Comprehensive Guide to Tool Management Systems
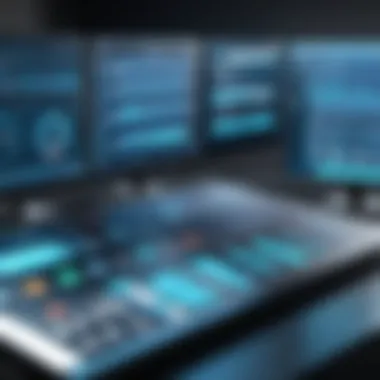
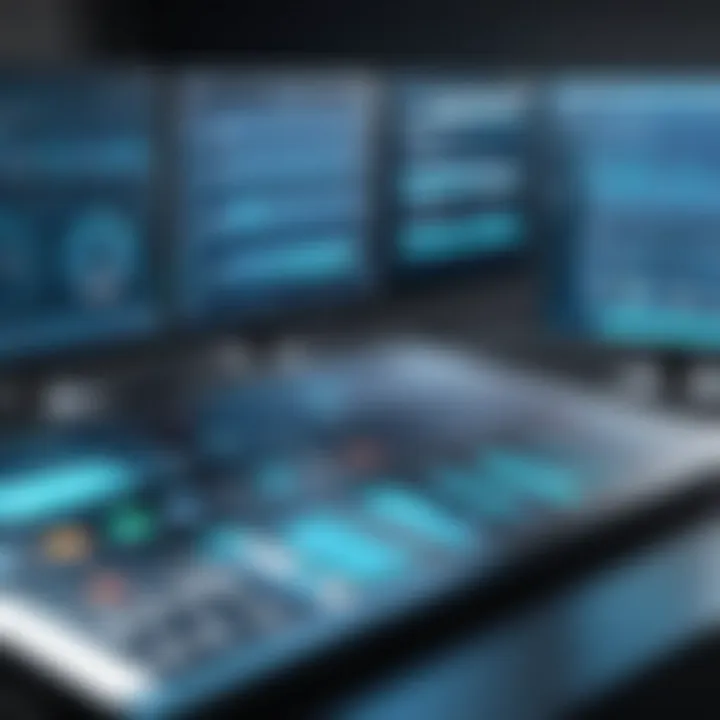
Intro
Tool management systems have become a pivotal aspect in various industries. These systems are designed to streamline the organization and deployment of tools, ensuring that each piece is accounted for and effectively utilized. In today’s fast-paced environment, where efficiency is king, the lack of a comprehensive tool management strategy can lead to significant setbacks. Thus, understanding the ins and outs of such systems is not just an option; it's a necessity for organizations striving to remain competitive.
This article will delve into every facet of tool management systems, from their core features to best practices for implementation. It will also explore the role technology plays in enhancing these functionalities, ensuring that decision-makers, IT professionals, and industry leaders are well-equipped to make informed choices in their tool management endeavors.
Software Overview
Brief Description of Software
A tool management system typically encompasses software solutions designed to track and manage tools used across various operations. From construction sites to manufacturing plants, the right software can facilitate proper tool allocation, maintenance schedules, and even costly loss prevention. By digitizing these elements, organizations can gain a clearer picture of their assets, leading to more proactive decision-making processes.
These software systems often operate from a centralized platform that integrates with other technologies, fostering seamless communication and functionality. Whether it is a cloud-based solution or an on-premise installation, the tool management software provides a comprehensive interface that helps users manage tools effectively and efficiently.
Key Features and Functionalities
When evaluating tool management systems, several key features stand out:
- Inventory Tracking: The ability to monitor tool availability and condition in real-time.
- QR Code/Barcode Scanning: Enables quick and easy check-in and check-out processes.
- Maintenance Scheduling: Helps in planning routine maintenance to prolong tool lifespan and reduce downtime.
- Reporting and Analytics: Provides insights into usage trends, helping make informed procurement decisions.
- User Access Control: Ensures that only authorized personnel can access specific tools, minimizing loss.
In today's context, many tools have gone digital with IoT integrations, where smart tools can report directly to the management software, further increasing efficiency.
Detailed Comparison
Comparison with Competitors
When selecting a tool management system, it's important to compare available options. Each software will have its strengths and weaknesses:
- ToolWatch: Focuses heavily on construction industries, providing robust tracking and maintenance features.
- GigaTrak: Offers strong inventory management suited for various sectors but is especially popular within manufacturing.
- Asset Panda: Known for its adaptability across industries but can be a bit pricey for smaller organizations.
Evaluating these providers against your specific requirements helps in narrowing down the best fit.
Pricing Structure
Pricing models for these systems can vary widely. Many offer subscription-based pricing, generally on a monthly or annual basis. Factors that influence the cost include:
- Number of Users: More users typically mean higher costs.
