CNC Tool Management Software: Boosting Manufacturing Efficiency
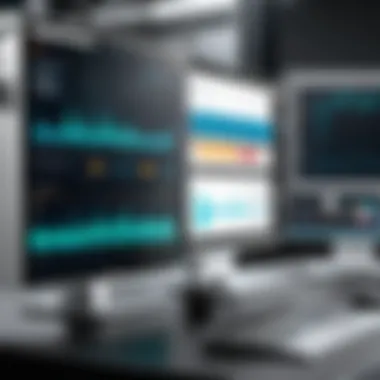
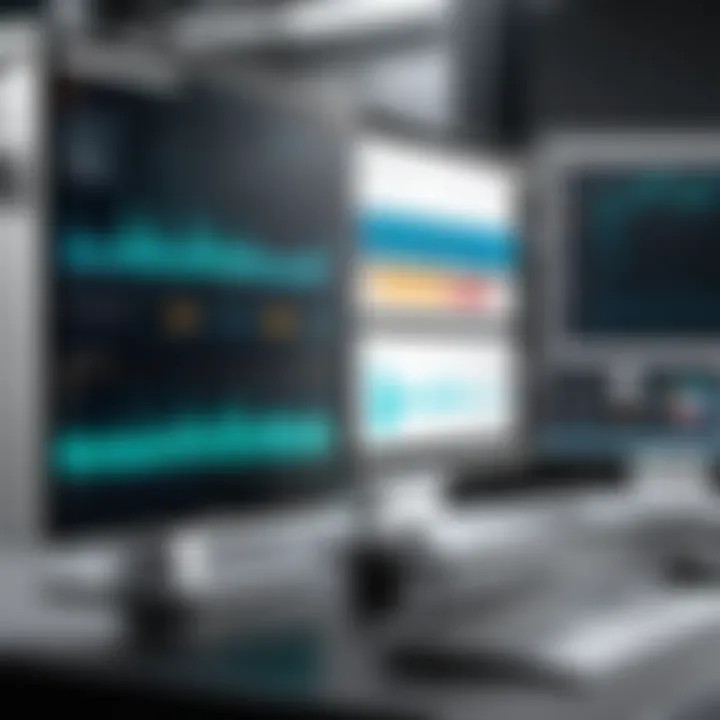
Intro
In the realm of manufacturing, maintaining precision and efficiency is crucial for staying competitive. CNC tool management software plays a pivotal role in achieving these objectives. This section will outline the importance of such software in modern production environments, emphasizing its functionalities and benefits. As industries evolve, so do the intricacies of managing tools required for CNC operations. Decision-makers must grasp how these systems enhance productivity and streamline processes.
A robust CNC tool management software effectively manages inventory, tracks tool life cycles, and ensures optimal utilization of assets. It integrates easily with existing manufacturing systems, facilitating a seamless transition into more automated workflows.
This article aims to provide a comprehensive understanding of CNC tool management software, focusing on key components that assist industry professionals in their decision-making processes.
Prelims to CNC Tool Management Software
CNC tool management software plays a crucial role in enhancing efficiency and precision within modern manufacturing. This system is designed to streamline operations, reduce errors, and ultimately improve productivity. With the increasing complexity of manufacturing processes, the need for effective tool management becomes paramount. By automating various aspects of tool handling, businesses can focus more on their core competencies, minimizing the time spent on logistical issues.
One of the significant benefits of CNC tool management software is its capability to optimize inventory control. Manufacturers can track tool usage, schedule maintenance, and manage inventory levels more effectively. This not only conserves resources but also ensures that tools are readily available when needed. Lack of proper tool management can lead to delays in production and increased costs. Therefore, employing a dedicated tool management system is not merely a convenience; it is a strategic necessity.
The software enhances operational accuracy by providing real-time data on tool performance. Users can analyze wear and tear, forecasting when tools will need replacement or maintenance. This predictive capability means that decision-makers can avoid unexpected downtime, which is critical for maintaining production schedules.
Furthermore, integration capabilities with existing manufacturing systems, such as ERP and CAD/CAM software, allow for a seamless flow of information across platforms. This feature ensures that all relevant departments have access to up-to-date and accurate data, creating a more cohesive operational environment.
