Insights into Discrete Manufacturing Practices
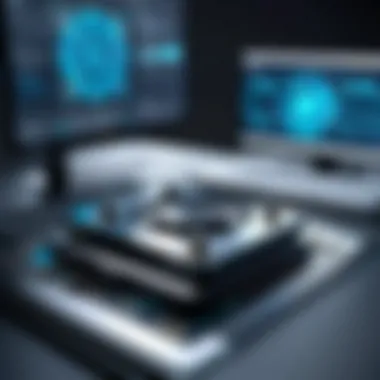
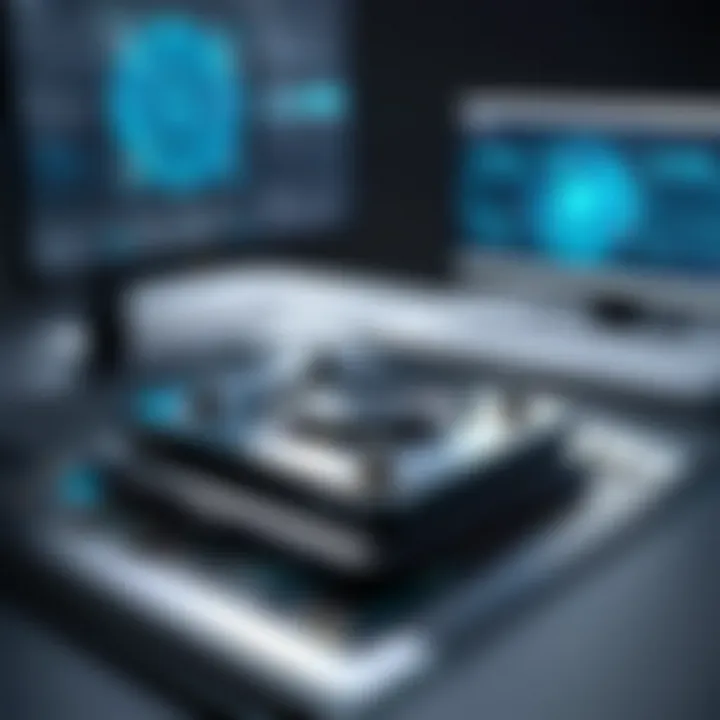
Intro
Discrete manufacturing fuels a significant portion of the global economy, producing everything from mundane items to sophisticated machinery. As the sector evolves, understanding the underlying principles and methodologies becomes vital for those who navigate its complexities. This article will flesh out the essential nuances of discrete manufacturing, focusing on its practical applications and technological advancements.
The discussion encompasses methodologies relevant to different manufacturing contexts, while also diving into how the advent of Industry 4.0 reshapes production landscapes. Technology is not merely a backdrop here; it's a key player that influences how entities operate—from the smallest workshops to massive production facilities.
In light of this, decision-makers, IT professionals, and entrepreneurs should be well-equipped with insights that empower informed choices. The impact of varied strategies, the challenges manufacturers face, and the transformations brought about by innovations will weave together a narrative that highlights the critical nature of discretion in manufacturing.
Through this explorative journey, readers will garner a firm grasp on optimizing production workflows and the strategic applications that drive efficiencies in discrete manufacturing.
Understanding Discrete Manufacturing
Discrete manufacturing stands out as a crucial component in the world of production, where unique items are produced individually, as opposed to bulk materials. By exploring this subject, one not only grasps the fundamental principles behind manufacturing's mechanics but also uncovers the profound implications that such methods have across various sectors.
The term "discrete" signifies distinct, individual units, making it essential for industries like automotive, machinery, and consumer electronics. Understanding this concept paves the way for better decision-making, as it highlights key characteristics that differentiate it from other manufacturing forms. Decisions made in this field often involve complex interactions among various factors, including design, assembly, and resource allocation, all of which are pivotal for ensuring efficiency and quality.
Delving into discrete manufacturing equips decision-makers and IT professionals alike with the insights needed for streamlining operations and making informed investments in technology.
Definition and Characteristics
At its core, discrete manufacturing involves the creation of specific items that can be counted, touched, and tracked through their production lifecycle. Each unit is distinct and often carries unique attributes, like serial numbers, which can aid in identifying them individually. Examples of products in this category include automobiles, machinery components, and consumer appliances.