- Features Included: Advanced features usually come at a premium.
- Support and Maintenance Services: Ongoing support can add to the overall price.
Understanding these elements can lead to smarter financial planning and resource allocation.
"A thorough grasp of tool management systems not only saves costs but significantly boosts overall operational effectiveness."
Being aware of every aspect related to tool management systems will empower industry advisors and decision-makers to guide their companies into a future of productivity and efficiency.
Understanding Tool Management Systems
Understanding tool management systems is vital in today's fast-paced, efficiency-driven work environments. These systems go beyond mere inventory tracking; their core lies in streamlining operations that ultimately lead to cost reduction and enhanced productivity. For decision-makers, IT professionals, and entrepreneurs alike, comprehending these systems is crucial for making informed choices about implementing and optimizing processes in their respective domains.
Definition and Purpose
A tool management system can be defined as a structured approach that organizations adopt to oversee their tools and equipment throughout the entire lifecycle. The primary purpose of these systems is to ensure accountability, increase efficiency, and facilitate the effective utilization of resources. Think of it like having a digital toolbox where you not only know what tools you have but also where they are, their condition, and when they need maintenance. This level of oversight is particularly beneficial in industries with heavy machinery or specialized equipment, where downtime can be costly.
Key Components of Tool Management Systems
Several key components work in tandem to create an efficient tool management system. These components include:
- Inventory Tracking: Real-time monitoring of tool locations and statuses is a cornerstone, preventing tools from going missing and reducing search times.
- Maintenance Scheduling: Regular upkeep prolongs the lifespan of tools, reduces repair costs, and maintains safety standards.
- User Access Control: Defining who can access certain tools helps in minimizing unauthorized usage and maintains accountability.
- Data Reporting: Effective data analysis aids in making informed decisions in inventory management, procurement, and budgeting tasks.
Incorporating these components results in a robust framework_ that empowers organizations to manage their tools more effectively._
Historical Evolution of Tool Management
The concept of tool management has evolved significantly over the decades. In the early industrial era, tracking tools was often done manually, relying heavily on physical inventory counts. In those times, tools would be marked with chalk or tagged, a method that was labor-intensive and prone to error. As technology improved, the introduction of barcodes and basic inventory systems brought about a technological shift. Today, we experience sophisticated software solutions that leverage cloud computing and mobile applications, allowing organizations to manage tools remotely and view real-time data.
The transition from manual tracking to automated systems illustrates the drive towards efficiency. With each advancement in technology, organizations have realized greater value in monitoring their asset lifecycle more intricately, paving the way for continuous improvements in productivity and operational cost savings.
In summary, a robust understanding of tool management systems lays the foundation for effective operational strategies in various industries. This goes hand-in-hand with achieving greater visibility, efficiency, and accountability in managing assets.
The Importance of Tool Management Systems
In today's fast-paced industries, the significance of tool management systems cannot be overstressed. As enterprises expand and diversify, managing tools is no small feat. These systems play a quintessential role, offering a strategic advantage that transcends simple organization. When executed effectively, they drive operational efficiencies, reduce costs, and improve safety.
Enhancing Operational Efficiency
Operational efficiency is the backbone of any successful organization. Tool management systems streamline the workflow by ensuring tools are accounted for, accessible, and in good working condition. Consider a construction site: having the right tools at the right location, without searching high and low, can save precious time.
When tools and equipment are labeled and tracked, workers can find what they need quickly, reducing downtime. Additionally, these systems can send automated alerts for maintenance schedules, so no tool is left to gather dust or, worse, break down during critical tasks.
Some key ways tool management systems enhance efficiency include:
- Real-time Tracking: Knowing where tools are at any given moment minimizes delays.
- Inventory Optimization: Understanding usage patterns leads to smarter purchasing decisions and eliminates unnecessary spending on tools.
- Workflow Integration: Modern systems can tie into project management tools, allowing seamless updates and accurate project timelines.

