Exploring MRP Systems in Manufacturing Efficiency
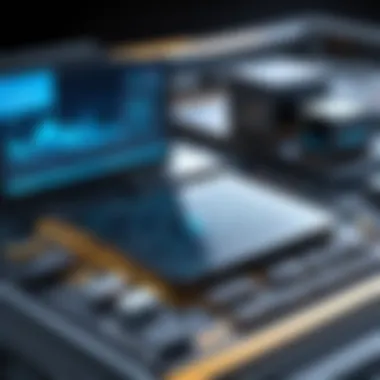
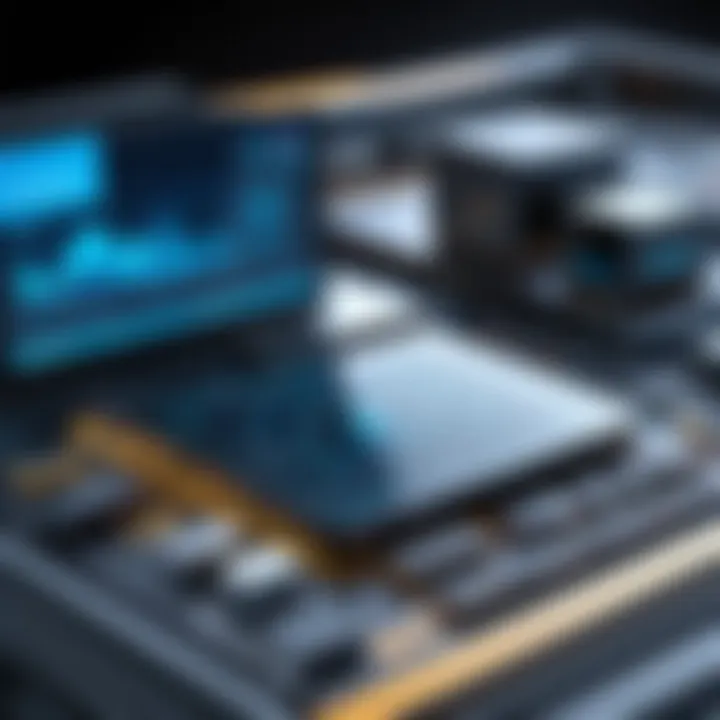
Intro
Material Requirements Planning (MRP) systems have become a cornerstone in the manufacturing sector, guiding production and inventory management with a focus on efficiency and effectiveness. As industries face increasing competitive pressures and complex supply chains, understanding MRP systems is crucial for decision-makers and IT professionals. This article aims to unravel the intricacies of MRP, from its fundamental principles to modern advancements, and highlight its relevance in optimizing both production processes and supply chain management.
In this comprehensive exploration, we will discuss the core components of MRP systems, their types, implementation challenges, and the benefits they bring to businesses. By gaining insights into MRP systems, industry-specific advisors will be equipped with the necessary knowledge to recommend the most suitable solutions for their clients, ultimately leading to enhanced operational effectiveness and strategic advantage in an increasingly volatile market.
As we advance through this narrative, readers will gain a clear understanding of how MRP systems work and the significance of these tools in achieving manufacturing success.
Preface to MRP Systems
In the realm of manufacturing, understanding Material Requirements Planning (MRP) systems is crucial. These systems serve as a backbone for many manufacturing processes. They are designed to manage materials, scheduling, and inventory, ensuring that production runs smoothly and efficiently. This introduction sets the stage for exploring the multifaceted nature of MRP systems, highlighting their importance in modern manufacturing environments.
Definition of MRP Systems
Material Requirements Planning is a production planning, scheduling, and inventory control system. It primarily aims to ensure that materials are available for production and products are available for delivery to customers. At its core, MRP focuses on the right quantity of materials at the right time. This minimizes waste and ensures optimal utilization of resources. It functions by using data from a bill of materials, inventory status, and the master production schedule, converting these inputs into actionable insights.
Greater efficiency is attained through careful planning. MRP helps businesses manage their supply chain effectively by forecasting demand and aligning production schedules accordingly. This accuracy in planning translates into less downtime, reduced holding costs, and better customer satisfaction. With MRP, companies can gain a tighter grip on their operations.
