Mastering Industrial Construction Estimating
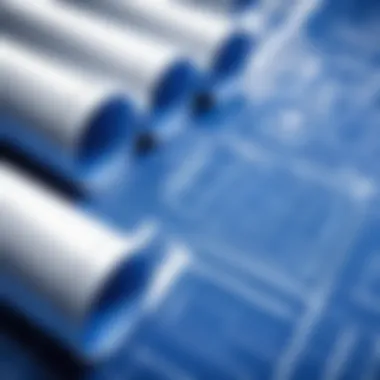
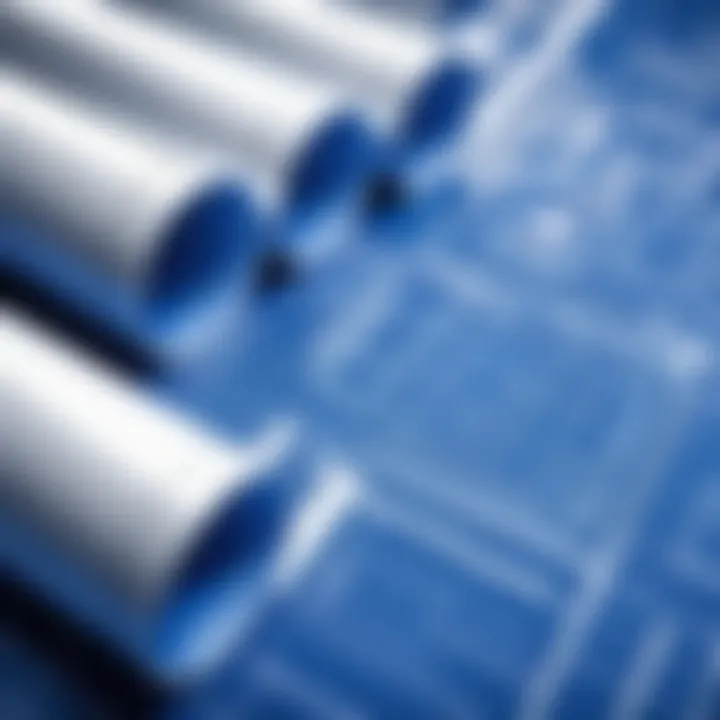
Intro
Industrial construction estimating is a specialized field that holds critical significance in project management. Accurate estimating enables professionals to allocate resources efficiently and maintain budget control. This guide aims to discuss various methodologies, tools, and best practices that specialists employ to ensure precise cost estimates. Additionally, it will touch on the challenges estimators face and how advances in technology can enhance accuracy in predictions.
Through a carefully structured overview, decision-makers and industry professionals will gain insights into the intricacies of industrial construction estimating. Comprehending these elements not only aids in project completion but also enhances strategic planning in resource management.
Understanding Industrial Construction Estimating
In the realm of industrial construction, accurate estimation serves as a foundational pillar for project success. This section highlights the essential elements that define industrial construction estimating while also emphasizing its significance in effective resource management and budget allocation.
Definition and Scope
Industrial construction estimating can be defined as the process of predicting the costs associated with a construction project. It involves analyzing various factors such as materials, labor, equipment, and time. The scope of this estimation process extends beyond merely calculating costs; it also encompasses evaluating risks and determining project feasibility. This requires construction professionals to have a comprehensive understanding of both the specific project requirements and broader market trends.
Typically, estimation in industrial construction might involve:
- Direct costs: These include materials and labor directly associated with the construction activities.
- Indirect costs: Such as overhead expenses and administrative costs that support the project.
- Contingencies: Funds set aside to address unforeseen issues or variances in project scope.
- Profit margins: The anticipated return for the contractors or stakeholders.
The depth of analysis required in this field makes it critical to engage with precise data and expert methodologies.
Importance of Accurate Estimation
Accurate estimation is more than a procedural requirement; it is essential for mitigating risks and ensuring seamless project execution. When cost estimates are flawed, the repercussions can be severe, leading to potential project overruns and resource misallocation. The following points illustrate why accuracy in estimation is vital:
- Budgeting: Reliable estimates allow for effective budgeting, guiding how resources will be allocated throughout the project lifetime, thus preventing financial surprises later.