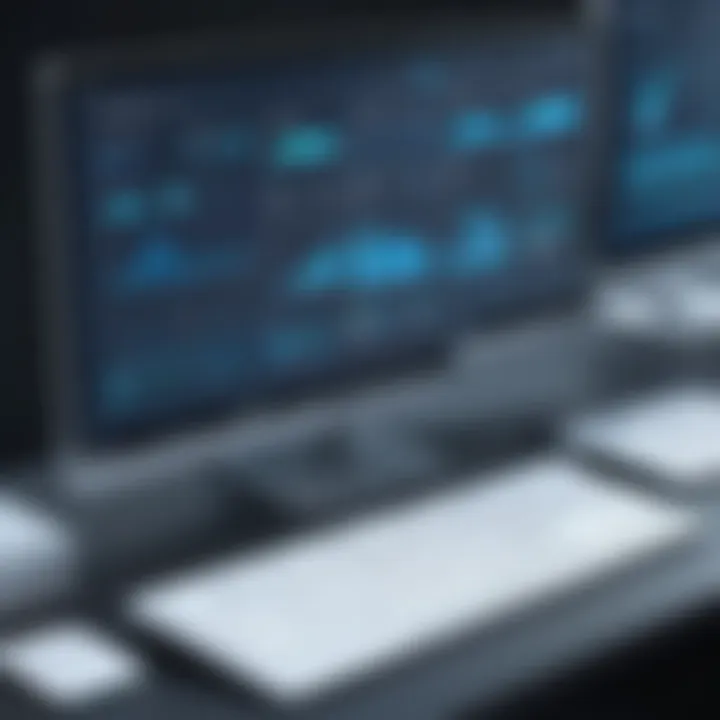
"Efficiency is doing things right; effectiveness is doing the right things."
Cost Reduction Strategies
Cost containment strategies are another layer where tool management systems shine. Misplaced, lost, or damaged tools can lead to hefty replacement bills and project delays. By implementing an effective management system, companies can significantly slash unnecessary expenditures.
Some crucial strategies include:
- Preventive Maintenance: Regular inspections facilitated by the system can help catch issues before they escalate. This means avoiding costly last-minute repairs.
- Usage Analytics: Analyzing which tools are most utilized can streamline future purchasing strategies, opting for those that yield the best return on investment.
- FIFO Management: First-In-First-Out strategies ensure older tools are used before newer ones, depreciating the tools appropriately over time and maximizing the lifespan of all assets.
Improving Safety and Compliance
Safety is non-negotiable in any working environment. Tool management systems also play a pivotal role in enhancing workplace safety. With stringent regulations across various industries, compliance becomes easier when tools are well-managed.
Here are some important aspects of how tool management systems contribute to safety:
- Inventory Control: Knowledge of where tools are and their proper maintenance status contributes to reducing accidents and injuries. Tools that undergo regular checks are less likely to malfunction.
- Tracking Historical Data: Keeping records of tool usage and maintenance helps comply with safety regulations and allows for audits if necessary.
- Standard Operating Procedures: Integrating a management system can facilitate uniformity in how tools are used, further driving down potential hazards.
Types of Tool Management Systems
Understanding the various types of tool management systems is crucial for decision-makers grappling with the complexities of their operational needs. Each system offers unique features and benefits, tailored to specific environments and requirements. By recognizing these differences, businesses can select tools that not only enhance productivity but also align with their strategic objectives.
Manual vs. Automated Systems
In the world of tool management, systems can generally be broken down into manual and automated categories.
Manual systems are the traditional approach, where inventory tracking and management rely heavily on human input. This might involve spreadsheets or physical logs to keep tabs on tools and their usage. While this method is cost-effective and straightforward, it comes with notable challenges, such as increased chances of human error and time-consuming processes.
On the other hand, automated systems integrate technology to streamline operations, employing software solutions to track tools more accurately. They use features like barcode scanning, RFID tracking, and cloud storage. The convenience of real-time updates and reduced labor-intensive tasks makes automated systems highly appealing for contemporary businesses.
A comparison of these systems might look like this:
- Manual Systems:
- Automated Systems:
- Low initial costs
- High labor requirements
- Increased risk of errors
- Higher upfront investment
- Saves time and labor
- Reduces human error
Ultimately, the choice between manual and automated systems hinges on an organization's size, budget, and operational complexity.
Best-of-Breed Solutions
When discussing tool management systems, best-of-breed solutions emerge as a compelling option. These systems are specialized tools designed to perform specific functions exceptionally well. They often address particular pain points organizations face in managing their tools, making them valuable for niche applications.
For example, a construction company may benefit from a best-of-breed inventory tracking solution that provides in-depth reporting on tool usage and maintenance schedules, tailored to the unique challenges of the construction industry. By focusing on excellence in specific areas, these solutions can deliver enhanced features compared to more generalized systems.
However, it's important to weigh the potential drawbacks as well. Best-of-breed systems may require integration with other software, leading to possible complexities in data sharing and communication.
Integrated Management Systems
The robust counterpart to best-of-breed systems is integrated management systems. These are comprehensive solutions that merge various functionalities into a single platform, enabling organizations to handle multiple aspects of tool management seamlessly.
For instance, an integrated system might combine inventory management, maintenance scheduling, and human resources functionalities, creating a centralized hub for data and operations. This can enhance data consistency and provide a holistic view of tool management across an organization.
Adopting an integrated system can be beneficial; however, potential implementation hiccups may occur, including learning curves and the need for significant changes to existing workflows.