Historical Context
The origins of MRP systems can be traced back to the 1960s when manufacturers sought more sophisticated ways to manage their production processes. The first wave of MRP was simple; it focused primarily on material management. The 1970s saw the evolution into MRP II, which integrated additional aspects such as capacity planning and shop floor control. This shift laid the foundation for contemporary systems, which now emphasize integrated solutions that encompass resources beyond mere materials.
As industries continued to develop, MRP systems expanded their capabilities. These advancements now include features like demand forecasting and analysis, allowing businesses to adapt to trends in the market quickly and reliably.
MRP systems have progressively aligned with technological advancements, shifting towards software solutions as computing power increased. Today, many MRP systems are integral components of larger Enterprise Resource Planning (ERP) frameworks. This evolution signifies that organizations can no longer afford to dismiss the strategic role of MRP in their manufacturing processes.
By examining MRP systems through this dual lens of definition and historical context, we can better appreciate their valuable contribution to manufacturing efficiency. The following sections will delve deeper into the significance of MRP in manufacturing, exploring its key components and types.
The Importance of MRP in Manufacturing
Material Requirements Planning (MRP) systems are critical in the manufacturing landscape. Their significance lies in their ability to optimize production processes, enhance efficiency, and control costs. MRP provides a framework through which companies can manage resources, ensuring that materials are available for production and products are delivered to customers on time. This section breaks down the importance of MRP into several key areas.
Enhancing Production Efficiency
Production efficiency is a primary goal for manufacturing firms. MRP systems tie together various elements of production, from raw materials to delivery schedules. By meticulously planning material requirements, firms can reduce delays caused by the unavailability of materials. This directly impacts production cycles and leads to a more streamlined manufacturing process.
Benefits of MRP in enhancing production efficiency include:
- Synchronized manufacturing processes: MRP allows for better alignment across various production stages. When material needs are planned accurately, every department works in harmony.
- Improved lead times: With precise scheduling, lead times decrease. Companies can respond faster to customer demands without juggling inventory levels.
- Waste reduction: By forecasting demand and aligning production schedules accordingly, MRP minimizes excess production and inventory costs.
The efficiency gained does not just save time; it also contributes to a healthier profit margin. Increased efficiency means reduced labor and overhead costs, crucial for maintaining competitive pricing in the market.
Cost Control and Resource Allocation
Effective cost control is essential, especially in an industry where margins can be tight. MRP systems provide a disciplined approach to managing both direct costs and indirect costs associated with production.
Key aspects of cost control through MRP include:
- Accurate demand forecasting: By analyzing data, MRP systems can project future material requirements. This helps avoid the pitfalls of overordering, which ties up cash flow and storage resources.
- Tailored resource allocation: By tracking inventory levels in real-time, MRP enables companies to allocate resources more effectively. This ensures that materials are used efficiently and aligned with production needs.
- Cost analysis: Historical data integrated within MRP systems allows firms to assess performance over time. This data is invaluable for budgeting and allows companies to identify areas where costs can be reduced.
Implementing MRP systems does incur initial setup and operational costs. However, the reduction in waste and improved resource allocation typically offsets these costs over time.