Efficient tool management is not just about tracking; it's about making informed decisions that can enhance the overall manufacturing process.
In summary, the introduction of CNC tool management software is essential for modern manufacturers who aim to remain competitive. It addresses core challenges in tool efficiency and inventory management, making it an indispensable asset in today's fast-paced manufacturing landscape.
Understanding CNC Technology
CNC technology is a cornerstone of modern manufacturing. It automates the control of machining tools through computer programming. This advancement is significant due to its ability to enhance precision, improve efficiency, and reduce human error in production processes. Understanding CNC technology is essential for manufacturers seeking to optimize operational effectiveness.
Definition and Overview of CNC
CNC stands for Computer Numerical Control. It refers to a system that automates the operation of machinery. Techniques involve programming code that dictates how equipment like lathes, mills, and routers operate. In essence, CNC enables machines to interpret commands from a computer, facilitating intricate manufacturing tasks with exceptional accuracy. This technology allows for complex designs and ensures consistent output quality, making it invaluable in sectors that prioritize precision, such as aerospace, automotive, and medical.
Common Applications of CNC in Manufacturing
CNC technology finds its application across various manufacturing domains. Some common applications include:
- Aerospace Component Manufacturing: Precision is paramount in aerospace, and CNC machining helps produce parts that meet tight tolerances.
- Automotive Parts Production: From engine components to intricate interior designs, CNC allows for a high level of customization and quality assurance in automobile production.
- Medical Devices Fabrication: The medical industry relies on CNC for creating devices that require high precision, such as surgical tools and prosthetics.
- Furniture Production: Custom furniture design and production can easily be achieved through CNC, allowing for unique shapes and designs that are both functional and aesthetic.
"CNC technology revolutionizes manufacturing by ensuring a seamless blend of creativity and precision in product design."
Adopting CNC technology can lead to substantial improvements in productivity and product quality. As manufacturers continue to explore its potential, understanding the nuances of CNC is vital for decision-making leaders in the industry.
The Importance of Tool Management in CNC
Effective tool management is crucial for CNC manufacturing operations. The precision and efficiency of a production line heavily rely on how well tools are managed. Inaccuracies and tool mishandling can lead to significant production delays and increased costs. Adequately managed tools ensure that the CNC machines operate at optimal efficiency.
By streamlining processes, tool management minimizes waste and enhances productivity. Tools are expensive, and their efficient use can lead to reduced operational costs. Therefore, investing in robust tool management practices is necessary for sustaining competitiveness in todayβs market.
Challenges of Manual Tool Management
Manual management of tools often introduces various challenges that can hinder performance and productivity. First, the tracking system is prone to human error. Workers may misplace tools or record incorrect information in logs. This can lead to tools being unavailable when needed, causing delays in manufacturing processes.
Another issue is limited visibility into tool usage and inventory. Without proper tracking, it becomes difficult to determine when a tool needs maintenance or replacement. This lack of proactive management can lead to tools failing during production, which produces costly downtimes. Moreover, manual processes often require significant labor hours for tracking and replacing tools, further increasing operational costs.
Lastly, there is a significant reliance on employee knowledge. If key staff members leave or if there are staffing changes, valuable information about tool management may be lost. This creates gaps in efficiency and can lower the overall performance of the manufacturing system.
Benefits of Automated Tool Management
Automating tool management presents several advantages that are notable in any manufacturing environment. First, automation reduces the likelihood of human error. Systems designed specifically for tool management improve accuracy in tracking and inventory assessments. This leads to fewer production disruptions caused by misplaced or forgotten tools.
Subsequently, automated tools help monitor the condition of the tools regularly. Alerts can be issued when maintenance is due or tools are nearing their end of life. Proper maintenance enhances tool lifespan and performance, ultimately decreasing costs over time. This proactive approach can also support inventory control by automatically adjusting records after tool usage.
Furthermore, it allows employees to focus on higher-value tasks rather than menial tracking work. This shift can lead to improved morale and job satisfaction. Effective use of human resources, combined with automated systems, creates a streamlined workflow that can significantly boost productivity.
"The integration of automated tool management can unlock immense benefits, from minimizing human error to optimizing inventory control."