- Decision-making: Stakeholders rely on accurate estimates to make informed decisions regarding project feasibility, timeline, and risk assessment.
- Resource optimization: Proper estimation helps in optimizing the use of resources by ensuring that funds are used efficiently.
- Competitiveness: Companies that provide more accurate estimates can secure contracts more easily compared to competitors who may lack precision.
Accurate estimation influences the overall health of a project, impacting timelines, profitability, and stakeholder satisfaction.
The role of accurate estimating in industrial construction can not be overstated. By prioritizing precision in the early stages of construction planning, companies can lay a strong foundation for project success, ensuring not just compliance but also the satisfaction of all parties involved.
Key Factors Influencing Cost Estimation
Cost estimation in industrial construction is a multifaceted process. It involves several critical elements that directly impact the accuracy and reliability of budget forecasts. Understanding these factors is crucial for decision-makers and project managers. Each component not only influences the overall project cost but also shapes risk assessments and resource allocation during the project lifecycle.
Raw Materials and Supply Chain
Raw materials constitute a significant portion of construction costs. The pricing and availability of these materials fluctuate based on market demand, geopolitical events, and supply chain dynamics. For example, steel and concrete prices can vary widely, influenced by tariffs or regional shortages. As a result, it is essential to develop a strategy for sourcing materials that accommodates potential fluctuations in cost.
Mitigating these fluctuations involves maintaining good relationships with suppliers, understanding the market landscape, and sometimes, purchasing in bulk during favorable pricing periods. This proactive approach can help to ensure that material costs remain as predictable as possible. Keeping abreast of market trends and engaging in effective inventory management are vital to reducing disruption impact on project timelines and budgets.
Labor Costs
Labor represents another crucial expense in the industrial construction sector. The cost of labor can vary based on geographic location, skill levels required, and current economic conditions. To accurately estimate labor costs, project managers must account for wage rates, benefits, and productivity levels.
Additionally, local labor laws and union agreements may play a role. Utilizing labor costing software can help track these variables effectively. It is also important to consider the availability of skilled labor as a factor in your estimation. A shortage of qualified workers can lead to increased wages or project delays. Therefore, planning for labor needs is essential in establishing a realistic budget and ensuring project timeliness.
Equipment and Tools
Equipment and tools significantly influence the overall cost of industrial construction projects. Rental or purchase decisions must be carefully evaluated to compare long-term versus short-term costs. The type of equipment needed can differ based on the scope and complexity of the project.
Using modern, efficient equipment may offer substantial long-term savings. Nevertheless, concerns related to maintenance, operational efficiency, and upfront costs must also be considered. Comprehensive planning around equipment utilization can lead to increased productivity and reduced idle time.
Also, including a contingency budget for unexpected equipment breakdowns or the need for specialized tools can protect against unintended expenses. Consideration must also be given to how equipment choices affect labor costs, as more advanced machinery may require fewer personnel or increase productivity among existing teams.