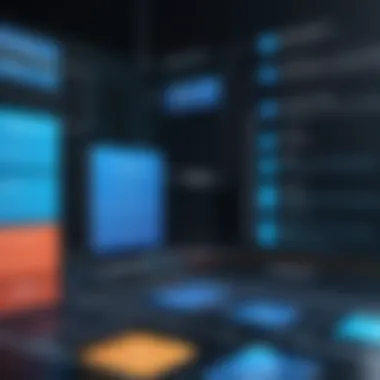
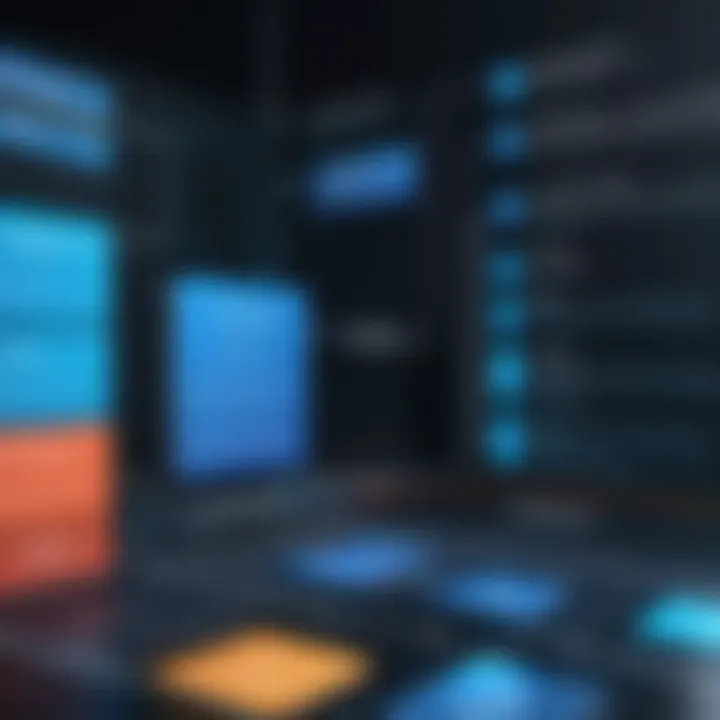
โIn the complex world of manufacturing, MRP systems serve as a backbone. They guide decision-makers by turning data into actionable intelligence.โ
The discussion about the importance of MRP systems highlights their role in enhancing productivity and ensuring cost control. The following sections will now delve into the key components of these systems, explicating how each function contributes to the broader organizational goals.
Key Components of MRP Systems
Understanding the key components of Material Requirements Planning (MRP) systems is crucial for effective manufacturing management. These components serve as the backbone of MRP systems, providing structure and clarity in production processes. By focusing on the essential elements, businesses can improve efficiency, reduce waste, and synchronize resources.
Bill of Materials (BOM)
The Bill of Materials, often referred to as BOM, is a comprehensive list that details all the raw materials, components, and sub-assemblies needed to produce a finished product. It functions as a vital blueprint in the production process. Accurate BOM documentation is necessary for proper inventory management and effective production scheduling. Some benefits of a well-structured BOM include:
- Provides clarity in material requirements.
- Facilitates communication between departments.
- Helps avoid overstocking or stockouts.
Creating a BOM requires attention to detail. It must include quantities, specifications, and appropriate units of measure. Any errors in the BOM can lead to production delays and increased costs. Thus, maintaining accuracy and updating the BOM as product designs change is critical.
Master Production Schedule (MPS)
The Master Production Schedule, or MPS, outlines when and how much of each product a company intends to manufacture during a specific period. It plays a pivotal role in aligning production activities with demand. The MPS is essential for the following reasons:
- Ensures production aligns with customer orders.
- Helps allocate resources appropriately.
- Aids in determining labor and equipment needs.
The MPS must be both realistic and flexible to adjust to changing market demands and unforeseen circumstances. A robust MPS enhances overall operational performance and leads to better customer satisfaction. Regular reviews of the MPS allow for adjustments based on real-time data and forecasting.
Inventory Management
Effective inventory management is integral to the success of any manufacturing operation. In the context of an MRP system, inventory management focuses on overseeing the ordering, storing, and utilization of materials. Efficient inventory management can bring several advantages:
- Reduces carrying costs of excess inventory.
- Minimizes waste due to obsolescence.
- Improves cash flow by optimizing stock levels.
Employing a systematic approach to inventory management allows manufacturers to maintain optimal stock levels while meeting production schedules. Techniques such as Just-In-Time (JIT) and ABC analysis can be employed to enhance inventory control. Consistent monitoring and forecasting help to manage fluctuations in supply and demand, ensuring a smooth production process.
Navigating these components requires a firm understanding of their roles and the relationships between them. Only then can manufacturing operations achieve their full potential.
Types of MRP Systems
Understanding the different types of MRP systems is crucial for organizations aiming to optimize their manufacturing processes. Each type serves distinct purposes and offers various benefits, making it essential for decision-makers to select the most suitable system for their needs.