In summary, choosing the right type of tool management system can significantly influence an organization's effectiveness. Understanding the distinctions between manual and automated systems, weighing the pros and cons of best-of-breed against integrated solutions, is essential in making informed decisions that cater to a business's unique needs.
"Selecting the appropriate tool management system is much like choosing the right tool for a job; the wrong one can lead to complications and inefficiencies."
Through careful consideration of the system types, organizations can harness the power of optimized tool management to drive growth and productivity.
Selection Criteria for Tool Management Systems
When it comes down to selecting the right tool management system, the decision can often feel like trying to find a needle in a haystack. The landscape is packed with options, each boasting its own set of features, but not all systems are created equal. In this section, we will dissect the necessary criteria that organizations, especially those in technical and operational roles, need to grapple with to make educated decisions.
Assessing Business Needs
The first step is to understand the specific needs of your business. This isn’t just about what’s handy but aligning the tool management system with your strategic goals. An organization’s requirements can differ widely based on size, industry, and operational complexity.
For instance, a small mechanical shop might primarily need a system for tracking a limited number of tools, while a large construction firm might require robust capabilities for handling many thousands of items and ensuring compliance with safety regulations.
To effectively assess needs:
- Identify Key Performance Indicators (KPIs): Define what success looks like for your tool management. Is it reduced downtime, improved asset utilization, or perhaps enhanced compliance?
- Engage Stakeholders: It’s beneficial to consult team members at various levels - from the shop floor to management. Their insights can highlight unique pain points and requirements.
- Map Current Processes: Understand existing workflows and how a new system can either complement or overhaul those methods to boost efficiency.
By being thorough in this assessment phase, you avoid the trap of selecting a system that looks good on paper but falls flat in real-world application.
Budget Considerations
Money talks in any business, and selecting a tool management system is no exception. Cost isn’t just about the initial investment, but should also encompass the total cost of ownership. Here are a few aspects to weigh:
- Upfront Costs: Consider not only the software or hardware expenses but also potential setup fees.
- Ongoing Expenses: Subscription fees, maintenance costs, and support charges can creep up over time. It’s prudent to factor these into your budget.
- Hidden Costs: Often overlooked costs like training and the need for additional staff can derail your budget.
- Return on Investment (ROI): Before diving in, assess how this tool will pay off. Will it save time? Reduce losses? Ultimately, aiming for systems that yield a favorable ROI is wise.
A clear financial plan allows you to sift through options thoughtfully rather than being lured by shiny features that stretch your budget too thin.
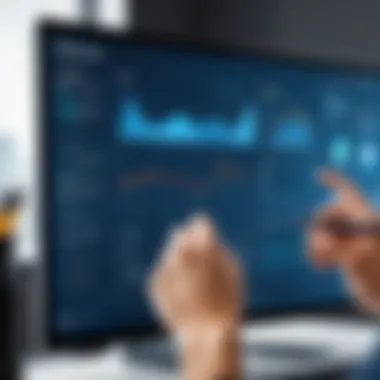
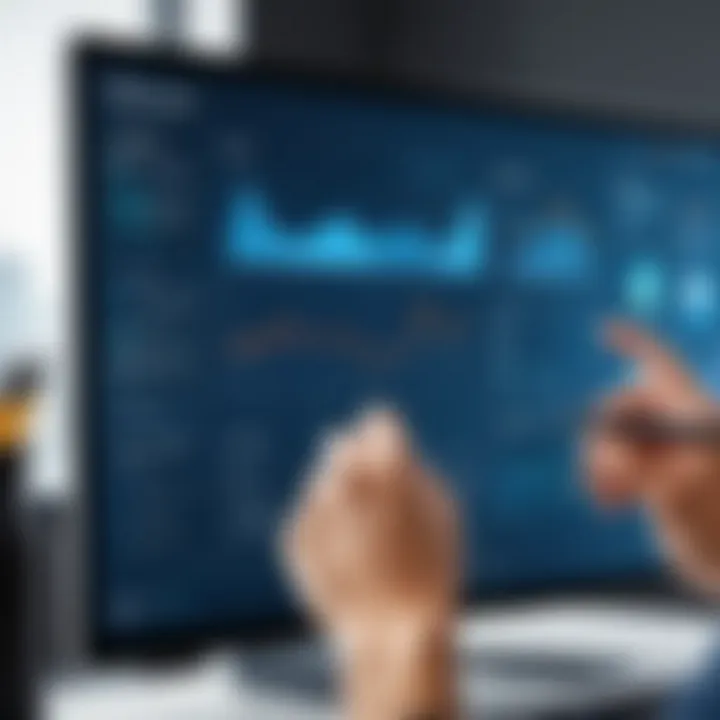
User Experience and Accessibility
User experience is the silent driver of acceptance. When systems are difficult to navigate, it’s like trying to swim against the tide—frustrating and unproductive. Here’s how you can ensure a user-friendly implementation:
- Interface Design: Look for intuitive interfaces that simplify the user's journey. It can make a world of difference, especially for those who may not be tech-savvy.
