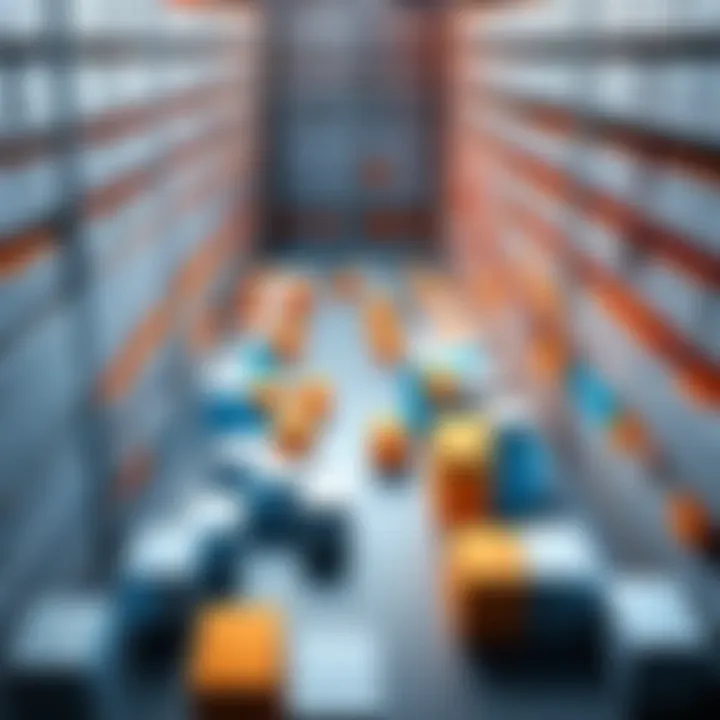
Human resources are often overlooked in the inventory storage framework. Well-trained staff can make all the difference in achieving operational efficiency. Providing continual training ensures that employees are aware of best practices in managing inventory.
A proactive training program might include:
- Workshops on New Technologies: Training on the latest warehouse management systems or inventory tracking tools ensures that staff are proficient and that these systems are used to their full potential.
- Safety Procedures: Proper training in handling stock safely reduces accidents, thus maintaining a healthy work environment.
- Soft Skills Development: Encouraging communication and problem-solving skills can help staff collaborate better, facilitating smoother operations.
Ultimately, investing in employees doesn't just enhance productivity; it fosters a more engaged workforce, which is key to achieving long-term goals and maintaining a competitive edge in the market.
Future Trends in Inventory Storage Management
In the ever-evolving landscape of inventory storage management, understanding future trends is not just advantageous but essential. Businesses that stay ahead of the curve can leverage innovative systems and practices to enhance efficiency, reduce costs, and satisfy their customers. This section explores the implications of sustainability, artificial intelligence, and the booming e-commerce sector, offering valuable insights into how these trends can shape the future of inventory storage.
Sustainability Practices
Sustainability is more than just a buzzword; it’s a necessity in today’s business environment. As companies grapple with the impact of their operations on the environment, adopting sustainable inventory practices is gaining traction. Here are some key considerations:
- Energy Efficient Storage Solutions: Utilization of energy-efficient lighting and climate control systems can significantly reduce a warehouse's carbon footprint. Switching to LED lights not only cuts costs but also creates a better work environment.
- Sustainable Materials: Storing products using renewable packaging and adopting practices like reusing pallets contribute positively to sustainability goals. This reduces waste and environmental impact, aligning with customer preferences for eco-friendly practices.
- Waste Reduction Programs: Regular assessment and analysis of stock can lead to better management of perishable goods, helping cut down on waste. A strategy emphasizing waste management can even unfold new avenues for profit through recycling and repurposing materials.
By integrating these practices, businesses not only contribute to a healthier planet but also enhance their reputations among environmentally conscious consumers.
Integration of Artificial Intelligence
The integration of artificial intelligence within inventory storage management represents a pivotal shift. This technology empowers organizations to operate with enhanced precision and agility. Here’s how AI is transforming the landscape:
- Predictive Analytics: AI tools can analyze vast amounts of data to forecast inventory needs more accurately. This predictive capability helps in minimizing overstock and stockouts, leading to optimal inventory levels.