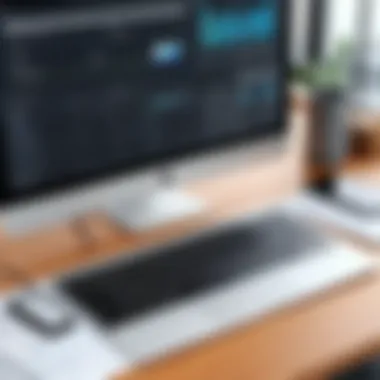
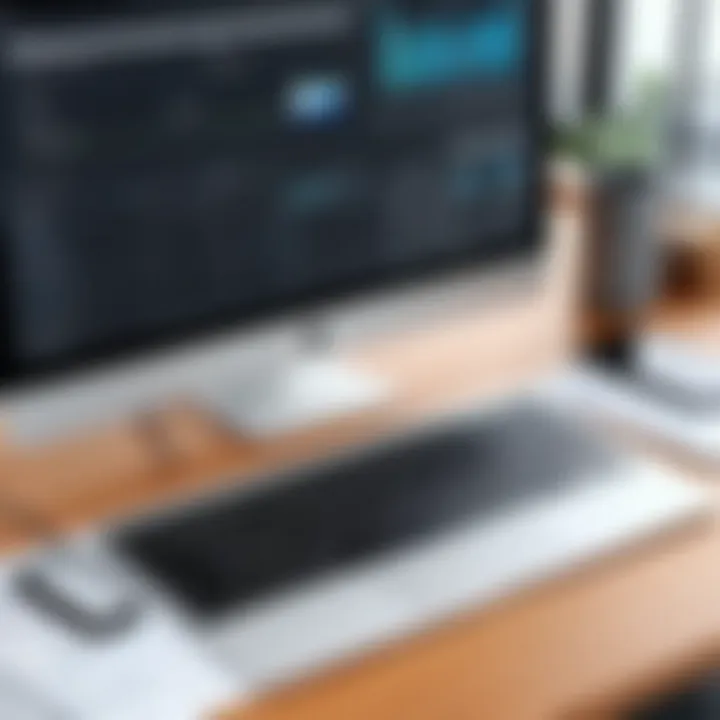
It is essential to factor in the complete lifecycle costs of equipment and tools when estimating budgets.
Estimation Methodologies
Estimation methodologies play a crucial role in the realm of industrial construction estimating. They provide a structured framework to derive cost estimates that guide project budgeting and resource allocation. Each methodology offers unique benefits and considerations, ensuring accuracy while minimizing risks associated with budget overruns. Understanding these different approaches is essential for decision-makers who need reliable data to inform their choices in construction projects.
Top-Down Estimating
Top-Down estimating is an approach where the overall project cost is estimated first, then broken down into specific components. This method is beneficial when there is limited project detail available during the early stages. Experts gather high-level assessments that factor in similar previous projects and broader market data. It allows management to set a preliminary budget quickly.
However, this method can lead to inaccuracies if base assumptions are off. It may overlook critical details affecting specific cost sections.
Bottom-Up Estimating
Bottom-Up estimating focuses on individual components of a project. Each part is estimated in detail, and totals are rolled up to formulate the overall project cost. This methodology is thorough and ensures no critical element is missed. It is advantageous when project details are well understood, improving the accuracy of estimates.
Nonetheless, it can be time-consuming, requiring extensive data and coordination. A careful balance must be struck between detail and efficiency.
Analogous Estimating
Analogous estimating uses historical data from similar projects to create quick estimates. This method relies on the experience and judgment of estimators to adjust figures based on differences in project scope and environment. It is particularly useful during the early project phases when quick approximations are needed.
While it provides speed, the accuracy of this method hinges on the relevance of the projects used for comparison. Significant differences in scope can lead to misleading estimates.
Parametric Estimating
Parametric estimating involves statistical relationships between historical data and other variables. It employs formulas to calculate costs based on defined parameters, like cost per square foot or materials quantities. This method provides quantitative insights, allowing for more objective calculations.
The downside is that the assumptions made in the parameters can greatly impact accuracy. Hence, reliability is dependent on data quality and relevance.
In summary, selecting the right estimation methodology is vital. Each method has its advantages and limitations, and the choice often hinges on project specifics. For successful outcomes in industrial construction, professionals should consider using a combination of methods to complement each other, ensuring that estimates are both accurate and practical.
"Accurate estimations set the foundation for sound decision-making in project management."
Understanding how to navigate through these methodologies can enhance the estimation process and lead to better project outcomes.
The Role of Software in Construction Estimating
In today’s industrial construction environment, software plays a crucial role in enhancing estimating processes. This technology enables professionals to produce more precise cost estimates with less time and effort. Effective estimating software integrates various data sources, simplifies calculations, and supports real-time collaboration among stakeholders. As project complexity increases, the need for robust systems that can handle diverse project requirements becomes essential.
Utilizing software not only enhances transparency but also reduces human error, which is a common challenge in manual estimating. Accurate estimates are vital for budget control and resource allocation. Thus, the right software can greatly influence project outcomes, aiding in both efficiency and profitability.