MRP
MRP I, or Material Requirements Planning, is one of the simplest forms of MRP systems. It primarily focuses on inventory management and scheduling production. The core function of MRP I is to ensure that materials are available for production at the right time, thus preventing production delays. This system relies heavily on information derived from the Bill of Materials (BOM) and Master Production Schedule (MPS).
The benefits of MRP I include:
- Improved Inventory Management: By providing accurate forecasts for material requirements, MRP I reduces excess inventory and minimizes shortages.
- Reduced Lead Times: The streamlined process of scheduling and inventory availability can shorten lead times.
- Enhanced Visibility: It offers a clearer view of the supply chain, assisting managers in making informed decisions.
However, MRP I has limitations. It lacks the integrated functionalities needed for broader operational management, which leads many organizations to explore more sophisticated systems.
MRP
MRP II, or Manufacturing Resource Planning, expands upon the foundation set by MRP I. This system integrates additional functionalities like financial management and labor tracking into the planning process. MRP II provides a comprehensive view of a company's resources, covering not just materials but also capacity and manpower.
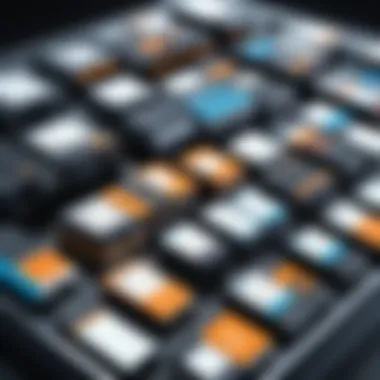
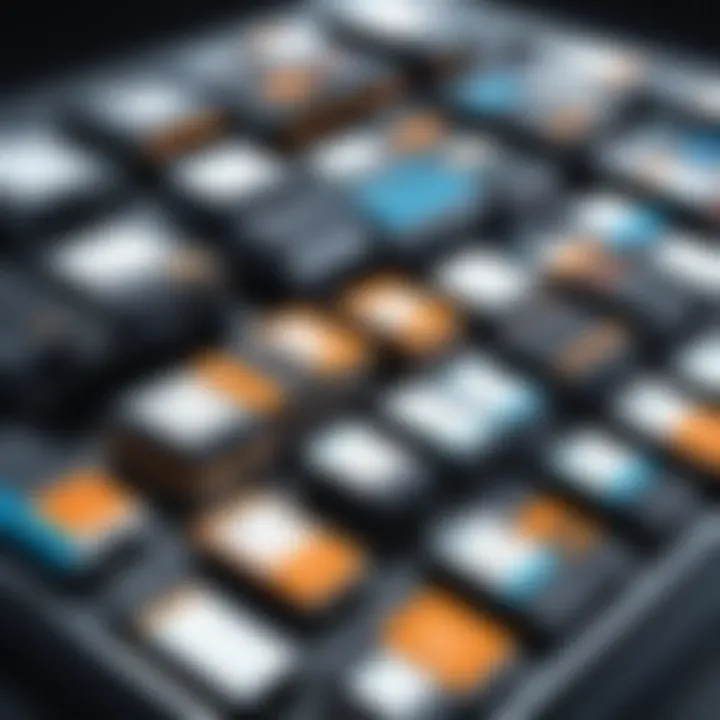
Key considerations for implementing MRP II include:
- Holistic Resource Management: MRP II enables companies to optimize all of their resources, not just materials. This includes machine utilization and workforce allocation.
- Increased Flexibility: It can adapt to changes in manufacturing processes and structures, providing businesses the flexibility to respond to new challenges.
- Integrated Planning: The interconnected nature of MRP II allows for more coordinated actions across departments, enhancing overall efficiency.
Despite its advantages, MRP II requires substantial investment for implementation and training, as well as ongoing maintenance. Organizations must weigh these costs against the benefits.
Enterprise Resource Planning (ERP)
Enterprise Resource Planning systems represent the next level of growth from both MRP I and MRP II. ERP systems consolidate multiple business functions into a single integrated system, which not only includes MRP but also finance, human resources, and supply chain management. This integration ensures all departments operate from the same data sets, promoting efficiency and accuracy.
