Essential Guide to Small Machine Shop Software
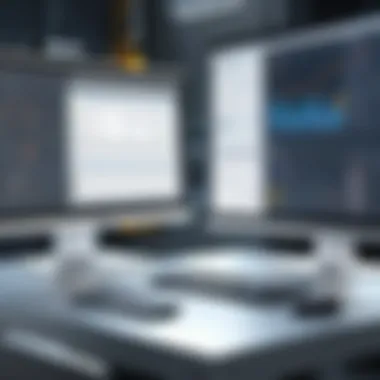
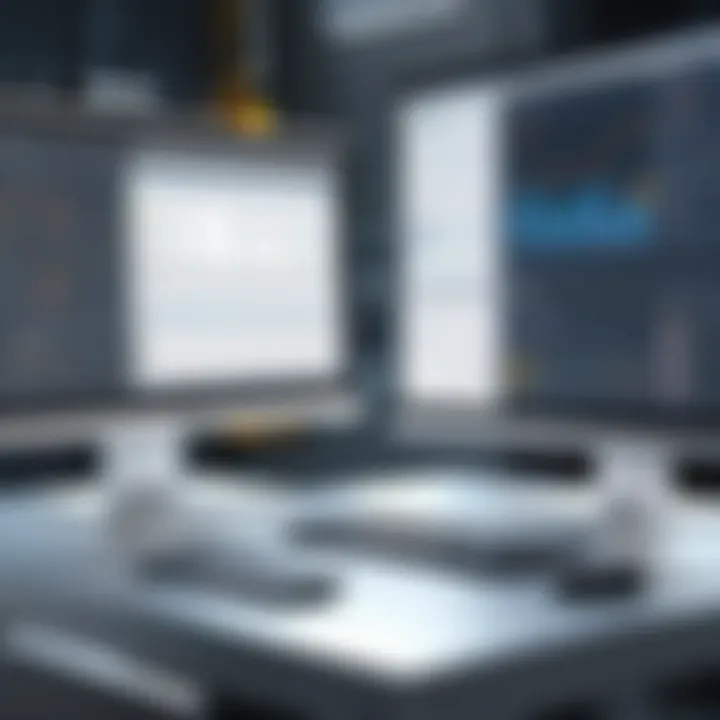
Intro
The landscape of manufacturing has evolved significantly over the past years. Small machine shops now face increased competition, and the need for operational efficiency has never been more pressing. Small machine shop software plays a crucial role in this environment by optimizing processes, tracking projects, and managing resources.
Understanding how to select the right software can transform operations, enhancing productivity and streamlining workflow. This article aims to delve into the essential features and functionalities of such software, while also addressing the challenges and benefits that come with adopting these technological solutions. The target audience includes decision-makers, IT professionals, and entrepreneurs who seek not only to navigate the software options available but also to make informed choices that align with their specific needs.
Software Overview
Brief Description of Software
Small machine shop software encompasses solutions designed to streamline operations in machining environments. These systems provide essential tools for managing inventory, scheduling jobs, and tracking customer orders. Many solutions provide a centralized platform that integrates various aspects of the shop's operations, from production planning to financial management.
Key Features and Functionalities
A well-rounded small machine shop software typically includes the following key features:
- Job Tracking: Monitor the progress of various jobs in real-time, ensuring deadlines are met.
- Inventory Management: Keep track of materials and components to avoid shortages or excess.
- Financial Reporting: Generate reports on income, expenses, and profitability.
- Customer Relationship Management (CRM): Manage interactions with customers, facilitating communication and follow-ups.
- Scheduling Tools: Plan and allocate resources efficiently, maximizing output.
These functionalities contribute to a more efficient workflow, thus allowing small machine shops to remain competitive in an ever-evolving market.
Detailed Comparison
Comparison with Competitors
When selecting small machine shop software, comparing various solutions is essential. Top providers such as JobBOSS, Fusion 360, and ProShop offer unique features that cater to different needs.
- JobBOSS excels in job tracking and quoting. It provides a user-friendly interface conducive to quick learning.
- Fusion 360 integrates advanced design capabilities, appealing to shops that engage in both design and manufacturing.
- ProShop notably emphasizes customer management, streamlining communication and service delivery.
Evaluating these options helps decision-makers identify the best fit for their specific operational goals.