Some defining characteristics of discrete manufacturing include:
- Batch Production: Items are produced in batches, allowing for flexibility in product specifications.
- Customization: Often, products can be tailored to customer needs, making the manufacturing process dynamic.
- Complex Assembly: The process frequently involves multiple components that are assembled to create the final product.
- Inventory Management: Due to the varied nature of items produced, effective inventory management is critical to mitigate excess stock or shortages.
To fully understand discrete manufacturing, one must appreciate the integration of various operational processes, including planning, scheduling, and quality control, which are essential to optimizing production.
Difference from Process Manufacturing
Discrete manufacturing should not be confused with process manufacturing, which is characterized by producing goods through a continuous flow of materials. In process manufacturing, items typically undergo chemical or physical changes in a sequential manner, resulting in products that cannot be distinctly identified after production. This is common in industries such as food and beverage, chemicals, and pharmaceuticals.
Key differences include:
- Nature of Products: In discrete manufacturing, products remain identifiable; in process manufacturing, they become part of a mixture.
- Production Flexibility: Discrete manufacturing offers a higher degree of customization compared to the standardization often found in process manufacturing.
- Production Techniques: Discrete manufacturing can utilize various assembly techniques, while process manufacturing relies heavily on continuous processes.
Understanding these differences is critical, as they inform how businesses strategize their manufacturing approaches, impacting everything from operational efficiencies to customer satisfaction.
By getting a grip on what discrete manufacturing entails and how it varies from other types of manufacturing, industry leaders can navigate challenges and seize opportunities more effectively. This knowledge serves as a springboard for exploring the nuances of the field further.
Key Components of Discrete Manufacturing
Understanding the key components of discrete manufacturing is crucial for grasping its operational efficiency and effectiveness. This sector doesn’t just create product - it thrives on principles that ensure every stage of production aligns with strategic goals. Companies are increasingly recognizing that by focusing on the vital elements, they can drive performance, reduce costs, and enhance quality. In the following sections, we’ll delve into two primary components: Product Lifecycle Management and Supply Chain Management.
Product Lifecycle Management
Product Lifecycle Management (PLM) is an integral part of discrete manufacturing. It encompasses the entire journey of a product, from its conception to its retirement. PLM isn’t merely a set of processes; it’s a mindset that enfolds every team member involved with product development.
- Collaboration: Effective PLM fosters collaboration among different departments like engineering, marketing, and sales. It ensures every voice is heard and contributes to better product outcomes.
- Data Management: Managing vast amounts of data is vital. PLM systems streamline the organization of design data, specifications, and compliance information, making it accessible yet secure.
- Efficiency: By refining processes, PLM helps shorten the time between product ideas and market launch. If you can reduce time-to-market, you’ll have a leg up on the competition.
Moreover, PLM allows for better risk management. Companies can simulate potential issues and plan for unpredictable problems before they arise. That preparation can save tons of resources and prevent frustration down the line. Simply put, adopting a PLM approach is no longer optional; it’s a necessity in today’s fast-paced market.
"A well-implemented PLM strategy can be the difference between leading the pack and trailing behind."
Supply Chain Management
Supply Chain Management (SCM) is another cornerstone of discrete manufacturing. At its core, SCM orchestrates the flow of goods, data, and finances as products move from suppliers to manufacturers to retailers and finally to customers. This is often where manufacturers see significant gains or losses in efficiency.
- Integration: Modern SCM involves integrating suppliers and distributors into a cohesive network. This facilitates real-time data sharing, ultimately leading to better decision-making.
- Inventory Management: Managing inventory is essential. Too much stock means waste, while too little can lead to missed opportunities. Advanced SCM systems provide analytics to maintain just the right amount.
- Agility: In an era where market demands can change overnight, having an agile supply chain helps businesses adapt swiftly. The ability to pivot quickly can establish a company as a market leader.