Key Features of Estimating Software
Estimating software comes with key features designed to make the cost estimation process smoother and more accurate. Some notable features include:
- User-friendly Interface: An intuitive interface allows users to navigate easily, reducing training time and increasing productivity.
- Cost Databases: Access to up-to-date material and labor cost databases ensures accurate and current estimates.
- Customizable Templates: Tailorable templates facilitate quick setup for various projects, allowing for streamlined processes.
- Integration Capabilities: Good estimating software connects with other project management tools, enabling seamless data sharing and collaboration.
- Reporting Tools: Built-in reporting features provide insights into project costs, budget variances, and more.
These features not only simplify the estimating process but also provide the necessary insights for stakeholders to make informed decisions.
Popular Estimating Software Solutions
Several software solutions dominate the market, catering to the needs of professionals in industrial construction estimating. Some prominent options include:
- Sage Estimating: Known for its comprehensive databases and integration capabilities, Sage Estimating is widely used for its reliable performance.
- Bluebeam Revu: This software excels in document management and includes tools for cost estimation, making it a popular choice among professionals.
- PlanSwift: It focuses on takeoff and estimation, facilitating accurate measurements and quick data processing.
- ProEst: ProEst stands out with its cloud-based platform and user-friendly features, allowing for effective collaboration across teams.
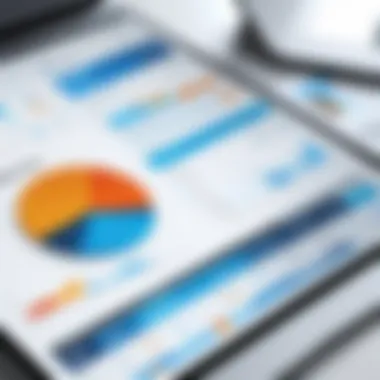
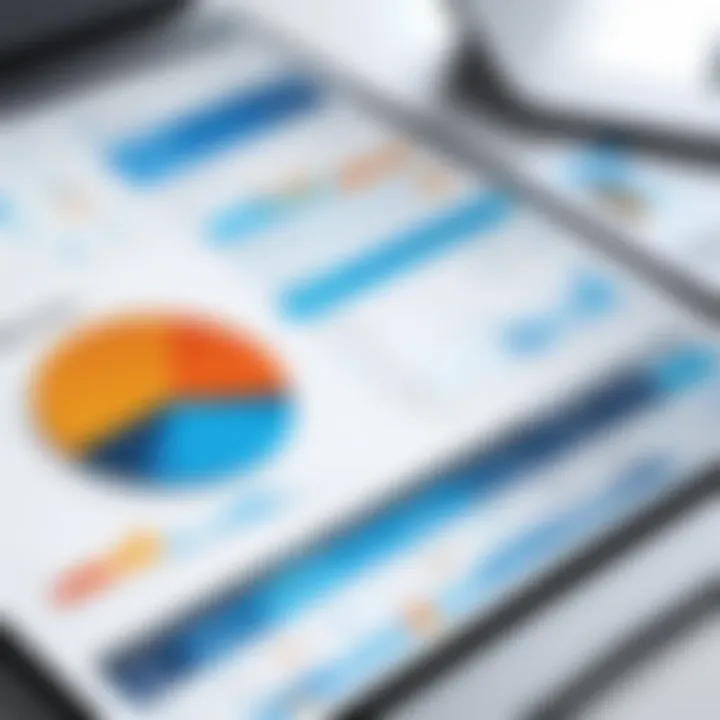
Each of these solutions has distinct advantages tailored for different project needs, thereby improving efficiency and accuracy in the estimating process.
Challenges in Industrial Construction Estimating
The field of industrial construction estimating is fraught with numerous challenges. Understanding these challenges is essential for accurate project assessments and financial planning. Each project differs based on various factors including size, scope, and location. As such, overcoming obstacles becomes crucial to keep projects on track and within budget. The three most notable challenges include market volatility, inaccurate data inputs, and constantly changing regulations.