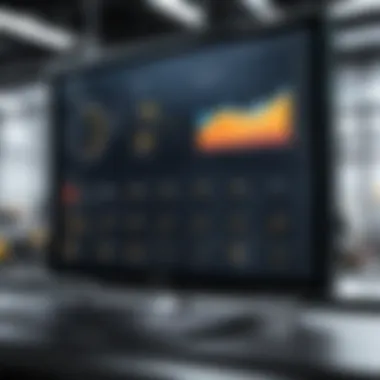
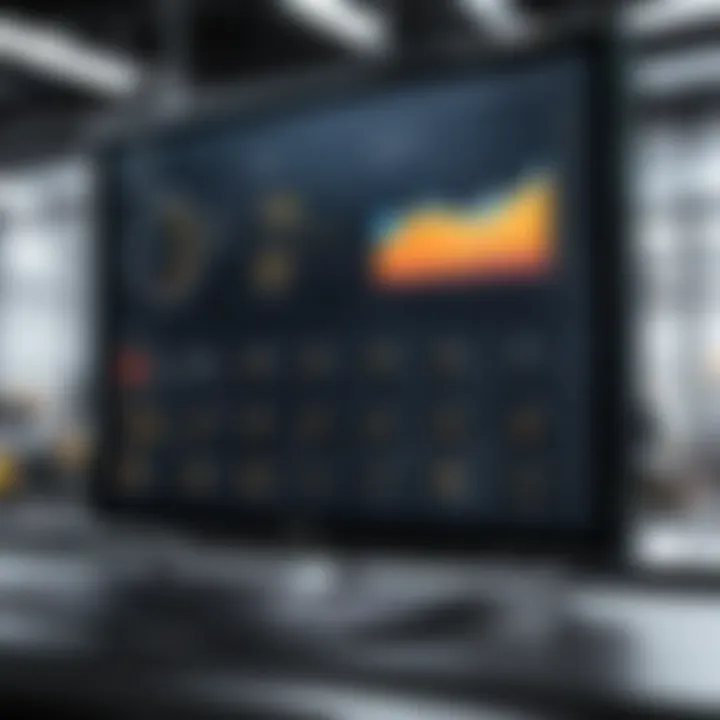
Core Features of CNC Tool Management Software
CNC tool management software plays a critical role in enhancing precision and efficiency in manufacturing. Understanding the core features of such software helps stakeholders make informed decisions. This section delves into vital functionalities, examining why they matter for management and operation. Each feature contributes to streamlining processes, reducing errors, and improving productivity.
Inventory Tracking and Control
A fundamental aspect of CNC tool management software is inventory tracking and control. This feature enables users to monitor tool availability in real-time. Accurate inventory management prevents production delays caused by missing tools. It keeps track of tool usage frequency, conditions, and locations, which ultimately aids in maintaining an effective supply chain.
Moreover, advanced tracking allows for automatic reordering of tools when stocks fall below a certain level. This reduces downtime significantly, allowing manufacturers to operate more smoothly. Proper inventory control also helps in minimizing excess inventory costs, driving overall efficiency.
Tool Lifecycle Management
Tool lifecycle management encompasses the entire lifespan of a tool, from acquisition to disposal. The software monitors usage patterns, service records, and wear rates. By analyzing this data, organizations can predict when tools require maintenance or replacement. Such foresight is essential because it helps in preventing unexpected failures during production, which can be costly.
Efficient lifecycle management leads to less waste of resources and time. Moreover, it ensures that only tools in optimal condition are utilized. By focusing on the performance of tools, manufacturers can achieve greater precision in their operations, which is paramount in competitive markets.
Integration with CNC Machines
For CNC tool management software to be effective, integration with CNC machines is paramount. This feature allows for seamless data exchange between the software and machinery. When tools are managed in conjunction with machine operations, it greatly enhances the accuracy of setups and adjustments.
Effective integration can lead to a streamlined workflow, helping to minimize the chance of errors. Users can access real-time data on tool status, cutting conditions, and other operational parameters. This not only boosts production efficiency but also helps in achieving higher quality outputs, effectively meeting stringent specifications.
Efficient integration yields better precision in CNC operations, ultimately benefiting output quality and resource management.