- Customization Options: Look for systems that allow tailoring to specific user roles which can enhance efficiency.
- Mobile Accessibility: In today’s mobile-driven world, having access to systems on-the-go is often a necessity. Solutions that offer mobile applications can greatly enhance productivity.
- Collaborative Features: Those that encourage team collaboration often see higher levels of adoption and satisfaction.
In the grand scheme of things, selecting a user-friendly tool management system will not only streamline operations but also minimize resistance from staff that may be apprehensive about change.
"The right system is like a good tool; it helps you create, not complicate."
As you approach the selection of a tool management system, keep these criteria at the forefront. It’s about finding a fit that not only meets present needs but also scales with you as your operations evolve.
Technological Impact on Tool Management Systems
In today's fast-paced industrial landscape, the role of technology in enhancing tool management systems cannot be overstated. The integration of advanced technological features into these systems has not only reshaped how tools are managed but also significantly improved operational efficiency and decision-making capabilities. This section explores three critical technological components—cloud-based solutions, mobile applications, and data analytics—while considering their specific benefits and applications in tool management.
Cloud-based Solutions
Cloud technology has revolutionized the approach to tool management by offering flexibility and accessibility that was previously unimaginable. Instead of being tethered to a physical location, users can access their tool management systems from anywhere, anytime. This change has paved the way for a whole new workflow paradigm.
- Scalability is one of the prime advantages. As businesses grow, their tool management needs evolve. Cloud platforms allow for easy scaling without the complex hardware upgrades associated with traditional systems.
- Cost-effectiveness also plays a crucial role, as organizations save on hardware expenses and maintenance. With the pay-as-you-go model, companies only pay for what they use.
- Data stored in the cloud is often more secure and backed up, reducing risks related to data loss.
With these benefits, various firms have shifted towards cloud-based solutions. Using a platform like Amazon Web Services or Microsoft Azure facilitates not only tool tracking but supports collaboration among team members in real-time.
Mobile Applications
The rise of mobile technology has made it easier for on-site personnel to manage tools effectively. Mobile applications have become essential, allowing immediate updates and communication regardless of location.
Key Features include:
- Real-time updates: Users can add, remove, or modify tool availability instantly, ensuring accurate inventories and reducing downtime.
- Barcode scanning: This feature simplifies tool checkouts and returns, making the tracking process seamless.
- Notifications and alerts: Tools that require maintenance or tools nearing their usage limits can send alerts directly to users’ phones, promoting proactive management.
Leveraging mobile platforms is distinctively beneficial for fields where employees are frequently on the move, like in construction or manufacturing, thus enhancing overall efficiency and productivity.
Data Analytics and Reporting
Data analytics is a game changer in the context of tool management systems. The ability to convert vast amounts of usage and maintenance data into actionable insights can inform decision-makers, allowing for optimized operations.
- Predictive maintenance stands out among the benefits, where patterns are analyzed to foresee tool failures before they happen. This approach minimizes disruptions and extends the lifespan of tools.
- Usage tracking and reporting enable companies to identify trends, ensuring that tools are not overused or underutilized. Establishing usage benchmarks helps in implementing better inventory management practices.
- Cost analysis tools within the analytics framework help companies monitor and control their budgets efficiently. By checking which tools incur the most costs, businesses can make informed decisions about divestment or replacement.
Implementation Strategies
Implementing a tool management system is not just about picking a solution from a catalog. It’s a multifaceted process that requires thoughtful planning and careful consideration. When organizations take time to lay the groundwork, the chances of success skyrocket. Automation, efficiency, and accuracy don’t just come from the system itself; they come from how well it’s implemented. This section delves into the essential strategies that underpin successful tool management system implementation.
Planning and Preparation
Just like assembling furniture from a flat-pack, the initial steps in implementation can make or break the project. Planning is not merely a formality; it’s the backbone of successful adoption. A well-laid plan addresses specific business needs and aligns them with the system’s capabilities. When a group of construction workers decided to streamline their tool usage, they first needed to benchmark their current situation. This could involve listing tools, figuring out where they’re stored, and understanding usage patterns.
In the preparation phase, consider creating a detailed outline that includes:
- Objectives of the implementation: Define what success looks like for your organization. Do you want to minimize lost tools or improve maintenance schedules?
- Stakeholders: Involve team members across various departments from the start. They can provide valuable insights and foster deeper acceptance of the new system.