Pricing Structure
Pricing for small machine shop software varies widely based on functionality and provider. It offers models including:
- Subscription-Based Pricing: Monthly or annual fees that provide ongoing updates and support.
- One-Time License Fee: A single payment for a perpetual license, but may require additional costs for updates.
Generally, software that offers comprehensive features tends to carry a higher price. However, the ROI through increased efficiency can justify these costs.
"Investing in the right small machine shop software is not just about functionality, but about enabling a shop to thrive in a competitive landscape."
Selecting small machine shop software should not be a rushed decision. It requires careful analysis of business needs, potential software capabilities, and ongoing costs. This ensures that the selected software will effectively enhance productivity and contribute to the overall success of the shop.
For further insights on manufacturing technology, consider visiting Wikipedia or Britannica.
By staying informed on industry trends and software capabilities, decision-makers can position their machine shops for greater success.
Prolusion to Small Machine Shop Software
In today's competitive landscape, small machine shops must adapt rapidly to changing demands and technological advancements. Small machine shop software plays a crucial role in ensuring these businesses remain efficient and profitable. It is essential for streamlining operations, managing resources effectively, and enhancing overall productivity. With precise software solutions, machine shops can better control their inventory, optimize production schedules, and accurately track costs, which ultimately leads to improved decision-making and business growth.
Definition and Purpose
Small machine shop software is designed specifically for businesses that provide machining services, often on a small to medium scale. The primary purpose of this software is to facilitate the planning, execution, and monitoring of various production processes. It integrates several functionalities, including manufacturing resource planning, inventory management, job costing, and quality control. By centralizing these operations within a single platform, the software eliminates inefficiencies that often arise when using disjointed systems. This results in a smoother workflow, reduced errors, and more accurate data collection.
Importance in the Manufacturing Sector
The manufacturing sector is arguably one of the most dynamic industries, where efficiency and accuracy are paramount. Small machine shop software addresses the unique challenges faced by smaller operations, such as limited resources and labor. Its importance is underscored by several factors:
- Efficiency: The software enables machine shops to streamline processes, leading to faster turnaround times and better utilization of machine tools.
- Cost Management: By providing accurate job costing and inventory tracking, businesses can identify and eliminate unnecessary expenses.
- Quality Assurance: Built-in quality control features help maintain the standards required by clients, which is crucial for retaining and attracting customers.
- Data-Driven Decisions: The software collects and analyzes data, offering insights that guide strategic decisions.
"Investing in the right software can transform not only processes but also the trajectory of a small machine shop's success."
Therefore, as small machine shops look to leverage their capabilities, understanding small machine shop software becomes critical in navigating the complexities of modern manufacturing.
Key Features of Small Machine Shop Software
Small machine shop software plays a crucial role in the modern manufacturing environment. Understanding its key features ensures that decision-makers can choose the right solution that meets their business needs. Significant features increase productivity, streamline operations, and enhance the overall efficiency of small machine shops. Each feature serves a distinct purpose and contributes to the effective management of resources and processes. The following sections will discuss these essential features in detail.
Manufacturing Resource Planning (MRP)
Manufacturing resource planning is the backbone of effective production management. MRP systems allow small machine shops to plan and manage manufacturing processes efficiently. They help in forecasting demand, scheduling production, and managing raw materials. A well-implemented MRP system leads to reduced waste and improved inventory turnover.