Understanding these core features emphasizes the significance of CNC tool management software. With proper implementation, manufacturers can harness the full potential of these systems, ensuring enhanced performance and minimizing operational challenges.
User Accessibility and Interface Design
The effectiveness of CNC tool management software relies heavily on user accessibility and interface design. Both elements play a crucial role in ensuring that the software can be utilized efficiently, facilitating smooth operations in a manufacturing environment. The complexity of functionalities offered by such software should not obstruct users from achieving their goals quickly and intuitively.
User Role Management
User role management is essential to ensure that the right individuals have access to the functionalities they need without compromising security. In a manufacturing setup, different roles require varied permissions. For example, administrators need comprehensive access to configure systems, while machine operators may need limited yet specific permissions for their tasks.
Implementing an effective user role management system includes:
- Customizable Roles: Organizations should be able to tailor role definitions based on operational needs.
- Access Controls: Setting strict boundaries ensures that sensitive data and critical functions are available only to authorized personnel.
- Audit Trails: It is crucial for compliance; tracking user actions can help in identifying misuse or errors, leading to quicker resolutions.
The ability to manage user roles effectively results in not only enhanced security but also increased productivity. Employees can focus on their tasks without confusion over their permissions or introduced obstacles in their workflow.
System Usability and Navigation
System usability and navigation are integral to the user experience within CNC tool management software. If employees struggle to navigate the interface, it can lead to frustration and inefficiency. A well-designed interface allows for easy workflows and minimizes the learning curve.
Key components of usability and navigation include:
- Intuitive Layout: Clear categorization of tools and functionalities allows users to find what they need swiftly.
- Responsive Design: The software should perform seamlessly across different devices. Whether on a desktop or tablet, users should get a uniform experience.
- Comprehensive Search Functionality: This feature allows users to locate tools or functions quickly, reducing time spent on searching.
- Feedback Mechanism: Users should have the capability to submit feedback or report issues easily. This feedback is vital for ongoing improvements.
Integration with Existing Systems
Integration with existing systems forms a crucial component of CNC tool management software. Without seamless integration, the benefits of tool management systems can be significantly diminished. It is essential for organizations to ensure that the software aligns well with their pre-existing operational frameworks.
One significant aspect of integration is how it affects data flow across different platforms. When CNC tool management software interfaces effectively with other systems, it allows for real-time data exchange. This capability enhances accuracy in inventory tracking and tool management while reducing human error. Moreover, interconnected systems lead to enhanced reporting capabilities. This improved data visibility aids decision-makers in monitoring performance and resource allocation more effectively.
Enterprise Resource Planning (ERP) Integration
Integrating CNC tool management software with an organization's Enterprise Resource Planning (ERP) system is vital. ERPs serve as the backbone for many manufacturing processes, encompassing modules for finance, HR, supply chain, and production. When CNC tool management software synchronizes with ERP systems, it provides a holistic view of operations.
Such integration allows for:
- Streamlined Operations: Information flows smoothly between tools and production, reducing delays in production cycles.
- Enhanced Forecasting: Data regarding tool usage can help predict future needs accurately, leading to better inventory management.
- Cost Reduction: By aligning tool management with financial oversight, companies can identify cost-saving opportunities and manage budgets more efficiently.
Challenges can arise in ensuring compatibility and data consistency between different systems. Organizations must prioritize selecting software solutions that offer robust integration capabilities with their existing ERP systems.