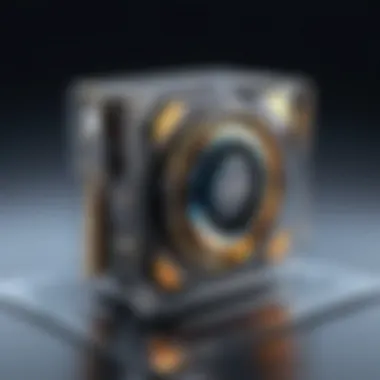
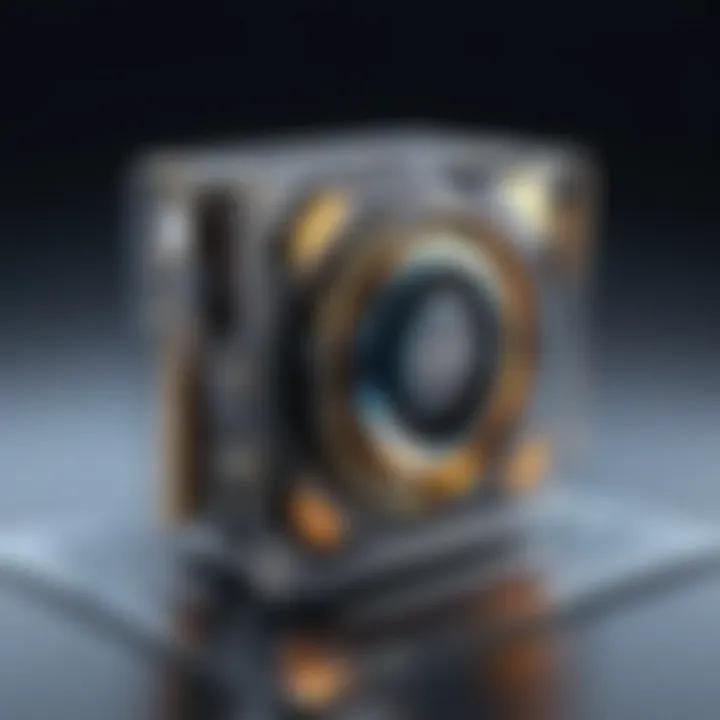
In summary, succeeding in discrete manufacturing hinges on how well companies implement PLM and SCM. These components are not isolated; they work in tandem, influencing various aspects of business operations. The right focus on both not just enhances productivity but also paves the way for sustainable growth.
Technological Advancements in Discrete Manufacturing
The field of discrete manufacturing is undergoing a transformation thanks to a slew of technological advancements that are reshaping how products are designed, produced, and delivered. When we talk about these advancements, we are not merely referring to shiny new machines or software. Instead, we are diving into elements that make processes more precise, efficient, and adaptive. The significance of these technology shifts lies in various aspects, from streamlining operations to enhancing product quality, and even enabling better sustainability practices. All of these factors contribute to a competitive edge in a crowded marketplace.
Automation and Robotics
Automation is perhaps one of the most prominent technological developments making waves in discrete manufacturing. The incorporation of robotics in production lines is a game-changer. Robots, equipped with AI and machine learning, can work alongside human operators to carry out repetitive tasks more efficiently than before. It’s like having a well-oiled machine that never tires. These intelligent machines can also perform quality checks, greatly reducing the margin for error. This means that defects can be detected and addressed almost in real time, enhancing the overall quality of the output.
Furthermore, with the latest advancements in collaborative robots, or cobots, human workers and machines can interact seamlessly. It’s not just about efficiency; it’s about creating a safer working environment where robots handle the heavy lifting or dangerous tasks, allowing humans to focus on areas requiring creativity and critical thinking.
Additive Manufacturing
Additive manufacturing, often referred to as 3D printing, is another disruptive technology that deserves attention. Unlike traditional subtractive methods where material is cut away, additive manufacturing builds products layer by layer, which can significantly reduce waste. Imagine creating a complex part that would be impossible or too costly to produce using conventional methods. This opens the doors to customization, allowing manufacturers to cater to specific customer needs without compromising on quality or speed.
In sectors like aerospace and medical devices, additive manufacturing enables rapid prototyping and allows for on-demand production of spare parts. This kind of flexibility can drastically cut lead times and associated costs. It encourages innovation, giving engineers the chalkboard space to sketch bold ideas without the immediate restraints of manufacturing limitations.