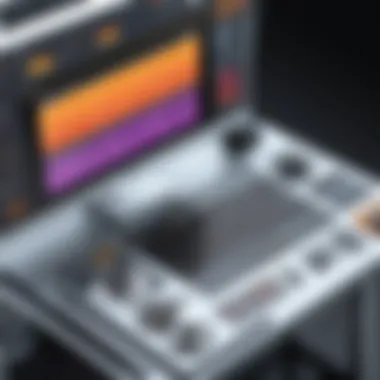
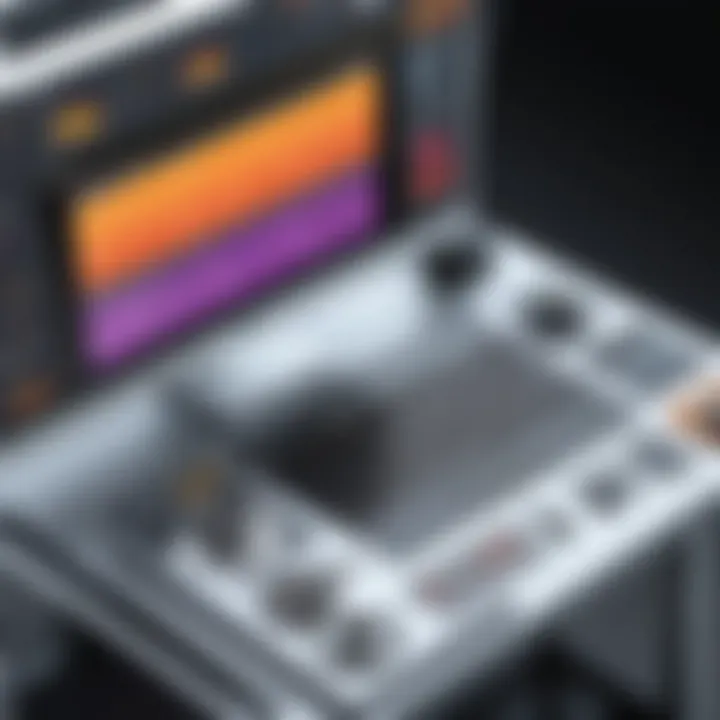
Key benefits of MRP include:
- Efficient resource allocation: It ensures that materials and labor are used optimally.
- Better inventory control: Visibly tracking inventory prevents overstocking or stockouts.
- Enhanced production schedules: MRP systems adapt quickly to changes in manufacturing schedules, which is crucial in keeping projects on track.
Inventory Management
Effective inventory management is vital for any small machine shop. This feature helps businesses maintain optimal stock levels, monitor inventory usage, and avoid obsolete materials. Good inventory management systems track real-time stock levels and usage patterns. This insight is essential in decision-making, ensuring that shops can respond swiftly to changes in demand.
Advantages of robust inventory management include:
- Cost savings: By avoiding excess inventory, shops can reduce holding costs.
- Improved order fulfillment: Accurate inventory tracking leads to faster turnaround times on orders.
- Data-driven decision making: Historical data helps predict future inventory needs, reducing uncertainty.
Job Costing
Job costing is an integral feature that details the expenses associated with each specific project. This function allows machine shops to analyze costs related to labor, materials, and overhead for each job. By understanding these costs, businesses can set competitive pricing and ensure profitability.
Benefits of job costing comprise:
- Transparency in project costs: Clear insights into expenses enable better financial planning.
- Accurate pricing: Helps in setting prices that cover costs and yield profits.
- Resource management: Knowing which jobs are profitable improves resource allocation for future projects.
Scheduling and Production Planning
Scheduling and production planning modules integrate workflows and ensure that all tasks are completed on time. This feature is key to maintaining an efficient production cycle. It allows managers to prioritize tasks, allocate resources effectively, and respond to delays without disruption.
Scheduling benefits include:
- Optimized workflows: Proper scheduling reduces bottlenecks in production, enhancing throughput.
- Adaptive planning: Capability to quickly adjust the production plan in response to real-time changes.
- Labor management: An organized schedule helps in efficient workforce management.
Quality Control Features
Quality control is critical in manufacturing, ensuring that products meet acceptable standards. Small machine shop software often includes tools for tracking quality throughout the production process. Quality control features help in identifying defects early, minimizing waste and rework.
Important aspects of quality control include:
- Consistency: Helps in maintaining product standards over time.
- Data analysis: Provides insights into quality trends, allowing for continuous improvements.
- Compliance: Ensures products meet industry standards, which is vital for customer satisfaction and regulatory requirements.
In summary, each of these key features—Manufacturing Resource Planning, Inventory Management, Job Costing, Scheduling, and Quality Control—combine to create a powerful toolkit for small machine shops. An understanding of these elements helps in selecting software that can transform operations and drive efficiency.
Benefits of Implementing Small Machine Shop Software
Implementing small machine shop software offers several significant advantages that impact productivity, cost management, and overall operational efficiency. For decision-makers and industry professionals, understanding these benefits is crucial in making informed choices regarding technology investments.
A well-chosen software solution can streamline processes, reduce waste, and enhance communication, leading to measurable improvements across the board.