Compatibility with CAD/CAM Systems
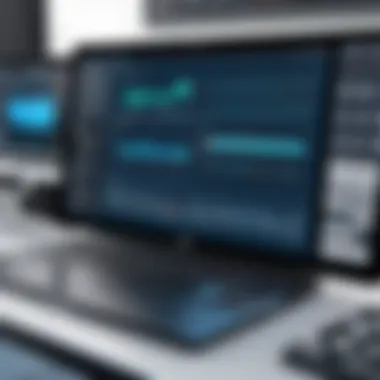
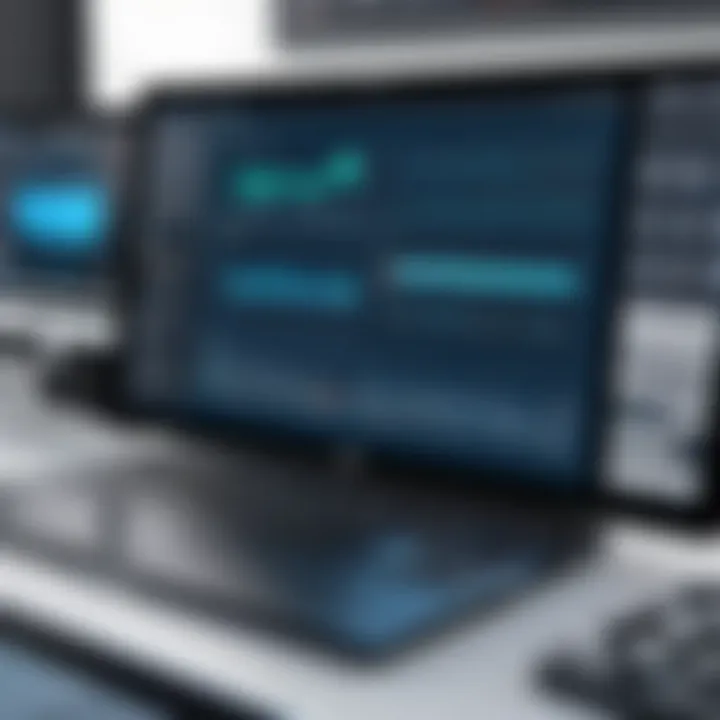
Compatibility with Computer-Aided Design (CAD) and Computer-Aided Manufacturing (CAM) systems stands as an equally important consideration. CAD/CAM software is instrumental in designing products and controlling the manufacturing process. Therefore, tool management software must align with these platforms for effective implementation.
The benefits of this compatibility include:
- Improved Design Efficiency: Quick access to tools and inventory data results in fewer interruptions during the design process, allowing engineers to focus on innovation.
- Enhanced Production Quality: Accurate tool data ensures that the right tools are used for the correct applications, ultimately improving the quality of the finished product.
- Faster Time to Market: A streamlined process from design to production reduces the time required to bring products to market.
Market Trends and Innovations
In the realm of CNC tool management software, understanding market trends and innovations is essential for businesses aiming to maintain a competitive edge. Such software continuously adapts to the evolving landscape of manufacturing technology, making it imperative to be aware of current developments. The integration of emerging technologies not only enhances operational efficiency but also improves precision in machining processes. Consequently, companies that stay current with these trends gain advantages in productivity and quality compared to their competitors.
Emerging Technologies in Tool Management
The advent of intelligent systems and automation has transformed the landscape of tool management. Technologies such as machine learning, Internet of Things (IoT), and big data analytics play pivotal roles in shaping modern CNC applications. These technologies enable real-time monitoring of tools, predicting wear and failure points, thus optimizing maintenance schedules. For instance, machine learning algorithms can analyze historical data to identify patterns, allowing companies to prevent tool failure before it occurs.
This predictive capability is vital for minimizing downtime and reducing operational costs. Furthermore, automated inventory systems linked with IoT devices ensure accurate tracking of tool use and availability. By harnessing these advancements, firms can maintain tighter control over their tool assets, promoting a more efficient production cycle.
Shift Towards Cloud-Based Solutions
Cloud-based solutions have gained prominence in CNC tool management, offering flexibility and scalability that traditional technologies cannot provide. Such platforms facilitate centralized data access, allowing different stakeholders to make informed decisions based on real-time information. Users can quickly access tool inventories, manage lifecycle data, and oversee productivity metrics from virtually anywhere.
One significant benefit of cloud solutions is their cost-effectiveness. Companies avoid high upfront costs associated with maintaining on-premises infrastructures. Instead, they can subscribe to services that fit their needs, which can be adjusted as their operations grow.
Furthermore, cloud-based tools enhance collaboration across teams. As data is stored in the cloud, information can be rapidly shared among engineers, managers, and operators. This seamless flow of data reduces misunderstandings and accelerates response times when adjustments are necessary.
Cloud technologies not only streamline processes but also improve agility in manufacturing, helping companies adapt swiftly to market changes.