Internet of Things
The Internet of Things (IoT) is perhaps one of the most exciting realms within discrete manufacturing. Imagine a factory where each piece of equipment communicates with one another, sharing information and optimally coordinating tasks. Smart sensors can monitor machinery health and predict failures before they occur, minimizing downtime. It’s akin to having health check-ups for your machines, ensuring they perform at their best.
Data plays a central role in this landscape. By harnessing data analytics, manufacturers can gain insights into production performance, enabling real-time decision-making. Understanding trends and patterns can lead to smarter inventory management and can further refine supply chain processes. The result is an agile, responsive manufacturing environment that can pivot when market demands shift.
"Incorporating new technologies isn’t just about keeping up with the times; it’s about staying ahead."
Embracing these technological advancements will not only boost operational efficiency but also lay the groundwork for sustainable practices that respond to the growing concerns about the environmental impact of manufacturing. As manufacturers navigate this complex landscape, leveraging technology will help them forge a pathway into the future.
The Role of Software in Streamlining Processes
The integration of software solutions in discrete manufacturing has become indispensable, driving the efficiency and precision that today's industries demand. As manufacturers grapple with increasing complexities and dynamic supply chains, leveraging software tools is not just a luxury; it’s a necessity. The right software can simplify operations, enhance communication, and ultimately keep the production line humming.
Enterprise Resource Planning Systems
Enterprise Resource Planning (ERP) systems serve as the backbone of most manufacturing operations. By centralizing data from different departments—such as finance, HR, and inventory—ERPs provide a holistic view of the ongoing processes. This integration enables decision-makers to assess the performance of various components quickly, leading to optimized workflows.
Key benefits of implementing ERP systems include:
- Real-time insights: Instant access to inventory levels, production schedules, and financial data helps in making timely decisions.
- Streamlined processes: Automation of routine tasks like order processing reduces manual errors and saves time.
- Cost savings: Improved efficiency often translates into lower operational costs, enabling firms to allocate resources more effectively.
- Scalability: As organizations grow, scalable ERP systems can adapt to handle increased data and more complex operations without a hitch.
Considerations for choosing an ERP can be daunting. Each organization must weigh factors such as compatibility with existing systems, user-friendliness, and the ability to customize based on specific business needs.
Manufacturing Execution Systems
Manufacturing Execution Systems (MES) go one step further by connecting the production floor with the ERP layers. They monitor and control manufacturing operations in real time, providing insights that help optimize production efficiency. MES is particularly crucial in environments where quality and speed are paramount.
Some notable advantages of MES include:
- Work-in-progress tracking: Manufacturers can monitor the status of items throughout production, identifying bottlenecks immediately.
- Quality assurance: By capturing data at every stage of manufacturing, MES ensures compliance with quality standards.
- Data analysis and reporting: MES offers analytical tools that help manufacturers make informed decisions based on production metrics.
- Improved worker productivity: Operators equipped with real-time data can perform their tasks more effectively, resulting in less downtime.
Adoption of MES systems must be carefully planned. The integration into existing workflows requires training and sometimes a shift in existing organizational culture, which can be challenging.
"In today’s fast-paced manufacturing environment, effective use of software can mean the difference between staying competitive and falling behind."
By investing in the right software solutions, manufacturers not only streamline their processes but also prepare for future technological advancements that are rapidly transforming the industry.
Challenges and Considerations in Discrete Manufacturing
The world of discrete manufacturing isn't just a walk in the park; it’s more like navigating a maze filled with unforeseen obstacles and tight corners. As companies churn out distinct items—from intricate machinery to sophisticated electronic gadgets—they must grapple with several challenges that can’t be glossed over. Properly addressing these elements can significantly enhance efficiency and quality, thus making this section a cornerstone of this article. Let’s explore the key considerations that underscore the challenges in discrete manufacturing, focusing on quality control and regulatory compliance.