Benefits of ERP systems feature:
- Real-Time Data Access: Decision-makers have access to real-time data across the organization, facilitating informed action.
- Streamlined Processes: By integrating various departments, ERP systems simplify processes and reduce redundancies.
- Improved Collaboration: Cross-department collaboration is promoted as all teams work within the same framework.
However, ERP implementations can be complex and time-consuming. Expenses associated with ERP, including software costs and staff training, can be significant. Companies should engage in thorough planning and assessment before adoption.
"Investing in the right MRP system can be a game-changer in optimizing manufacturing efficiency."
In summary, the types of MRP systemsโMRP I, MRP II, and ERPโeach cater to different organizational needs. A well-informed choice can result in more effective resource management, improved production planning, and enhanced operational efficiencies.
Implementing MRP Systems
Implementing MRP systems effectively is crucial for manufacturing organizations striving for optimal production efficiency and resource management. A well-thought-out implementation process can help a company overcome common operational challenges and position it for future growth. The following sections will elaborate on why careful planning and execution of MRP system implementation is necessary.
Assessment of Business Needs
To begin the implementation of an MRP system, it is essential for organizations to understand their specific business needs. A comprehensive assessment can help to identify gaps in current processes and clarify objectives.
- Identifying Requirements: Assessing needs involves gathering insights from various departments, such as production, inventory, and sales. Each department has unique requirements that contribute to the overall functionality.
- Setting Clear Goals: Organizations must set clear, measurable goals for the MRP system. This can include reducing lead times, improving inventory accuracy, or enhancing production scheduling.
- Evaluating Existing Systems: A critical step is to analyze existing systems and processes. Understanding what works and what doesn't provides a foundation for determining necessary improvements.
By taking the time to evaluate business needs thoroughly, companies can tailor their MRP system to meet their unique challenges while optimizing resources effectively.
Choosing the Right MRP Software
The software selection process is an integral part of MRP system implementation. Not all MRP solutions are created equal, and aligning software capabilities with organizational needs ensures effective implementation.
- Understanding Features: Organizations should look for specific features that align with their goals. Key functionalities may include advanced forecasting, real-time inventory tracking, and robust reporting tools.
- Scalability: Choosing a scalable solution is essential. As businesses grow, their needs change. The selected software should adapt to these changes without requiring a complete overhaul.
- User Experience: A user-friendly interface simplifies training and can enhance user adoption. Employees must feel comfortable navigating the system to fully exploit its capabilities.
- Vendor Support: Evaluate the level of customer support and training offered by the software provider. A reliable vendor can significantly enhance the implementation process and provide ongoing assistance.
By thoughtfully choosing the right MRP software, organizations can lay the groundwork for a successful implementation that aligns with their operational objectives.
Training and Support
Once the MRP system is selected, proper training and ongoing support are vital. Effective training ensures that all users are capable of leveraging the new system.
- Comprehensive Training Programs: Develop a structured training program that addresses the needs of different user roles within the organization. This program should cover not only basic functions but also advanced features of the MRP system.
- Workshops and Hands-On Sessions: Real-world practice can solidify learning. Conducting hands-on workshops allows employees to interact with the system under guidance and build confidence before going live.
- Establish Support Channels: Post-implementation support is an essential aspect as users encounter challenges. Organizations should set up support channels, such as a helpdesk or user forums, to address user inquiries and concerns.
- Continuous Learning: As software evolves, ongoing training sessions should be scheduled. Keeping users updated about new features or best practices can ensure that they are continually improving efficiency.
Implementing robust training and support mechanisms helps to maximize the benefits of the MRP system, facilitating a smoother transition and promoting long-term success in managing manufacturing processes.
"Proper implementation of MRP systems is a journey that begins with understanding the business's unique needs and ends with capable users driving efficiency in manufacturing."