Market Volatility
Market volatility has a significant impact on the industrial construction sector. Prices for raw materials can fluctuate dramatically due to various factors, including geopolitical tensions and changes in export regulations. These fluctuations can lead to unexpected increases in project costs. For instance, when the price of steel or lumber rises, the overall budget for a construction project may become outdated very quickly.
By monitoring market trends and integrating real-time data into the estimation process, professionals can minimize the risk associated with these changes. Adopting flexible estimating methods can also help accommodate price alterations. Understanding historical market behavior provides insight into potential future fluctuations, allowing estimators to make better-informed decisions.
Inaccurate Data Inputs
Inaccurate data inputs are another major challenge. Cost estimators rely on various sources of data to develop their estimates accurately. If the data is flawed or outdated, the finished estimate may not reflect the true costs. For example, labor rates vary by location and can change frequently. Therefore, inaccuracies in labor cost data can lead to significant overruns during a project.
To mitigate this issue, it is vital to ensure that data is regularly updated and verified. Employing robust data management systems can streamline this process. Regular audits of estimation tools help maintain data integrity and consistency. Collaborating with experienced professionals who understand local markets can also enhance the accuracy of the data inputs used in the estimation process.
Changing Regulations and Standards
The construction industry is subject to various regulations and standards that often evolve. New safety, environmental, and labor regulations can cause fundamental shifts in project costs. Keeping up with these changes is necessary, as non-compliance can result in costly penalties and project delays.
For instance, updates in sustainability regulations may require additional green materials or specific construction methods that were not originally accounted for in the budget. To navigate this uncertainty, it's essential for estimators to maintain a forward-thinking approach regarding regulatory changes. Engaging with legal and compliance experts can aid in accurately predicting how these regulations might affect future costs.
By addressing these challenges head-on, organizations can improve their estimating accuracy. This leads to more efficient project management and ultimately better financial performance.
The Impact of Technology on Estimating Practices
The integration of technology into industrial construction estimating has profoundly reshaped how projects are approached and managed. This section delves into the significance of technological advancements and how they contribute to enhancing accuracy and efficiency in the estimating process. Technology not only streamlines data collection and processing but also facilitates better decision-making through advanced analytical capabilities. Understanding these changes is crucial for professionals who aim to remain competitive in an evolving market.
Digital Transformation in Estimating
Digital transformation refers to the incorporation of digital technologies into all aspects of business operations, leading to fundamental changes in how organizations operate and deliver value. In the context of industrial construction estimating, this transformation encompasses various platforms and tools that aid in creating accurate estimates.
- Cloud-Based Solutions: These services enable real-time collaboration among team members regardless of their location. They allow for seamless updates to cost estimates and facilitate communication among stakeholders.
- Mobile Applications: Field workers can capture data on-site, which reduces the time lag between data collection and analysis. This immediacy enables more accurate estimations because it reflects the current site conditions.
- Data Management Systems: Advanced software tools help track and manage historical data about past projects. This data can serve as a valuable reference point for future estimates, allowing for more informed and precise calculations.
The shift to digital methods ensures a streamlined approach, reducing human error and allowing construction professionals to focus on strategic aspects of estimating rather than getting bogged down by manual tasks. As a result, the industry can respond more agilely to market fluctuations and project changes.
Use of AI and Machine Learning
Artificial Intelligence (AI) and Machine Learning (ML) are redefining how industrial construction estimating is done. These technologies harness vast amounts of data to improve predictive accuracy.
- Predictive Analytics: AI algorithms can analyze historical project data to predict future costs more accurately. They identify patterns in expenses and resource usage, which leads to refined estimates.
- Cost Modeling: Machine learning models can create dynamic cost models that adapt as new data becomes available. This capability means estimates can evolve through the life of a project, providing continuous alignment with real-time factors.
- Risk Assessment: By integrating AI, estimators can better assess risks associated with various scenarios. AI tools can simulate different project variables, assisting in identifying potential cost overruns before they occur.
Best Practices for Effective Estimating
Effective estimating is not merely a task but a critical process that shapes the entire framework of industrial construction projects. An accurate estimate serves as a roadmap, guiding project managers in decision-making and resource allocation. The integration of best practices ensures that estimates are not only reliable but also adaptable to changing circumstances. Several key aspects define these practices, which we shall discuss in detail below.