Quality Control and Assurance
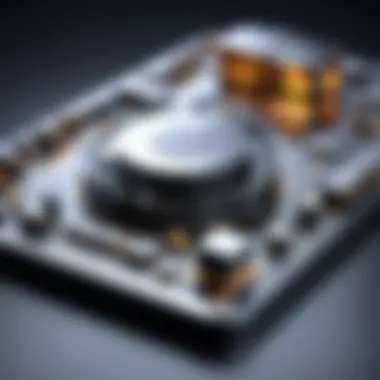
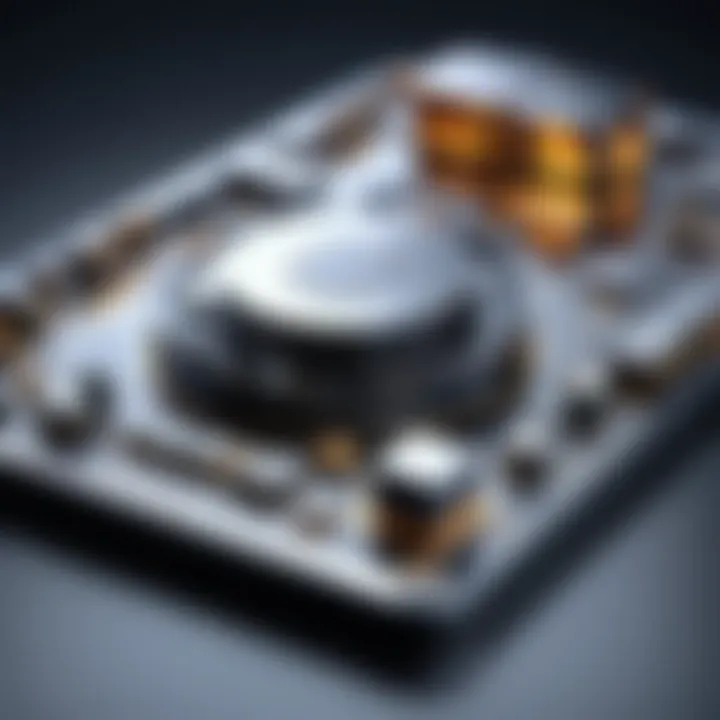
Quality control in discrete manufacturing acts like a hawk, keeping a vigilant eye on the production process to ensure that every unit meets a stringent standard. The need for rigorous quality checks cannot be overemphasized; if a product falls short, it can lead to costly recalls or tarnished reputations. Here are some factors that come into play:
- Consistency: Each product must not only meet specs but also look and feel the same. Consumers expect reliability,
- Error Reduction: Early detection of defects saves time and money downstream.
- Feedback Loops: Continuous monitoring allows for immediate adjustments based on real-world performance.
Moreover, as manufacturing processes become more complex due to technological advancements, the implementation of tools like Statistical Process Control becomes vital. It helps in predicting outcomes and catches potential issues before they escalate. In this competitive landscape, companies must prioritize quality assurance not just as an afterthought but as a central tenet of their operational ethos.
"Quality is not an act, it is a habit."
— Aristotle
Regulatory Compliance
Regulatory compliance is another daunting hurdle in the realm of discrete manufacturing. Companies must navigate a web of rules and regulations that vary by industry and region. Ignoring these can lead to hefty fines, legal troubles, or worse. Not delivering on compliance can compromise not only a business but also its customers. Some essential aspects include:
- International Standards: Many companies need to comply with ISO certifications, ensuring that they adhere to globally accepted criteria.
- Health and Safety Regulations: The well-being of workers must always come first, so manufacturers must implement guidelines that minimize workplace risks.
- Environmental Regulations: Manufacturers are required to follow laws regarding waste disposal and emissions, aligning with sustainability practices becoming ever more important.
Navigating these waters requires not just an understanding of production but also a deep dive into legalities. Staying updated and compliant helps build trust and credibility with customers. Truly, compliance is not merely a checkbox on a list; it’s a strategic part of business planning.
In summary, as discrete manufacturers face multi-layered challenges, both quality control and regulatory compliance serve as pivotal considerations that shape their operations. Ignoring these challenges is akin to sailing without a compass, risking the loss of direction amid the tides of fierce industry competition.
Strategies for Enhancing Manufacturing Efficiency
The pursuit of efficiency within discrete manufacturing is not just a fleeting ambition; it’s a fundamental necessity. In an age where market competition is fierce and consumer demands are ever-evolving, manufacturers must adapt and optimize their processes. The strategies that enhance manufacturing efficiency serve not only to cut costs but also boost productivity and maintain product quality. Each strategy should be carefully tailored, taking into account the unique challenges and strengths of a given organization.