- Automation of Routine Tasks: Tasks like order processing, stock tracking, and replenishment can be automated. This not only speeds up operations but allows human resources to focus on more strategic activities.
- Enhanced Decision-Making: AI can provide insights into customer behavior and market trends, informing better purchasing and inventory decisions. With AI, businesses can react swiftly to changes in demand, ensuring that they are always one step ahead.
Investing in AI technologies can yield substantial long-term benefits, contributing to greater operational efficiency and competitiveness.
Expansion of E-commerce Logistics
With the rise of online shopping, the expansion of e-commerce logistics is a trend that can no longer be ignored. The demand for quick and reliable delivery has created pressure on inventory storage systems to adapt:
- Flexible Storage Solutions: Companies are increasingly adopting flexible storage solutions to accommodate varying stock levels dictated by e-commerce trends. This responsiveness allows them to keep costs in check while meeting customer expectations.
- Real-Time Inventory Management: Leveraging advanced software solutions helps businesses manage inventory in real time, minimizing errors and ensuring timely deliveries. Knowing what’s in stock and where it is located makes a monumental difference in operational efficiency.
- Last-Mile Delivery Innovations: Solutions aimed at making last-mile delivery more efficient, such as automated warehouses and micro-fulfillment centers, are on the rise. These innovations not only cut delivery times but also enhance overall customer satisfaction.
Adapting to the needs of the e-commerce revolution requires agility in inventory storage practices, ultimately establishing a robust framework for future growth.
"The integration of sustainability and technology is not just a trend; it's a necessity for thriving in a competitive market."
In summary, staying aware of these future trends in inventory storage management allows businesses to proactively adapt their strategies, ensuring sustainable growth and efficiency in a fast-paced environment.
Ending
In the realm of inventory storage management, the conclusion serves as a pivotal element. It wraps up the discussion and highlights the key learning points. The critical nature of effective inventory management cannot be overstated. Every decision connected to inventory processes influences operational performance, cost control, and ultimately, your bottom line.
Inventory storage isn't just about housing goods; it's about ensuring those goods move seamlessly through the supply chain. As we have seen, various systems and technologies play a significant role in achieving this goal. Adopting practices that enhance accuracy, minimize errors, and streamline operations stands paramount.
A few specific elements have come to light that deserve emphasis:
- Comprehensive Understanding: Mastering the different types of storage systems, including static and dynamic, expands options to tailor solutions to specific business needs.
- Technological Adoption: Warehousing management systems and cutting-edge technologies like RFID represent greater efficiency, accuracy, and scalability.
- Proactive Management: Regular audits and leveraging data analytics are essential to ensure optimal performance and mitigate risks associated with overstocking or stockouts.
The insights shared throughout this article are integral for decision-makers, IT professionals, and entrepreneurs aiming to sculpt an efficient inventory management strategy. It’s clear that a prudent approach to inventory storage positively impacts broader business objectives, solidifying its relevance in today’s supply chain landscape.
Recap of Key Insights
Understanding the labyrinth of inventory storage management yields several crucial takeaways:
- Relationship with Supply Chain: Efficiency in inventory management forms the backbone of an effective supply chain, directly affecting customer satisfaction and financial outcomes.
- Investing in Technology: Innovative tools and systems lay the groundwork for future scalability and flexibility.
- Sustainability and Ethical Practices: Emphasizing green initiatives in inventory storage can lead not only to environmental benefits but also enhance brand loyalty among increasingly eco-conscious consumers.
These points stitch together a comprehensive understanding that can guide stakeholders in making informed decisions.
Recommendations for Software Solutions
When considering software for inventory storage management, a tailored approach is advisable. Here are some suggestions:
- Warehouse Management Systems (WMS): Prioritize solutions that integrate seamlessly with existing systems, providing real-time data and operational visibility.
- Flexible Cloud Solutions: Look for cloud platforms that allow scalability according to demand fluctuations, especially vital in e-commerce.
- Integration Capabilities: Ensure planned solutions can incorporate existing technologies, including RFID and barcode systems, for a unified approach to inventory tracking.
As you evaluate these software options, remember that choosing the right tools isn’t just about functionality. It’s about aligning them with your broader business strategy and adapting to future challenges.