- Timeframe and Milestones: Set a realistic timeline along with key milestones to track progress. Like a roadmap, this helps ensure everyone remains on the same page.
This stage sets the stage for a smoother transition, which leads us naturally to the next consideration: training and support.
Training and Support
Once the planning is all squared away, the real challenge often emerges: getting the team onboard. A state-of-the-art tool management system can fall flat if users don't know how to navigate it. It’s critical to present a comprehensive training program that’s tailored to the needs of various users.
Training should go beyond just ‘how-to’ sessions; it ought to embrace the underlying philosophy behind the tool management system. For example, a company could arrange workshops where employees learn not just to use the software but understand how it helps improve their daily tasks. Some potential training methods might include:
- Hands-on Workshops: These let users work directly with the system in a controlled setting, allowing real-time question-and-answer sessions.
- E-Learning Modules: For those unable to attend physical training, online platforms can offer flexibility.
- Continued Support: Assigning a mentor or a go-to support figure can alleviate fears regarding the new system.
"An organization is only as good as its weakest link, so investing in people means investing in your business's future."
Monitoring and Evaluation
After implementation, the work isn’t done. In fact, monitoring and evaluation are just as crucial as the earlier stages. Once the tool management system is live, it’s essential to ensure it functions as expected. This is where organizations can catch potential issues before they escalate.
Key points of focus during the evaluation phase include:
- Performance Metrics: Define clear indicators such as the number of lost tools, time saved on tool tracking, or enhanced user satisfaction.
- Feedback Loops: Establish mechanisms for ongoing feedback from users. Regular surveys or one-on-one conversations can provide insights into user satisfaction and potential areas for improvement.
- Adjustment Plans: Remain flexible. If something isn’t working as planned, be prepared to pivot. For instance, if workers find the software cumbersome, it might indicate a need for additional training or streamlining of processes.
Overall, effective implementation strategies aren’t just about deploying software. They encompass a series of deliberate decisions that pave the way for improved operational management, ultimately enhancing overall project efficiency. By taking a structured approach to planning, training, and monitoring, decision-makers can set their organizations up for long-term success.
Challenges in Tool Management System Adoption
Adopting a tool management system, while often seen as an advanced solution, can be filled with its own share of hurdles. The relevance of discussing challenges in adoption lies in culling those strings of resistance and concern that decision-makers frequently encounter. Understanding these challenges not only elucidates the complexities behind deploying these systems, but also frames the context for navigating pitfalls that could lead to significant operational disruption. Recognizing these challenges arms leaders with foresight. This means they're not just preparing for implementation, but also engendering a culture that embraces the change required for successful integration.
Resistance to Change
Resistance to change is perhaps the most commonly heard phrase in discussions surrounding any new system rollout. It emerges in different forms, from vocal dissent to passive avoidance. Employees, familiar with their routines, often feel threatened by new processes. This trepidation can lead to a lack of engagement and reluctance to adopt the new tool management system, reducing its potential effectiveness.
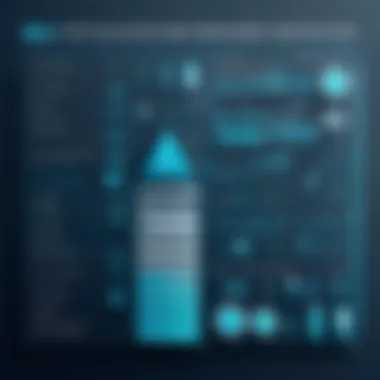
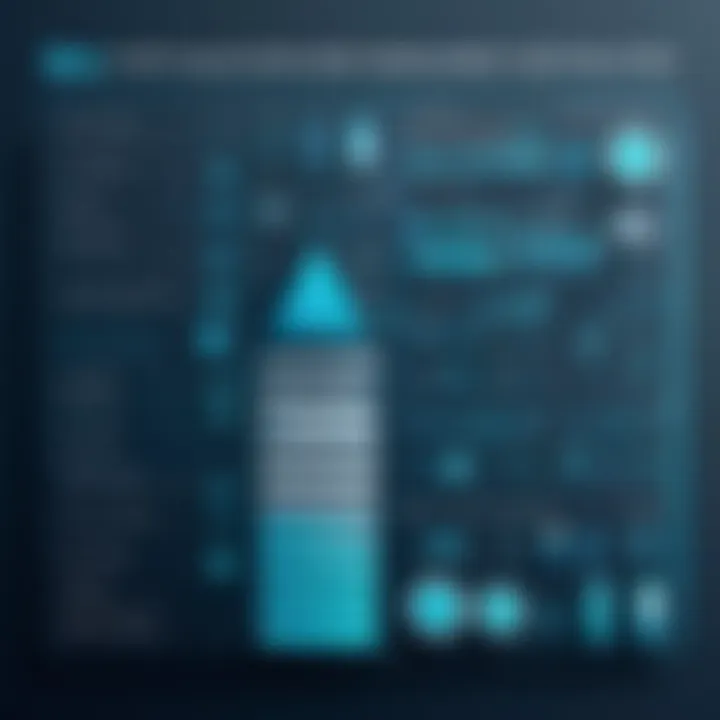
- Employees may believe the change is a menace to job security.