Increased Efficiency
Small machine shops usually face the challenge of balancing multiple tasks with limited resources. Implementing effective software can drastically improve efficiency. This efficiency stems from automating routine operations, which allows employees to focus on more value-driven tasks. The software can optimize workflows by tracking project statuses, automating scheduling, and even predicting machine downtime.
By minimizing human error, the software reduces idle time and enhances workflow management. As tasks are automated, employees can maintain higher levels of productivity, which also contributes to meeting deadlines more reliably.
Cost Reduction
Cost management is essential for the sustainability of small machine shops. With the right software, many of the costs associated with manual tasks and inefficiencies can be minimized. This cost reduction occurs in several ways:
- Lower labor costs due to automation of routine tasks.
- Reduced material waste through optimized inventory management.
- Better forecasting that leads to fewer excess stock situations.
By analyzing costs in real time, managers can make informed decisions that directly impact the bottom line. Investing in a good software solution may appear daunting initially, but the longer-term savings often far outweigh those initial outlays.
Improved Accuracy
Precision is a critical requirement in the manufacturing sector. The risk of errors in job costing, scheduling, or inventory tracking can have disastrous consequences. Small machine shop software enhances accuracy by providing a reliable framework for tracking data and generating reports.
For example, with features such as barcode scanning and parts tracking, human errors that occur during data entry can be significantly decreased. This improved accuracy allows for better decision-making, enhancing output quality and customer satisfaction. In an industry where quality is paramount, such accuracy can set a business apart from competitors.
Real-time Data Accessibility
Real-time data access is another key benefit of small machine shop software. Having immediate access to pertinent information can empower teams to make better strategic decisions. Decision-makers can track performance metrics, costs, and job statuses at any point in time without delay.
This accessibility not only facilitates quicker decision-making but also helps teams respond more effectively to unexpected challenges. With fast access to updated data, managers can implement changes on-the-fly, reducing downtime and increasing overall responsiveness.
"Real-time data is no longer a luxury; it is a necessity for effective operation in modern manufacturing."

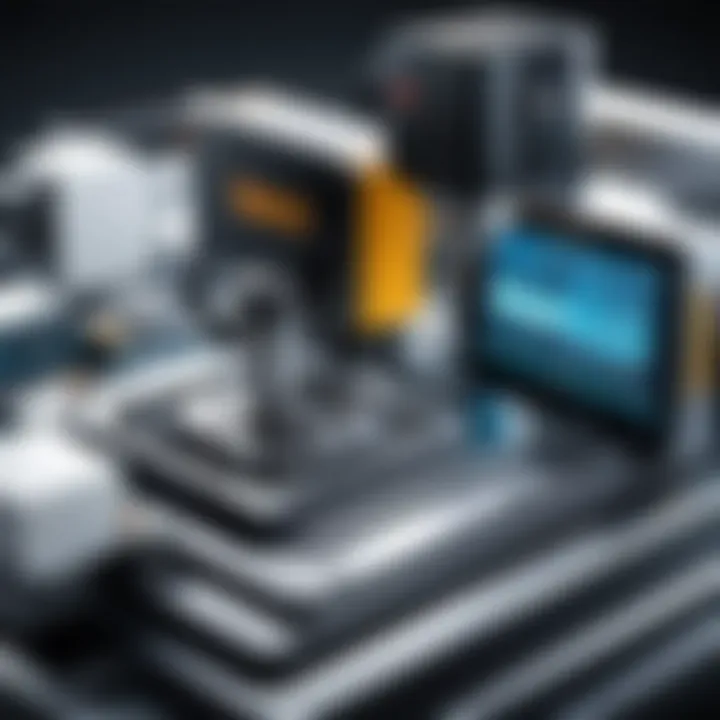
In summary, the benefits of implementing small machine shop software span increased efficiency, cost reduction, improved accuracy, and real-time data accessibility. Recognizing these factors provides a comprehensive understanding of how such software can transform operational processes, leading to enhanced profitability and competitiveness in the market.
Challenges in Selecting Appropriate Software
Selecting the right software for a small machine shop is not a straightforward task. The landscape of available solutions is vast and varied, making it crucial to identify what works best for a particular business's needs. Each small machine shop has unique processing capabilities, product lines, and operational requirements. Therefore, understanding the challenges involved in selecting appropriate software is essential for achieving the desired efficiency and productivity.