Establishing a Baseline Budget
Creating a baseline budget is essential for project success. This budget acts as a reference point throughout the project lifecycle. To establish a baseline, one must conduct a thorough analysis of requirements, including material costs, labor, and equipment needs. A well-structured baseline helps track actual spending against projected costs. Regularly revisiting this budget aids in identifying variance and understanding spending patterns over time. It is advisable to factor in historical data to increase reliability.
Key elements involved in establishing a baseline budget include:

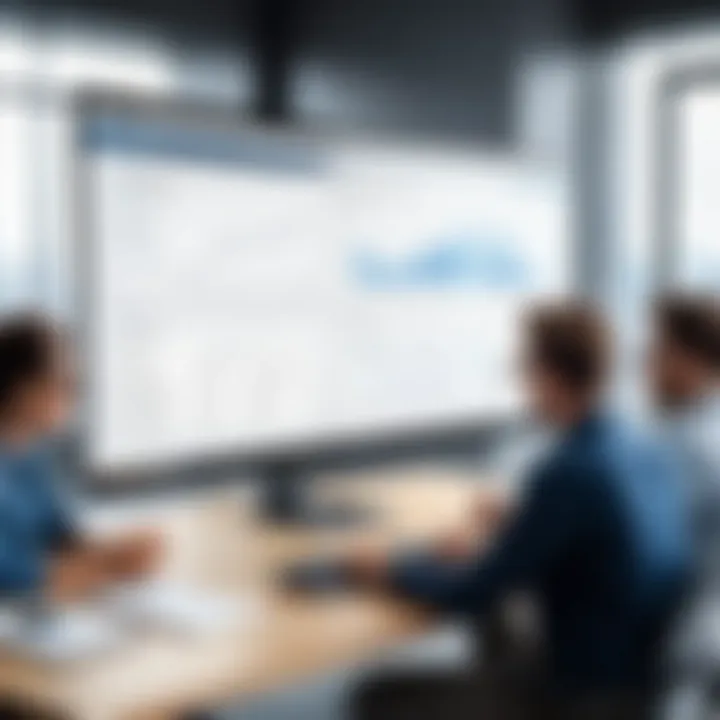
- Resource Evaluation: Identify all necessary resources for the project. This should include both tangible materials and workforce.
- Cost Analysis: Gather pricing information from previous projects or reliable suppliers. This data will help avoid unforeseen expenses later on.
- Stakeholder Input: Engage with all stakeholders to gather insights that might influence budget formation. This collaboration fosters transparency and shared understanding.
Incorporating Contingencies
Contingencies are an integral part of budgeting in industrial construction. They provide a cushion for unexpected events or cost overruns. Incorporating contingencies should be more than just an afterthought. It requires careful consideration of potential risks associated with the project.
When planning for contingencies, consider the following:
- Risk Assessment: Analyze potential risks that may impact the project. This includes economic fluctuations, supply chain issues, or design changes.
- Percentage Allocation: Typically, a contingency reserve ranges from 5% to 20% depending on risk levels. Adjust this percentage based on the complexity and uncertainties of the project.
- Flexible Adjustments: Regularly re-evaluate the contingencies as the project progresses. This adaptability will ensure that the project remains within budget while still being responsive to external factors.
Regular Review and Adjustment
A static estimate quickly becomes outdated. Therefore, regular review and adjustment are necessary to maintain accuracy and relevance. Continuous monitoring helps identify discrepancies and allows project managers to adapt as required. This practice not only minimizes the risk of going over budget but also improves the overall management of the project.
For effective review and adjustment, establish a routine that involves:
- Weekly or Monthly Checks: Set up a schedule for review meetings. Consistency is key to staying updated on project developments and challenges.
- Stakeholder Involvement: Involve essential stakeholders in these reviews. Their insights can provide valuable information for adjustments.
- Documenting Changes: Maintain a record of all adjustments and the reasons behind them. Documenting this process serves as a reference for future projects, improving overall effectiveness.