By keeping up with these trends and innovations, businesses can not only ensure effective tool management but also leverage technology to make informed strategic decisions.
Challenges in Implementing CNC Tool Management Software
Implementing CNC tool management software can greatly enhance the efficiency and precision of manufacturing workflows. However, the path towards full integration of such systems is not always smooth. The challenges faced can not only impact the deployment of the software but also its effectiveness in achieving the intended goals of improved productivity and inventory management. Understanding these challenges is essential for stakeholders who are considering adopting CNC tool management solutions.
Data Security and Privacy Concerns
One of the foremost challenges in adopting CNC tool management software revolves around data security and privacy. As manufacturing processes increasingly rely on interconnected systems, the volume of sensitive data shared across platforms grows. This data includes technical specifications, employee access levels, and operational trade secrets.
The risk of data breaches can expose enterprises to significant financial losses and loss of competitive advantage. Moreover, regulations like GDPR have imposed stringent guidelines on data handling, necessitating adherence to compliance standards, which can complicate the integration of such software.
To mitigate these risks, manufacturing organizations should prioritize selecting software solutions with robust data security features. These include end-to-end encryption, secure user authentication, and regular security audits. By addressing these concerns early, companies can ensure a smoother implementation process.
Resistance to Change Among Staff
Another considerable hurdle in the implementation of CNC tool management software is the potential resistance to change from staff members. Employees may be accustomed to traditional methods of tool management, often relying on manual tracking and inventory logs. Transitioning to an automated system may create feelings of uncertainty or anxiety about job security and changes to established routines.
Training and development programs play a vital role in overcoming this resistance. By investing time in training sessions focused on the benefits and functionalities of the new software, organizations can empower employees to embrace change. In addition, involving staff in the selection and implementation process can improve acceptance and help in addressing their concerns.
Effective change management strategies have been proven to facilitate smoother transitions in organizations. Highlighting how the software enhances job efficiency and reduces repetitive tasks can help alleviate fears and promote a positive outlook on the integration of CNC tool management systems.
Evaluating Software Solutions
Assessing CNC tool management software is crucial for ensuring that the selected tools meet the specific needs of a manufacturing operation. This evaluation process includes analyzing various aspects, such as usability, integration capabilities, and overall performance. A thorough evaluation helps decision-makers identify the best fit for their organization while also aligning with strategic goals.
Criteria for Selection
When selecting CNC tool management software, several criteria should inform the decision-making process:
- Functionality: The software must cover all essential features like inventory management, tool tracking, and performance analytics. Evaluators must ensure that the software supports the specific requirements of their machining process.
- Ease of Use: User-friendly interfaces promote efficient operation. When employees can navigate the software without extensive training, this translates to greater productivity.
- Integration Capability: It is important to ensure the software can seamlessly integrate with existing systems such as ERP or CAD/CAM. Compatibility reduces disruptions during implementation and leverages current investments in technology.
- Scalability: As businesses grow, the software should adapt to increase demands. Evaluating software for its capacity to scale can save time and costs in the future.
- Support and Maintenance: Reliable technical support and regular updates are essential for ongoing usage. It is beneficial to examine the vendor's track record in delivering service and updates.
Cost Considerations
The cost of CNC tool management software can vary significantly based on features, vendor reputation, and support services. Here are some important factors to consider regarding cost:
- Initial Investment: This includes purchase or subscription costs, installation fees, and potential hardware upgrades needed to support the software.
- Operating Expenses: Decide whether the software operates effectively within the budget for maintenance, training, and updates. Unanticipated costs can impact overall spending.
- Return on Investment (ROI): Evaluate how the software can enhance productivity and reduce waste. Analyzing ROI provides insight into the long-term value of the software.
- Hidden Costs: Consider training expenses and potential productivity loss during the transition phase. Omitting these factors can lead to underestimating total costs.