Customization Versus Off-The-Shelf Solutions
When choosing software, one key challenge is deciding between customization and off-the-shelf solutions.
- Customization allows the business to tailor the software to specific needs. This approach can lead to a perfect fit for unique processes. However, customized solutions can be costly and time-consuming to implement. They may also require ongoing maintenance, which can strain resources.
- Off-the-shelf solutions, on the other hand, are ready-made and can be implemented quickly. They may offer ample functionality for common manufacturing processes. Yet, these solutions can also lack flexibility. They might not cater well to specialized requirements, forcing adjustments to existing workflows.
A thorough evaluation of the shop's specific needs is critical. Businesses must weigh their readiness to invest in customization against the immediate benefits of off-the-shelf options.
Understanding User Requirements
Another significant challenge is understanding user requirements. This involves more than just gathering a list of desired features; it requires a comprehensive analysis of how users interact with existing processes and what improvements they seek.
Misunderstanding these requirements can lead to misunderstanding tool capabilities. For example, an emphasis on certain features like inventory management might overshadow more critical needs like job costing or scheduling.
It's advisable to involve team members from various departments during the needs assessment. This collaboration ensures that the selected software can cater to everyone, from shop floor operatives to management. Gathering feedback through surveys or interviews can also provide insight into functionalities that might not be immediately apparent.
Integration with Existing Systems
Integration with existing systems presents another layer of complexity in selecting software. Most small machine shops use various systems for operations, including accounting software and project management tools.
The new software must seamlessly connect with these systems to avoid data silos. A lack of integration often leads to operational inefficiencies, additional manual work, or even errors in data entry. Therefore, it is crucial to assess how well potential solutions will integrate with existing software.
- Questions to consider include:
- Will the software support data import/export?
- Can it connect with existing platforms via APIs (Application Programming Interfaces)?
- What level of technical support is offered for integration?
By addressing these aspects, business leaders can ensure smoother operations and higher productivity when transitioning to new software.
Selecting suitable software can lead to significant operational efficiencies, but failing to recognize these challenges may result in costly missteps.
Emerging Trends in Small Machine Shop Software
In recent years, the evolution of small machine shop software has become crucial for maintaining competitiveness in the manufacturing sector. The right software can simplify processes and enhance response times to market demands. Understanding emerging trends in this area helps decision-makers anticipate changes and prepares them to harness upcoming technologies effectively.
Cloud-Based Solutions
Cloud-based solutions represent a substantial shift in how software is deployed and managed. These platforms allow machine shops to access their software from anywhere with an internet connection. Rather than being confined to on-premises servers, cloud solutions offer greater flexibility and scalability. This becomes particularly important as machine shops expand operations or adjust production volumes.
Benefits of cloud-based solutions include:
- Cost-Effectiveness: Reduced need for extensive hardware investment leads to lower initial costs.
- Scalability: Businesses can easily upgrade their usage levels based on changing operational needs.
- Automatic Updates: Maintaining up-to-date software is seamless, as updates are managed by the service provider.
- Improved Collaboration: Teams can share information more easily, enhancing collaboration and productivity.
Automation and AI Integration
The introduction of automation and artificial intelligence (AI) in small machine shop software marks a transformative shift. Automation can handle repetitive tasks, allowing employees to focus on higher-value work. Integration of AI provides insights through data analysis that was previously unachievable.
Key features of automation and AI integration include:
- Data-Driven Decision Making: AI tools analyze operational data, helping managers make informed decisions.
- Predictive Maintenance: AI predicts potential equipment failures, which helps reduce downtime.
- Optimization of Production Processes: Automation adjusts operations based on real-time data, enhancing efficiency.
"Incorporating AI solutions enhances accuracy in forecasting, delivering substantial improvements in planning and productivity."
Mobile Accessibility
Mobile accessibility is becoming increasingly valuable as the workforce becomes more mobile. Small machine shop software that offers mobile functionality allows operators to monitor operations and make decisions from their mobile devices. This ability improves response times and allows for increased agility in production environments.
Considerations for mobile accessibility include:
- Remote Monitoring: Operators can track job progress and inventory levels in real time.
- Enhanced Communication: Teams can collaborate without being tied to a single location.