Challenges in MRP System Implementation
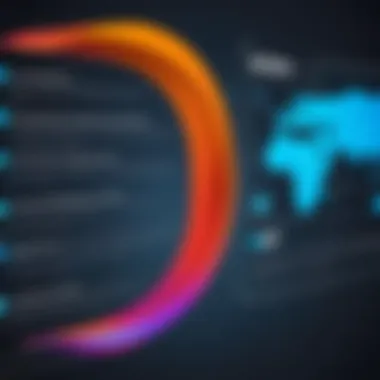
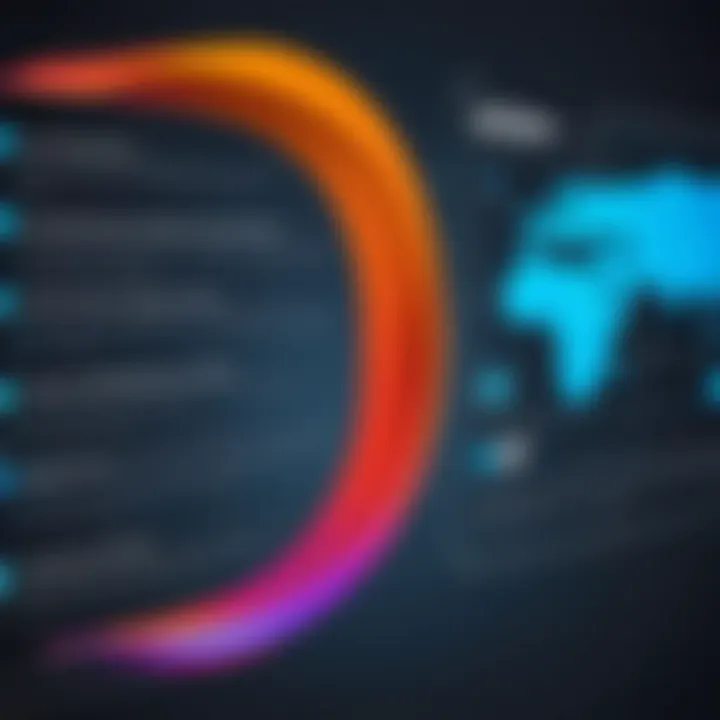
The implementation of Material Requirements Planning (MRP) systems is a critical undertaking for manufacturing organizations. While MRP systems can significantly enhance efficiency and productivity, their implementation is fraught with challenges. Recognizing and addressing these challenges is essential for a successful implementation. Organizations must navigate complexities related to data accuracy, user roles, and costs involved. Each of these areas presents unique considerations that can affect the overall effectiveness of an MRP system.
Data Integrity and Accuracy
Data integrity is paramount in any MRP system. The accuracy of the information fed into the system determines the reliability of output it generates. If the data regarding inventory levels, supplier lead times, or production schedules is inaccurate, the MRP will produce flawed forecasts and recommendations. Poor data integrity can lead to overproduction or stockouts, both of which entail significant costs. Therefore, the process should begin with thorough data audits. Organizations must ensure that existing data is clean and reliable before integrating it into the MRP system. Continuous monitoring and regular updates are also necessary to maintain data integrity over time.
User Resistance and Change Management
User resistance is another significant barrier that organizations face when implementing MRP systems. Change can be uncomfortable, and employees may fear that new systems will disrupt their routines or threaten their job security. Management must proactively address these concerns by involving users in the process right from the start. Training and support are essential components of change management. Providing comprehensive training helps users feel competent and confident in using the new system, bridging the gap between existing and new practices. Moreover, open lines of communication about the reasons for the change can help ameliorate tensions and gain buy-in from the team.
Cost Implications
Implementing an MRP system can have significant financial implications. Beyond just the software costs, organizations must account for training, potential downtimes during the transition, and ongoing system maintenance. It is important to perform a comprehensive cost-benefit analysis prior to implementation. This analysis should include potential savings from improved efficiency and inventory management. Additionally, organizations must consider the hidden costs that may arise, such as employee resistance or data integration issues. Planning for these costs ensures more informed decision-making and strategy alignment with business goals.
"Understanding these challenges lays the groundwork for a successful MRP implementation, which, in turn, can lead to greater operational excellence."
In summary, addressing challenges such as data integrity, user resistance, and cost implications is crucial for the successful implementation of MRP systems. Organizations devoted to overcoming these hurdles will better position themselves for the benefits that a robust MRP system can deliver.