Lean Manufacturing Principles
Lean manufacturing is centered on the idea of waste reduction without sacrificing productivity. The term ‘waste’ encompasses anything that does not add value to the final product. By focusing on eliminating non-value-adding activities, manufacturers can streamline their processes.
Key principles of lean manufacturing include:
- Identifying Value: Understanding what the customer sees as value helps guide efforts for improvement.
- Value Stream Mapping: This involves analyzing the flow of materials and information throughout the manufacturing process to pinpoint bottlenecks.
- Continuous Improvement: The philosophy of Kaizen urges ongoing analysis and tweaks to improve efficiency.
Implementing lean principles can result in a smoother operation where excess inventory sits idle no more. One organization that embraced these principles is Toyota, which has become a case study for lean production, showing how efficiency can lead to substantial cost savings and enhanced quality.
Six Sigma Methodology
Six Sigma emphasizes the removal of defects and the reduction of process variability. The methodology employs statistical tools and techniques with the goal of achieving a level of perfection in manufacturing of no more than 3.4 defects per million opportunities.
Some significant aspects of Six Sigma include:
- Define, Measure, Analyze, Improve, Control (DMAIC): A structured problem-solving process that engineers can use to improve existing processes.
- Data-Driven Decisions: Six Sigma relies heavily on data analysis which assists organizations in understanding their process variability and performance levels.
- Employee Involvement: Engaging employees at all levels encourages a culture of quality and shared responsibility.
By adopting Six Sigma, companies like General Electric have reaped financial awards while enhancing product trustworthiness. This methodology is not simply a buzzword but a pathway towards gaining competitive advantage through precision and quality.
Kaizen Approach
Kaizen, which means "change for the better" in Japanese, is about cultivating a culture of continuous improvement. Unlike large-scale changes, kaizen emphasizes small, incremental advancements.
Adjustments can include:
- Workplace Organization: Often referred to as 5S, this strategy organizes a workspace for efficiency and effectiveness by simplifying the environment.
- Team Involvement: Employees are encouraged to share ideas and propose solutions.
- Regular Reviews: Periodic assessments ensure that improvements are yielding positive results and allow for ongoing refinement.
One practical example involves the airline industry, where many companies deploy Kaizen methodologies to improve turnaround times, resulting in not only efficiency gains but also enhanced customer satisfaction and loyalty.
Epilogue
Employing these strategies for enhancing efficiency in discrete manufacturing is integral to long-term success. As industries evolve, so must the approaches to maintain competitiveness and adaptability. Organizations that embrace these methodologies put themselves in a prime position to excel in a demanding market. By focusing on lean principles, incorporating Six Sigma, and fostering a culture of continuous improvement with Kaizen, manufacturers can forge a path towards operational excellence.
"Efficiency is doing better what is already being done." – Peter Drucker
In this fast-paced manufacturing landscape, these principles offer substantial benefits and establish a framework for sustainable growth as well as profitability.