- User-Friendly Interfaces: Software designed for mobile use must be intuitive to ensure quick adoption.
Case Studies of Successful Implementations
Case studies offer concrete examples of how small machine shop software can impact operations in real environments. They allow decision-makers to see the practical benefits and challenges associated with software implementation. By examining case studies, businesses can gain insights into the processes involved, the decisions made, and the outcomes achieved. This understanding is essential for stakeholders to assess which software solutions align best with their specific needs and objectives. Moreover, these studies inform potential pitfalls to avoid, making the exploration of real-world applications invaluable.
Case Study One: Before and After Analysis
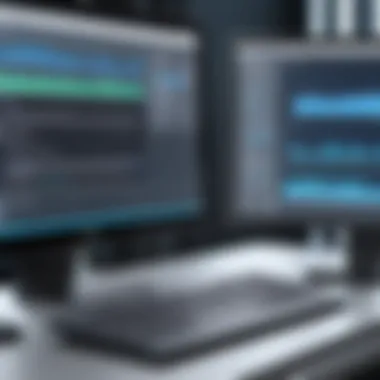
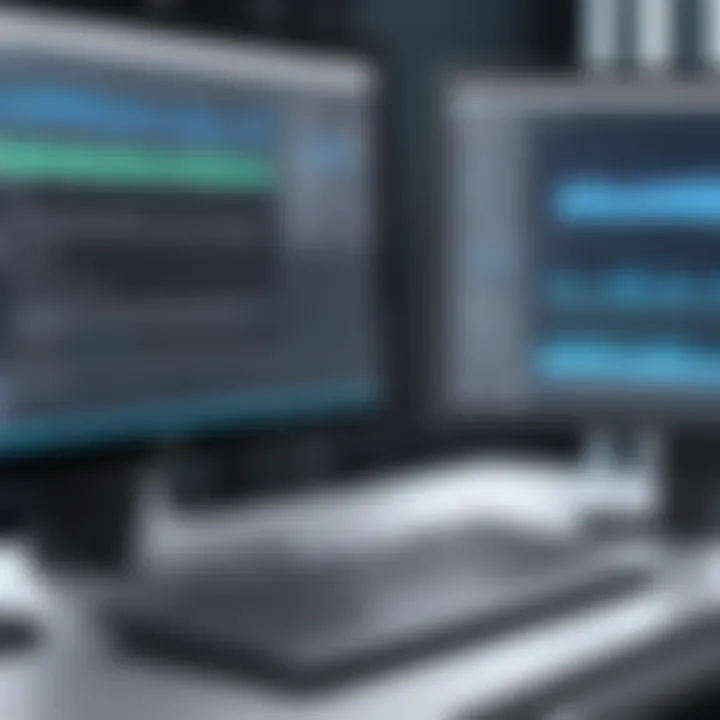
This case study focuses on a small machine shop that implemented the Fusion 360 software. Initially, the shop relied on manual methods for design and production management, leading to errors and inefficiencies. The workflow was fragmented, which caused delays in order fulfillment. After the implementation, the shop reported significant improvements. The software integrated design, machining, and project management in one platform.
Key improvements noted include:
- Increased Productivity: Production times decreased by 30%.
- Error Reduction: Mistakes in design were reduced by 50%.
- Enhanced Communication: Team members were able to collaborate in real time, improving overall project coordination.
The transformation was not instantaneous. Some challenges arose during the transition phase, such as training staff and adapting to the new system. However, robust training programs facilitated a smoother transition and helped staff become proficient with the software quickly.
Case Study Two: Overcoming Implementation Challenges
This study examines a machine shop that faced several roadblocks while adopting the JobBOSS software. Initially, the management underestimated the complexity of integrating new software with existing systems. This oversight led to delays and increased costs. However, the team employed strategic solutions to navigate these challenges.
Key Strategies Utilized:
- Comprehensive Needs Assessment: Engaging with employees across departments helped identify specific requirements.
- Incremental Integration: Instead of a full system overhaul, the approach was to integrate components gradually, testing each module thoroughly.
- Continual Support and Training: Ongoing support was established, which helped reduce resistance to change among staff.
As a result, the shop improved its operational efficiency by 25% and achieved greater real-time data utilization. Their ability to adapt the software to meet their needs ultimately resulted in a successful implementation that set a precedent for future technology adoption.