Future Trends in MRP Systems
Modern enterprises are navigating a rapidly changing landscape. It is crucial for organizations to stay updated on Future Trends in MRP Systems in order to remain competitive. The integration of advanced technology impacts how manufacturers conduct operations, enhance productivity, and streamline processes. This section will detail significant trends affecting MRP systems, focusing on integrating artificial intelligence, cloud-based solutions, and data analytics.
Integration with Artificial Intelligence
The incorporation of artificial intelligence (AI) into MRP systems can revolutionize manufacturing processes. AI aids in automating repetitive tasks, improving decision-making, and predicting demand with higher accuracy. When AI algorithms analyze historical data, they can identify patterns that help in inventory management and production scheduling.
This not only enhances efficiency but also reduces waste, making operations leaner. Additionally, AI can optimize supply chain decisions by delivering real-time insights. Such capabilities lead to reductions in lead times and improved customer satisfaction. The shift towards AI integration represents a substantial evolution, ensuring that MRP systems provide strategic advantage.
Cloud-Based Solutions
Cloud-based MRP systems are increasingly favored in the industry. These platforms offer flexibility and scalability that on-premise solutions often lack. With cloud technologies, manufacturers can access critical data from anywhere, promoting a more collaborative environment.
Backup and recovery become simpler, safeguarding data integrity. Furthermore, cloud systems typically require lower upfront costs, making them accessible to small and medium businesses. The continuous updates and maintenance performed by cloud service providers also relieve internal IT resources from routine tasks, allowing focus on more strategic initiatives. This trend highlights the shift toward agile practices in the manufacturing sector.
Data Analytics and Decision Support
Data analytics play a vital role in enhancing the capabilities of MRP systems. Businesses can collect and analyze vast amounts of data to gain critical insights. These insights can improve forecasting accuracy, identify inefficiencies, and highlight opportunities for cost savings.
MRP systems integrate with analytics tools to provide dashboards and reports that real-time info on key performance indicators. The resulting decision support enhances managersโ ability to react promptly to market dynamics. In addition, predictive analytics can further improve demand planning and resource allocation, thus driving operational excellence.
The Future of MRP Systems hinges on technology adaptations that enhance operational efficiency. As companies adopt these trends, the potential for improved supply chain management expands significantly.
End
In this article, we explored the various facets of Material Requirements Planning (MRP) systems, emphasizing their crucial role in the manufacturing sector. The examination ranged from understanding what MRP systems are to the future trends that may shape their evolution.
Recap of Key Points
To ensure clarity and retention, it is essential to recap the main points discussed:
- Definition and Significance: MRP systems are vital for streamlining production processes. They enhance efficiency, improve resource allocation, and contribute to cost management.
- Key Components: Essential elements such as the Bill of Materials, Master Production Schedule, and Inventory Management are fundamental in MRP systems.
- Types of Systems: Different variations like MRP I, MRP II, and ERP offer various capabilities and functionalities tailored to distinct business needs.
- Implementation Challenges: Challenges such as data integrity issues, user resistance, and associated costs must be managed carefully for successful adoption.
- Future Trends: Integrating AI, leveraging cloud solutions, and utilizing data analytics are set to redefine how MRP systems function and contribute to manufacturing efficiency.
Strategic Recommendations
Based on the insights gathered, several strategic recommendations can enhance the implementation and effectiveness of MRP systems:
- Evaluate Specific Needs: Organizations should assess their unique operational challenges and requirements before selecting an MRP solution.
- Invest in Training: Providing comprehensive training for users will mitigate resistance and improve system utilization.
- Focus on Data Integrity: Regular audits and data validations should be instituted to maintain accuracy and reliability within the MRP software.
- Leverage Analytical Tools: Utilize data analytics to derive actionable insights, helping debug production bottlenecks and improve decision-making processes.
- Explore AI Integration: Embrace artificial intelligence capabilities that can automate routine tasks and offer predictive analysis to stay ahead in the competitive landscape.
By considering these strategic recommendations, manufacturing enterprises can fully leverage MRP systems for improved operational efficiency and enhanced competitive positioning in the market.