The Impact of Industry 4. on Discrete Manufacturing
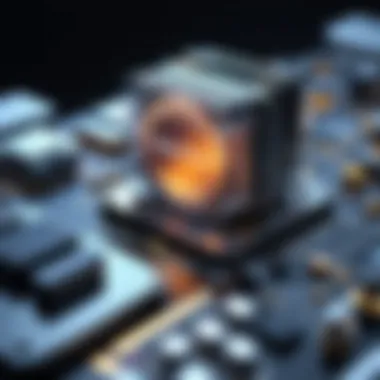
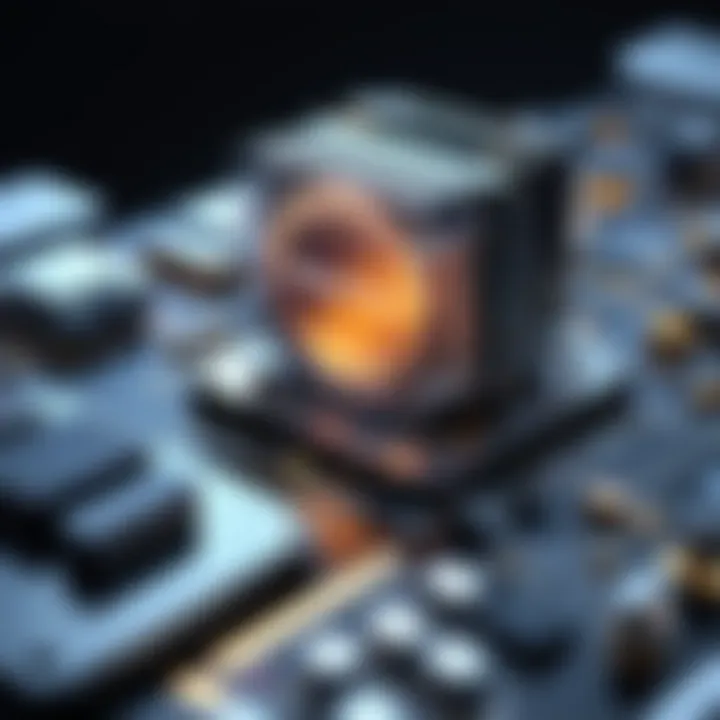
Industry 4.0 represents a transformative shift in how manufacturing processes operate. For discrete manufacturing, where tangible products are made to order, the principles of Industry 4.0 can unlock new realms of efficiency, productivity, and customization. It’s a blend of advanced technologies like the Internet of Things (IoT), AI, and machine learning that creates a smarter production environment. The significance of this shift cannot be overstated; embracing these changes is vital for companies aiming to stay relevant in a rapidly evolving market.
With Industry 4.0, discrete manufacturing embraces a more interconnected approach, allowing for better data sharing and agile responses to market demands. The emphasis here is on flexibility and responsiveness — traits that can directly impact a company’s bottom line. For instance, by integrating advanced software systems, manufacturers can optimize their operations based on real-time data, offering a clear edge over competitors.
"Industry 4.0 is not just a technological evolution; it's a revolutionary change in the manufacturing mindset."
Smart Factories
Smart factories are the cornerstone of Industry 4.0. These are highly digitized and connected production facilities that utilize smart sensors, robotics, and data analytics to streamline operations. In a smart factory, machines communicate with each other, exchanging data seamlessly to enhance productivity and minimize downtime.
The benefits of smart factories are vast:
- Increased Efficiency: Automated systems manage production schedules, ensuring minimal waste and maximized output.
- Better Quality Control: Real-time monitoring allows for immediate detection of deviations, enabling quick adjustments to maintain product quality.
- Enhanced Flexibility: Smart factories can swiftly adjust to variations in demand, allowing manufacturers to adapt their production lines as needed.
A prime example of this can be seen in automotive manufacturing, where processes are increasingly relying on IoT. Sensors in manufacturing equipment can monitor performance and alert operators to potential issues before they escalate, reducing costly shutdowns.
Predictive Maintenance
Predictive maintenance is another vital component of Industry 4.0 that helps maintain the operational integrity of discrete manufacturing facilities. Through data collected from various machinery, manufacturers can predict when maintenance should occur, rather than adhering to a fixed maintenance schedule.
This proactive approach has several advantages:
- Cost Savings: Reducing unexpected breakdowns can significantly lower maintenance costs and production delays.
- Increased Reliability: Knowing when a machine is likely to fail enables timely interventions, ensuring that machinery operates at peak efficiency.
- Extended Equipment Lifespan: Addressing issues before they become critical can prolong the life of expensive manufacturing equipment.
To implement predictive maintenance, companies typically utilize data analytics tools that collect and analyze performance data, allowing them to establish maintenance schedules based on usage patterns and historical performance. This technique not only boosts efficiency but also contributes to a more sustainable manufacturing approach, thereby aligning with broader trends in corporate responsibility.
Future Trends in Discrete Manufacturing
As the landscape of manufacturing continually evolves, staying ahead of the curve is crucial for industry leaders and decision-makers. Understanding the future trends in discrete manufacturing not only helps businesses remain competitive but also aligns with sustainability efforts and the increasing demand for flexibility in production. This topic tackles the emerging paradigms influencing the sector and underscores the necessity of adapting to these changes for long-term success.