- Miscommunication regarding the goals of the new system could foster a sense of displacement, leading to friction among team members.
- The complexities of the system itself could engender doubt about its practical usability.
For successful adoption, leadership must engage staff early on. Open communication about the benefits and offering ample training sessions can mitigate resistance. By creating an inclusive environment where employees feel heard, their investing in the transition becomes more probable, paving a smoother path forward.
Integration with Existing Processes
When it comes to tool management systems, the root of the matter often lies in integrating these new systems with existing processes. Each organization has its own unique workflow intricacies, and any perceived disruption can cause significant worry. Integrating a new tool management system into operations means aligning it with current practices, which can be a daunting task.
- The learning curve attached to shifting from legacy systems can slow down productivity.
- Compatibility issues may arise if the new system doesn't seamlessly interact with existing software.
- Fractures can occur where there’s a disconnect, potentially leading to inconsistencies in data flow and reporting.
Organizations must methodically outline how their existing processes can accommodate the new system. Conducting a thorough assessment prior to implementation can unveil critical alignment needs, minimizing integration problems. All of this requires careful planning, along with the agility to adapt during the integration process.
Data Security Concerns
In this digital age, data security stands as a formidable concern in the realm of tool management systems. As data begins to flow from traditional warehouses to cloud-based environments, questions about security become paramount. With increasing incidents of breaches, organizations are rightfully wary.
- There can be fears about the vulnerability of sensitive information stored in new systems.
- Questions may arise concerning regulatory compliance—especially in industries that handle an influx of personal data.
- The misconception that new systems automatically ensure data security can lead to deadly complacency.
Drawing from best practices in cybersecurity is essential. Organizations can deploy multi-layered security protocols to safeguard data during the transition. Evaluating the security measures within the tool management system itself is crucial. After all, the essence of a tool management system isn’t merely to keep track of assets but also to protect valuable information against threats.
Case Studies and Real-World Applications
Exploring case studies and real-world applications sheds light on how tool management systems operate in practice, showcasing their effectiveness across various industries. This narrative isn't just about examples - it's a deep dive into the benefits of these tools, highlighting what's been successful and where improvements are needed. Through detailed case studies, stakeholders can glean insights that are not only relatable but also significant for decision-making processes in different business contexts.
Industry-specific Implementations
Different industries have their unique challenges when it comes to managing tools and resources. For instance, the construction sector heavily relies on tool management systems to keep track of equipment availability and maintenance schedules. In a case involving a mid-sized construction firm, they implemented a tool tracking system that integrated RFID technology. This allowed them to reduce tool loss by over 30%, as they could effectively monitor their assets in real time.
Similarly, in the manufacturing industry, a company producing automotive parts incorporated a cloud-based tool management system that facilitated better inventory control. They found that by employing data-driven decisions derived from their tool management system, they could optimize production downtime, ultimately boosting overall efficiency and significantly reducing costs.
Success Stories
Success stories illustrate the direct impact of adopting effective tool management systems. > "A good tool management system not only saves time; it can also transform the way a business operates." This statement rings true for a notable success story from an aerospace company that faced major setbacks due to inefficient tool management. After deploying a sophisticated management system, which included mobile access for personnel on the ground, they reported a 50% decrease in tool retrieval time. This swift transition allowed them to complete projects faster without compromising quality.
In another instance, a hospital adopted a tool management system to oversee surgical tools. The implementation led to an evident reduction in surgical delays caused by misplaced tools, ultimately enhancing patient care and operational flow. Patients benefited as surgeries were performed timely, maintaining a high standard of healthcare.
Lessons Learned
Every implementation teaches valuable lessons that can ease future transitions. A key takeaway from the case studies above is the significance of user training. Many organizations initially struggled because employees weren’t fully acquainted with new systems. A major takeaway from these experiences is that adequate training ensures users feel confident and competent in utilizing the system.
Another lesson stems from ongoing support. Continuous user feedback can lead to system improvements, which ultimately fosters a more productive work environment. For instance, one construction firm learned that it’s crucial to establish feedback loops after the system was put in place, allowing technicians to voice their suggestions for further tweaks.
By examining these case studies and learning from real-world applications, decision-makers can tailor their tool management strategies to fit their specific industry needs while driving home the importance of adopting effective management systems.