"Accurate and versatile estimating practices are foundational for successful project completion. By ensuring a comprehensive baseline, planning for uncertainties, and conducting regular assessments, projects can remain on track and within budget."
The Future of Industrial Construction Estimating
The landscape of industrial construction estimating is evolving rapidly. As industries adapt to technological advancements, it is crucial to explore the future of estimating practices. The integration of innovative tools and techniques promises not only to enhance accuracy but also to streamline workflows. Decision-makers must understand these changes to maintain competitive advantage. With a clear comprehension of future trends, professionals can optimize their estimating strategies and improve overall project success rates.
Emerging Trends
Several trends are shaping the future of industrial construction estimating. Among these, the increasing use of Building Information Modeling (BIM) stands out. BIM facilitates better visualization of projects and allows for more precise cost estimations. This tool fosters collaboration among stakeholders, from architects to project managers.
Another trend is the adoption of cloud-based estimating solutions. They enable real-time data sharing and communication between teams. This aspect reduces the potential for errors and enhances efficiency throughout the estimating process. Furthermore, mobile applications are becoming more prevalent for on-site data collection and reporting, allowing for quicker adjustments and greater flexibility in workflows.
- Key developments to watch include:
- Advanced software solutions that incorporate machine learning.
- Increased reliance on remote collaboration tools to accommodate widespread office closures.
- Growing importance of sustainable practices in cost calculation, aligning with global environmental goals.
Predictive Analytics in Estimating
Predictive analytics represents a remarkable evolution in the estimation process. By leveraging historical data, machine learning algorithms can accurately forecast future project costs. This predictive capability not only improves budgeting but also helps identify risks before they escalate.
Utilizing predictive analytics involves collecting vast amounts of data from past projects, including labor rates, material costs, and project durations. The software analyzes this data to identify patterns and trends, providing professionals with solid foundations for cost estimation.
"With predictive analytics, estimators can anticipate project challenges and allocate resources more effectively."
This transition to data-driven decision-making enhances the overall estimating process. Key benefits of adopting predictive analytics include:
- Enhanced Accuracy: Traditional estimating often relies on best guesses or outdated methods. Predictive analytics, on the other hand, applies relevant data to make informed decisions.
- Efficient Resource Management: Estimators can allocate budgets effectively by predicting future needs based on past performance.
- Improved Risk Assessment: Identifying potential issues in advance allows decision-makers to devise mitigation strategies before project initiation.
In summary, the integration of emerging trends and predictive analytics is vital for the future of industrial construction estimating. Professionals who embrace these advancements are likely to achieve improved accuracy and efficiency, ultimately leading to successful project outcomes.
The End
In the realm of industrial construction, the conclusion serves as more than just a summary of the preceding content; it encapsulates the essence of effective cost estimation and its significant influence on project success. As we conclude this guide, it is vital to recognize several key takeaways.
First, accurate estimating is foundational to budgeting. Well-crafted estimates enable decision-makers to allocate resources efficiently, minimizing the risk of budget overruns. When managers understand their costs, they can also set more realistic timelines, ultimately improving project delivery.
Moreover, embracing the methodologies outlined in this guide—such as top-down and bottom-up estimating—empowers professionals to choose the most appropriate approach based on specific project circumstances. Each method carries its strengths and weaknesses, making it crucial for estimators to analyze their needs thoroughly.
The integration of technology into estimating practices cannot be overstated. As highlighted, advanced software solutions and tools provide the analytical power needed to refine estimates and improve accuracy. By leveraging predictive analytics, teams can anticipate future trends and adjust their estimates accordingly— a clear advantage in today’s fast-paced environment.
Finally, the challenges faced in this field, such as market volatility and data inaccuracies, underscore the necessity of continuous review and adaptation. Only through vigilant monitoring can professionals ensure their estimates reflect changing conditions.
In summary, the importance of precise industrial construction estimating cannot be overlooked. It is not merely a financial exercise but a strategic element that interlinks various facets of project management. By adopting best practices and staying attuned to emerging trends, industry professionals can navigate this complex terrain successfully.