Sustainability Practices
The focus on sustainability has transformed from a mere trend to a fundamental expectation in the manufacturing realm. Companies are now scrutinizing their practices, not only for compliance but also for community engagement and global responsibility. Here are some critical aspects of sustainability in discrete manufacturing:
- Resource Efficiency: By optimizing resource use, manufacturers can minimize waste. Companies are investing in technologies that track material flows and energy consumption to promote efficiency.
- Eco-friendly Materials: The shift toward using sustainable materials is gaining momentum. For instance, biodegradable composites and recycled metals are seeing heightened interest. The call for greener products resonates with today's environmentally conscious consumers.
- Reduced Emissions: There’s a growing emphasis on reducing carbon footprints. Manufacturers are exploring renewable energy sources and adopting more efficient production techniques to cut emissions during the manufacturing process.
Implementing these practices not only benefits the environment but also enhances brand loyalty among customers who value sustainability.
"In tomorrow’s market, sustainability isn't just a choice—it's a necessity for survival."
Customization and Modular Manufacturing
Customization has always been a hallmark of discrete manufacturing, but today’s consumer expectations push it to new heights. The prominence of modular manufacturing — the ability to create products using interchangeable parts — is central to addressing these demands effectively. Here’s how customization and modularity shape the future:
- Quick Responsiveness: Modular systems allow for rapid adaptation to market changes or consumer preferences. This flexibility can lead to shorter lead times and better alignment with local demands.
- Scalability: Businesses can expand their offerings without a complete overhaul of their production systems. If a manufacturer introduces a new product line, they can easily integrate new modules into existing processes, creating an environment conducive to innovation.
- Cost Efficiency: Streamlining the production through modular components can lower costs. Less waste occurs when manufacturers utilize the same modular pieces across different product lines, reducing inventory and simplifying logistics.
In a market leaning toward personalization, the ability to customize products while maintaining efficiency through modular design presents a win-win situation for both manufacturers and consumers.
Epilogue: The Road Ahead for Discrete Manufacturing
As we draw our exploration of discrete manufacturing to a close, it becomes clear that the trajectory of this field is heavily influenced by the rapid advancement of technology and shifting market demand. Discrete manufacturing isn't just about creating tangible goods like machinery or electronics; it’s about adapting to a landscape that’s more complex and interconnected than ever before. This adaptability is crucial for businesses to stay relevant in a competitive economy.
Summary of Key Points
In reviewing key aspects of this discourse, several important points emerge:
- Technological Evolution: The impact of Industry 4.0 is transformative. Technologies such as IoT, automation, and artificial intelligence are no longer just enhancements but essential components of the manufacturing ecosystem.
- Sustainability Concerns: With increasing consumer awareness regarding environmental impact, there’s a strong push towards sustainable practices. Manufacturers must embrace eco-friendly processes and materials to meet customer demand and regulatory requirements.
- Customization and Consumer Demand: The trend towards individualization of products requires that manufacturers become more flexible. This has led to the rise of modular manufacturing practices that enable faster adaptations to specific client needs.
- Regulatory Landscape: Compliance remains a critical issue. Navigating through complex regulations while ensuring product quality is paramount.
"The future of discrete manufacturing lies in the ability to pivot quickly without sacrificing quality or efficiency."
Implications for Industry Advisors
For decision-makers and industry advisors, understanding the current and evolving landscape of discrete manufacturing has far-reaching implications:
- Strategic Insights: Advisors must guide organizations in leveraging technological advancements to streamline operations and improve product offerings. This requires a strong grasp of emerging technologies and how they can be integrated effectively.
- Market Positioning: Staying abreast of trends such as sustainability and customization enables advisors to help companies strategically position themselves to capitalize on new markets and opportunities.
- Risk Management: Understanding regulatory risks and developing compliance strategies can safeguard organizations from potential penalties and reputational harm.
- Investment in Innovation: Advisors should advocate for ongoing investment in R&D. This ensures that the businesses they work with stay ahead of the curve and are capable of adapting to the fast-paced changes in industry expectations.
By synthesizing these insights, industry advisors can not only help organizations navigate current challenges but also prepare them for the future. The road ahead for discrete manufacturing is filled with potential, but tapping into that potential requires astute observation, deep industry knowledge, and adaptive strategies.