Future Trends in Tool Management Systems
The landscape of tool management systems is continually shifting, influenced by advancements in technology and the evolving needs of industries. Understanding these trends is crucial for decision-makers and IT professionals who aim to stay ahead of the curve. As we delve deeper into the future of tool management systems, we’ll cover pivotal advancements in AI and automation, sustainability considerations, and the changing role of integrations. Each of these elements plays a significant part in shaping effective tool management strategies, ultimately driving efficiency and innovation.
Advancements in AI and Automation
Artificial Intelligence and automation are no longer just buzzwords; they are becoming essential components of tool management systems. Businesses are leveraging AI to streamline operations and enhance decision-making processes. For instance, predictive maintenance powered by AI can foresee tool failures before they occur, saving companies substantial time and money.
Moreover, automation helps in inventory management. Automatic reordering systems can trigger purchases when stock levels dip below a certain threshold. This minimizes human error and ensures optimal tool availability without interruption. By utilizing AI-driven analytics, organizations can gather insights into tool usage patterns, which further aids in making informed decisions regarding which tools to invest in or retire.
"As technology evolves, so does the way we manage our tools. Embracing AI and automation is no longer an option, but a necessity."
Sustainability Considerations
The pressure for businesses to adopt sustainable practices has never been greater. Current trends indicate a growing focus on environmentally friendly methods of tool management. This involves not just the choice of equipment, but also the processes surrounding their use, maintenance, and disposal.
For example, firms are increasingly opting for energy-efficient tools and materials that reduce their overall carbon footprint. The integration of recycling programs within tool management systems can also ensure that end-of-life tools are disposed of responsibly, contributing to circular economy principles.
Furthermore, companies that prioritize sustainability in their tool management are often viewed more favorably by consumers and stakeholders alike. Thus, aligning tool management practices with sustainability goals not only benefits the environment but can also enhance a brand's reputation and market competitiveness.
Evolving Role of Integrations
The integration of various systems is changing how tool management is approached. As businesses strive for a more unified operational framework, the ability to connect tool management systems with other essential platforms becomes vital. For instance, integrating ERP (Enterprise Resource Planning) systems with tool management solutions allows for seamless data sharing and process synchronization.
This interconnectedness leads to improved visibility across the supply chain, making it easier to track tools, analyze performance metrics, and align inventory with demand. Furthermore, as the Internet of Things (IoT) becomes more prevalent, tools equipped with smart sensors can communicate their status in real time, feeding data back into the management systems. This kind of real-time integration is set to redefine how organizations monitor and maintain their tools, ultimately enhancing operational efficiency across the board.
The End
In wrapping up the discussion on tool management systems, it becomes clear that the implications of this subject are profound for industries across the board. Instead of merely serving as a means to an end, effective tool management fundamentally transforms operational capabilities, propelling businesses forward. The emphasis here is on understanding the nuances of individual systems and how they contribute to the larger organizational goals.
Recap of Key Insights
To summarize the essence of our exploration:
- Operational Efficiency: Tool management systems streamline workflows, minimizing time wasted on locating, tracking, and managing equipment.
- Cost Savings: By optimizing tool usage and inventory management, organizations significantly reduce costs related to purchases and maintenance.
- Safety and Compliance: These systems ensure compliance with safety standards, reducing risks related to equipment mishaps and ensuring a safer working environment.
- Technological Integration: Modern systems incorporate cloud solutions, mobile apps, and data analytics, enhancing the responsiveness and adaptability of tool management practices.
- Future Trends: As artificial intelligence and automation evolve, they will play critical roles in improving efficiency and decision-making within tool management systems. Achieving sustainability targets is becoming more vital too.
“In a world where tools are the silent partners in productivity, managing them effectively can pave the way for extraordinary outcomes.”
Final Recommendations for Advisors
For industry-specific advisors and decision-makers, consider the following actionable suggestions:
- Assess Unique Needs: Every organization possesses distinct characteristics. Understanding individual or sector-specific requirements is crucial for selecting an appropriate tool management system.
- Prioritize Usability: The best technology is often the easiest to use. Ensure that whichever solution chosen is accessible and comprehensible to all users, regardless of their technical background.
- Invest in Training: An ingenious system can fall flat without proper training. Advise organizations to invest in comprehensive training programs to facilitate the transition.
- Stay Informed on Trends: Keeping abreast of technological advancements and evolving practices in tool management will equip advisors with insights to recommend forward-thinking solutions.
- Encourage Feedback: Implementing feedback loops allows organizations to fine-tune their systems progressively, adapting to new challenges and ultimately enhancing operational effectiveness.
By integrating these insights and recommendations, decision-makers can navigate the multifaceted landscape of tool management systems, ensuring that their organizations not only adapt but thrive amid changing dynamics.