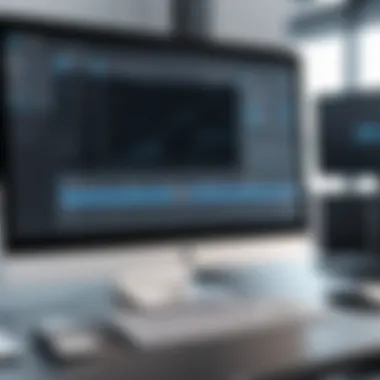
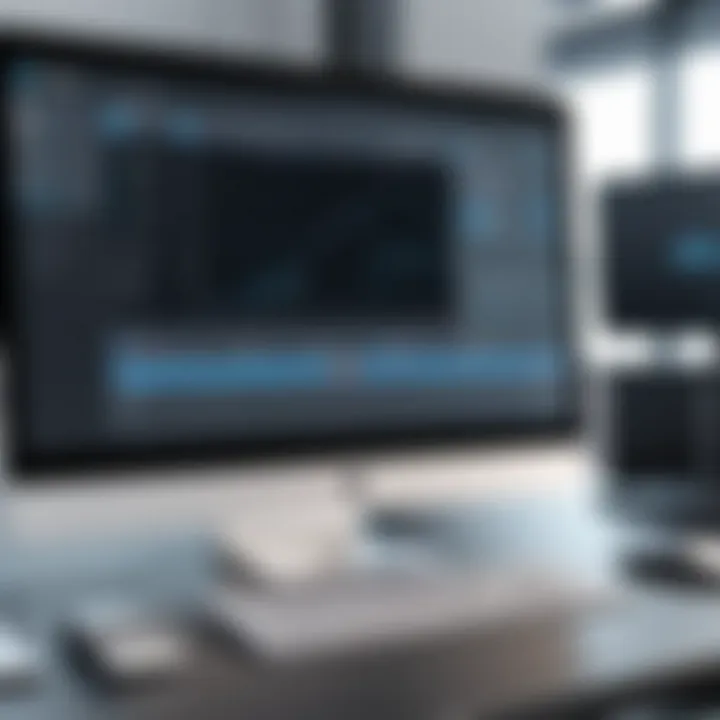
"An informed choice in software selection is critical for maximizing productivity and minimizing operational disruptions."
The evaluation of software solutions is not merely a procedural task; it is a strategic decision that can greatly affect the efficiency and precision of manufacturing processes. A systematic approach will yield better outcomes for manufacturers aiming to enhance their operational capabilities.
User Feedback and Case Studies
User feedback and case studies provide deep insight into the efficacy of CNC tool management software. They illustrate real-world applications and the tangible benefits that organizations can achieve by implementing such systems. Collecting information from users and analyzing different case studies allows decision-makers to understand how well a software solution meets operational needs.
In the realm of CNC tool management, user feedback is critical. It helps potential users and stakeholders discern the strengths and weaknesses of various software options. Specifically, positive feedback often emphasizes improved precision, efficiency, and inventory control, while negative feedback may highlight integration issues or a steep learning curve. This information can guide organizations in making informed decisions about which software best fits their unique requirements.
Case studies serve as concrete examples of how organizations have successfully integrated CNC tool management systems into their workflows. They illustrate before-and-after scenarios, showcasing metrics such as reduced downtime, increased tool use efficiency, and enhanced product quality. By examining these examples, prospective users can envision the benefits that could result from a similar implementation.
Insights from Industry Professionals
Industry professionals often provide valuable insights into the impact of CNC tool management software on their operations. They discuss various aspects such as the challenges faced during and after the transition to automated systems, the learning process for staff, and the overall outcome.
Common themes from these professionals highlight the need for a user-friendly interface, effective training programs, and responsive customer support. Many emphasize that the active involvement of staff in the selection process leads to better acceptance of the new system. Moreover, experienced users often advocate for features that streamline communication and collaboration among teams, as these elements can significantly affect the operational success of tool management initiatives.
Case Studies of Successful Implementations
Case studies present a clear narrative of success when implementing CNC tool management software. One notable example is a large automotive manufacturer that faced challenges in managing its extensive tool inventory. Before adopting a dedicated CNC tool management system, the company struggled with tool tracking and often experienced delays due to misplaced or unavailable tools. After the implementation, the firm reported a 30% reduction in tool-related downtime. They achieved this through robust inventory tracking features, enabling real-time monitoring of tool usage and availability.
Another case involves a small machining company that integrated cloud-based CNC tool management software. Initially hesitant about the investment, the firm ultimately recognized significant savings in operational costs. With cloud access, employees were able to manage inventory remotely, which facilitated easier updates and corrections. This led to a 25% improvement in turnaround time for their manufacturing projects.