"Real-world implementation case studies provide invaluable lessons and strategies for overcoming obstacles in software integration."
These case studies illustrate that while the journey to adopting small machine shop software can be fraught with challenges, the rewards often outweigh the initial difficulties. The careful selection of solutions and the willingness to adapt are crucial elements for success in this process.
Best Practices for Software Implementation
Implementing software in a small machine shop is a pivotal step towards modernizing operations and enhancing efficiency. Adopting best practices can significantly influence the success of this transition. Therefore, it becomes crucial for decision-makers to recognize the importance of structured implementation approaches that align with their business needs and operational goals.
Assessment of Business Needs
Before introducing new software, it is essential to conduct a thorough assessment of the business needs. This step involves understanding the specific challenges faced by the shop, such as inefficient workflow, inventory management issues, or difficulty in job costing.
Key actions include:
Clearly identifying operational bottlenecks.
- Evaluating existing software capabilities.
- Gathering input from staff on functionality gaps.
By comprehensively assessing these needs, businesses can determine what features are vital in the software. This foundational step often dictates the overall effectiveness of the chosen system.
Phased Rollout Strategies
Implementing software can be overwhelming if approached haphazardly. A phased rollout strategy mitigates risks and allows for smoother transitions. By breaking down the implementation process into manageable stages, machine shops can reduce disruptions to daily operations.
This strategy involves:
- Pilot Testing: Begin with a small group that uses the software and provides feedback.
- Gradual Integration: Scale up by adding users systematically. This allows for making necessary adjustments based on feedback.
- Continuous Evaluation: Regularly assess the system's performance and address any issues immediately.
A phased approach helps ensure that the workforce becomes accustomed to the new system gradually. This reduces the likelihood of resistance and enhances user engagement.
Training and Support for Staff
Training should not be an afterthought; it plays a critical role in the successful implementation of software. Providing comprehensive training enables staff to maximize the capabilities of the new system. It's also vital for building confidence in using the software effectively.
Training should include:
- Hands-on sessions for users to practice with the software.
- User manuals and documentation for reference.
- Ongoing support channels for addressing questions or concerns.
Investing time in training pays off. A well-trained staff is likely to adapt quickly, leading to increased productivity and reduced frustration.* Proper support ensures continuous improvement and alignment with operational goals.*
The Future of Small Machine Shop Software
As the manufacturing landscape continues to evolve, the role of small machine shop software becomes increasingly significant. This section discusses not only current trends but also anticipates future developments that could reshape the industry. For decision-makers and IT professionals, staying informed about these changes is essential for strategic planning.
Predictions for the Next Decade
Several key predictions can be made for the future of small machine shop software over the next ten years.
- Increased Dependence on Cloud Technology: Cloud solutions will become the norm, offering greater flexibility and scalability. Manufacturing firms will likely leverage these platforms to improve collaboration and data accessibility.
- Artificial Intelligence and Machine Learning: These technologies will find a broader application, paving the way for predictive analytics in production planning and inventory management. The shift will enable businesses to operate proactively rather than reactively.
- Enhanced Customization Options: Future software will offer more tailored solutions, addressing specific vendor requirements and shop-level intricacies.
- Real-time Data Integration: As IoT devices proliferate, integrating real-time data from machinery will become essential. This capability will help optimize workflows and enhance decision-making processes.
- Cybersecurity Enhancements: With increased digital reliance, robust cybersecurity measures will be paramount. Machine shops will need to prioritize protecting sensitive data from cyber threats.
Potential Disruptive Technologies
Considering the trajectory of small machine shop software, several disruptive technologies could emerge:
- Blockchain: This could increase transparency and security in supply chain management, offering a reliable way to track component origins and transactions.
- Augmented Reality (AR): AR may find applications in training and maintenance, allowing staff to visualize complex tasks over machinery in real time.
- Advanced Robotics: The evolution of robotics may lead to even more automated solutions, decreasing labor costs and allowing shops to focus on more skilled tasks.
"The future is not something we enter. The future is something we create."
This quote underlines the importance of proactive engagement with emerging technologies to shape the future landscape of manufacturing.
To conclude this section, it is evident that the small machine shop software of the future will heavily rely on technological advancements. Decision-makers need to be vigilant in their strategic planning to not only adapt but also thrive amid these changes.