These real-world examples emphasize the potential of CNC tool management software. They reveal the profound impact that effective software can have on precision and overall manufacturing efficiency. By examining different implementations, it becomes clear that investing in technology enhances productivity and streamlines management processes.
Future Prospects of CNC Tool Management Software
As industries advance towards greater efficiency and precision, CNC tool management software stands as a pivotal pillar for sustaining competitiveness. This section delves into the future prospects of CNC tool management software, emphasizing its anticipated growth, transformational capabilities through technological integration, and the comprehensive benefits it proffers.
Predicted Market Growth
The CNC tool management software market is projected to experience robust growth in the coming years. Analysts estimate a compounded annual growth rate (CAGR) of over 10% through the next five years. This growth can be attributed to several factors:
- Increased Demand for Automation: Manufacturers prioritize automation to enhance productivity and reduce operational costs. CNC tool management software plays a crucial role in automating tool inventory and tracking processes.
- Focus on Precision Manufacturing: As industries like aerospace and automotive require higher levels of precision, tool management software offers essential data analytics and monitoring to maintain high standards.
- Shift Towards Cloud Solutions: More manufacturers adopt cloud-based systems for accessibility and enhanced collaboration among teams, boosting software demand.
These elements not only signify increasing market potential but also highlight a shift in how manufacturers approach CNC processes. Thus, stakeholders must evaluate their systems to capitalize on this growth effectively.
Advancements in AI and Automation
Artificial Intelligence and automation are taking center stage in CNC tool management software's future, reshaping its functionalities and capabilities.
- Predictive Maintenance: AI can assist in predicting when a tool will need maintenance or replacement, reducing downtime and improving productivity. This proactive approach minimizes disruptions in manufacturing processes.
- Enhanced Decision-Making: Utilizing machine learning algorithms, software can analyze historical data to aid managers in making informed decisions regarding tool usage and inventory levels.
- Real-Time Data Processing: Advancements in automation enable real-time tracking and processing of tool data, allowing organizations to respond swiftly to production changes.
"The integration of AI into CNC tool management software not only enhances operational efficiency but also transforms data into actionable insights."
The incorporation of AI and automation into CNC tool management software illustrates a future where manufacturers are equipped with sophisticated tools that cater to their evolving needs. As these technologies mature, they are likely to deliver enhanced precision and refined efficiency, setting the stage for a new era in manufacturing.
In summary, understanding the future prospects of CNC tool management software is essential for organizations striving for excellence. By addressing market growth and embracing advancements in AI and automation, businesses can position themselves to navigate the complexities of modern manufacturing with greater agility.
Closure
The significance of CNC tool management software cannot be overstated in the contemporary manufacturing landscape. This software serves as a critical cornerstone for ensuring precision and efficiency through effective tools management. As CNC technology continues to evolve and integrate deeper into manufacturing processes, the necessity for robust tool management becomes clear.
Importance of Precision and Efficiency
Precision in manufacturing is paramount. Any slight deviation can lead to inefficiencies and product defects. CNC tool management software provides a systematic approach to manage tools, ensuring that they are ready and optimized for use. This guarantees minimal downtime and maximizes productivity.
Streamlining Operations
The tools in a manufacturing environment require meticulous monitoring. By automating inventory tracking and lifecycle management, companies can significantly reduce human error. Streamlining these operations directly influences the overall efficiency, allowing staff to focus on higher-level tasks rather than getting bogged down by manual tracking.
Effective tool management is not just about tools. It's about enhancing the entire production cycle.
Making Informed Decisions
Investing in CNC tool management software leads to informed decision-making. With accurate data at hand, businesses can predict tool wear, necessary replacements, and potential scheduling conflicts. This foresight is invaluable, allowing organizations to allocate resources wisely and plan for maintenance without disrupting production flow.
Future Outlook
The future of tool management is intertwined with advancements in technology, such as artificial intelligence and automation. As these technologies mature, they will refine how tool data is collected and analyzed, further enhancing precision and operational efficiency. Decisions made today regarding software selection will affect long-term operational capabilities.